Hydraulic systems are critical components in various industries, and their maintenance frequency depends on factors such as usage intensity, operating conditions, and the quality of the system. Regular maintenance is essential to ensure optimal performance, prevent breakdowns, and extend the lifespan of the equipment. Typically, hydraulic systems require routine inspections, fluid checks, and component servicing at intervals ranging from weekly to annually, depending on the specific system and its application. Proactive maintenance, including monitoring for leaks, contamination, and wear, can significantly reduce the risk of unexpected failures and costly repairs.
Key Points Explained:
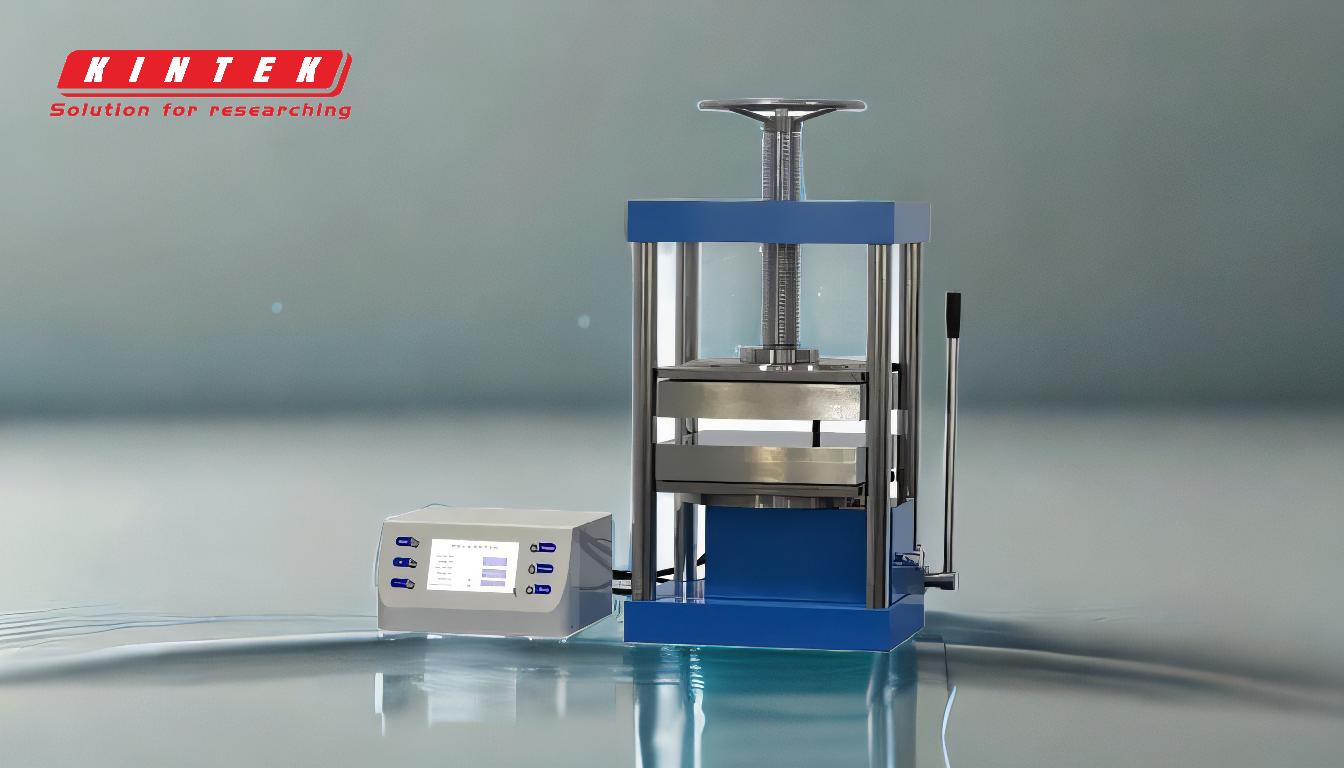
-
Factors Influencing Maintenance Frequency:
- Usage Intensity: Heavy-duty applications, such as construction or manufacturing, may require more frequent maintenance due to higher wear and tear.
- Operating Conditions: Systems operating in harsh environments (e.g., extreme temperatures or dusty conditions) need more frequent checks to prevent contamination and overheating.
- System Complexity: More complex systems with numerous components may require more detailed and frequent inspections.
-
Routine Maintenance Tasks:
- Fluid Checks: Hydraulic fluid should be checked regularly for proper levels, contamination, and degradation. Contaminated or degraded fluid can lead to system inefficiencies and damage.
- Filter Replacement: Filters should be inspected and replaced as needed to prevent contaminants from entering the system.
- Leak Inspection: Regularly check for leaks in hoses, seals, and connections, as leaks can lead to fluid loss and system failure.
- Component Lubrication: Ensure that all moving parts are adequately lubricated to reduce friction and wear.
-
Maintenance Intervals:
- Daily/Weekly: Basic checks, such as fluid levels and visual inspections for leaks or damage, should be performed frequently.
- Monthly: More detailed inspections, including filter checks and system performance evaluations, are recommended.
- Quarterly/Annually: Comprehensive maintenance, such as fluid replacement, component testing, and system calibration, should be conducted to ensure long-term reliability.
-
Proactive Maintenance Strategies:
- Condition Monitoring: Use sensors and diagnostic tools to monitor system performance and detect issues early.
- Preventive Maintenance Plans: Develop a maintenance schedule based on manufacturer recommendations and operational demands.
- Training and Documentation: Ensure that personnel are trained in proper maintenance procedures and that all maintenance activities are documented for future reference.
By adhering to a structured maintenance plan and addressing issues promptly, hydraulic systems can operate efficiently and reliably, minimizing downtime and repair costs.
Summary Table:
Maintenance Task | Frequency | Key Details |
---|---|---|
Fluid Checks | Daily/Weekly | Check levels, contamination, and degradation to prevent inefficiencies. |
Filter Replacement | Monthly | Inspect and replace filters to avoid system contamination. |
Leak Inspection | Weekly/Monthly | Regularly check hoses, seals, and connections for leaks. |
Component Lubrication | Monthly/Quarterly | Lubricate moving parts to reduce friction and wear. |
Comprehensive Checks | Quarterly/Annually | Conduct fluid replacement, component testing, and system calibration. |
Ensure your hydraulic systems run smoothly—contact us today for expert maintenance advice!