The energy required for pyrolysis depends on several factors, including the scale of the plant, the type of feedstock, the desired temperature, and the efficiency of the process. For a middle-scale pyrolysis plant, approximately 500 kg of oil is needed as heating fuel, and about 20 kWh of electricity is consumed over a 20-22 hour process cycle. The energy requirements include heating the biomass and water to 500°C, evaporating water, supporting the endothermic pyrolysis reaction, and compensating for energy losses. Factors such as feedstock composition, moisture content, temperature, residence time, and particle size significantly influence the energy needs and outcomes of the pyrolysis process.
Key Points Explained:
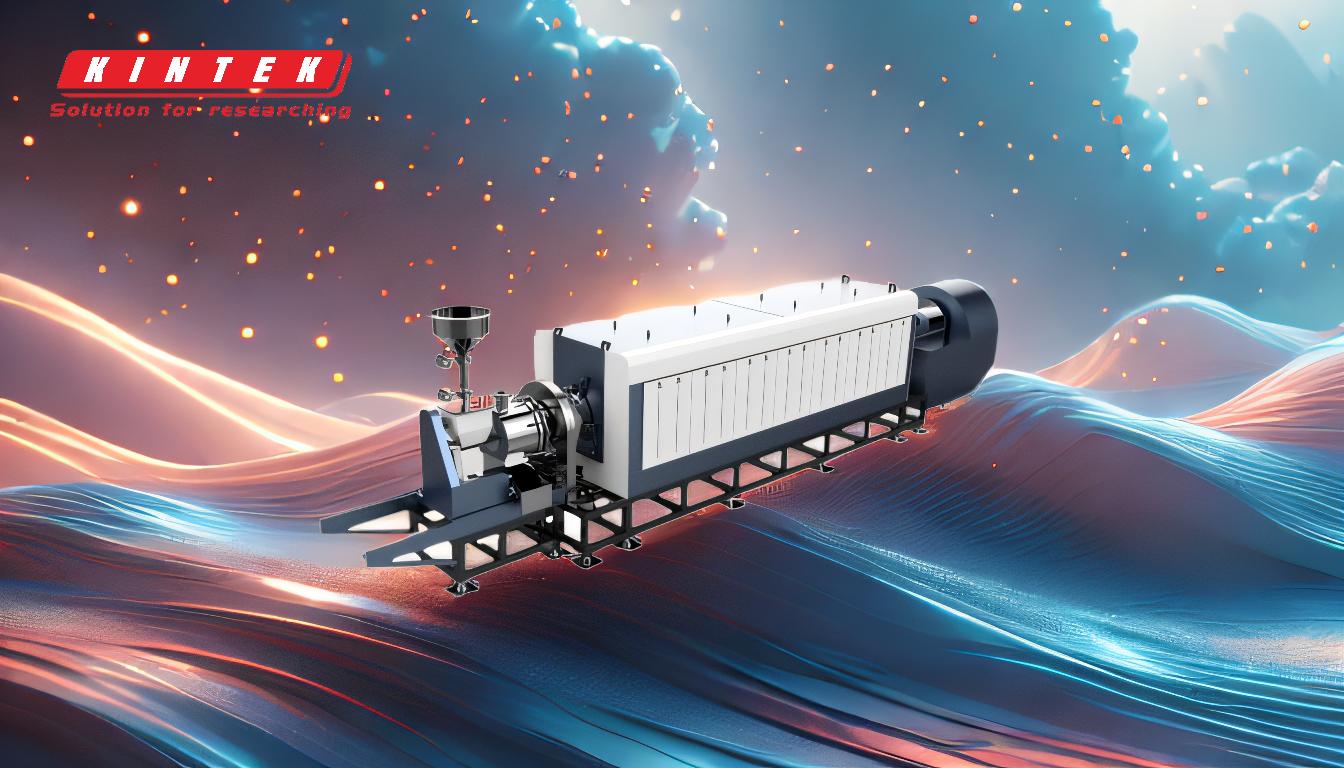
-
Energy Sources for Pyrolysis:
- Heating Fuel: For a middle-scale pyrolysis plant, around 500 kg of oil is required as a heating fuel. This fuel is used to generate the necessary heat for the pyrolysis process.
- Electricity: Approximately 20 kWh of electricity is consumed during the entire process, which includes feeding, pyrolysis, and discharging of final products.
-
Process Duration:
- The total process time from feeding to final product discharge is about 20-22 hours. This duration includes heating, pyrolysis, and cooling phases.
-
Energy Requirements:
- Heating Biomass and Water: The biomass and any water contained within it must be heated to 500°C. This is a significant energy requirement as it involves raising the temperature of the material to the point where pyrolysis can occur.
- Evaporating Water: Any moisture in the biomass must be evaporated at 100°C, which requires additional energy.
- Heating Water Vapor: After evaporation, the water vapor must be further heated from 100°C to 500°C.
- Endothermic Reaction: Pyrolysis is an endothermic process, meaning it requires energy input to break down the biomass into gas, liquid, and solid products.
- Energy Losses: Energy is also lost to the environment, and this loss must be compensated for to maintain the required process temperature.
-
Factors Influencing Energy Needs:
- Feedstock Composition: The type of biomass or waste material being pyrolyzed affects the energy requirements. Materials with higher moisture content or more complex structures may require more energy.
- Temperature: Higher temperatures generally increase the production of non-condensable gases but also require more energy.
- Residence Time: The time the material spends in the pyrolysis chamber affects the degree of thermal conversion and the energy needed.
- Particle Size: Smaller particles heat up more quickly and can lead to faster thermal decomposition, potentially reducing energy requirements.
-
Process Efficiency:
- The efficiency of the pyrolysis process is influenced by the composition of the waste flow and the extent to which the organic fraction can be degraded and converted into gas. This, in turn, affects the temperature, pressure, and other reactor settings, which are critical for optimizing energy use.
-
Simulation and Modeling:
- In some cases, the energy required for pyrolysis is modeled using software like AspenPlus. For example, heating a catalyst (modeled as sand) in a combustor operating at 900°C, which is then fluidized and used for heat exchange with the biomass, can be simulated to estimate energy requirements accurately.
-
Product Quality and Yield:
- The quality and yield of pyrolysis products are influenced by operating conditions such as temperature and residence time. Biomass properties, including moisture content, fixed carbon, and volatile matter, also play a role in determining the energy needed for optimal product distribution.
In summary, the energy required for pyrolysis is a complex interplay of various factors, including the scale of the operation, the nature of the feedstock, and the specific conditions under which the process is carried out. Understanding these factors is crucial for optimizing energy use and improving the efficiency of the pyrolysis process.
Summary Table:
Factor | Impact on Energy Requirements |
---|---|
Feedstock Composition | Higher moisture content or complex structures increase energy needs. |
Temperature | Higher temperatures require more energy but increase non-condensable gas production. |
Residence Time | Longer residence times improve thermal conversion but raise energy consumption. |
Particle Size | Smaller particles heat faster, potentially reducing energy requirements. |
Process Efficiency | Optimized reactor settings and waste flow composition improve energy use efficiency. |
Energy Losses | Heat lost to the environment must be compensated, increasing overall energy needs. |
Ready to optimize your pyrolysis process? Contact our experts today for tailored solutions!