Evaporation during deposition is a critical process in thin-film fabrication, where source materials are transformed into vapor and then condensed onto a substrate to form a thin film. The process occurs in a vacuum to ensure the vapor particles travel directly to the substrate without interference. Various techniques and equipment, such as thermal evaporation, electron beam evaporation, and sputter deposition, are employed depending on the material and application. The choice of evaporation source, such as evaporation boats, crucibles, or filaments, also plays a significant role in the efficiency and quality of the deposition.
Key Points Explained:
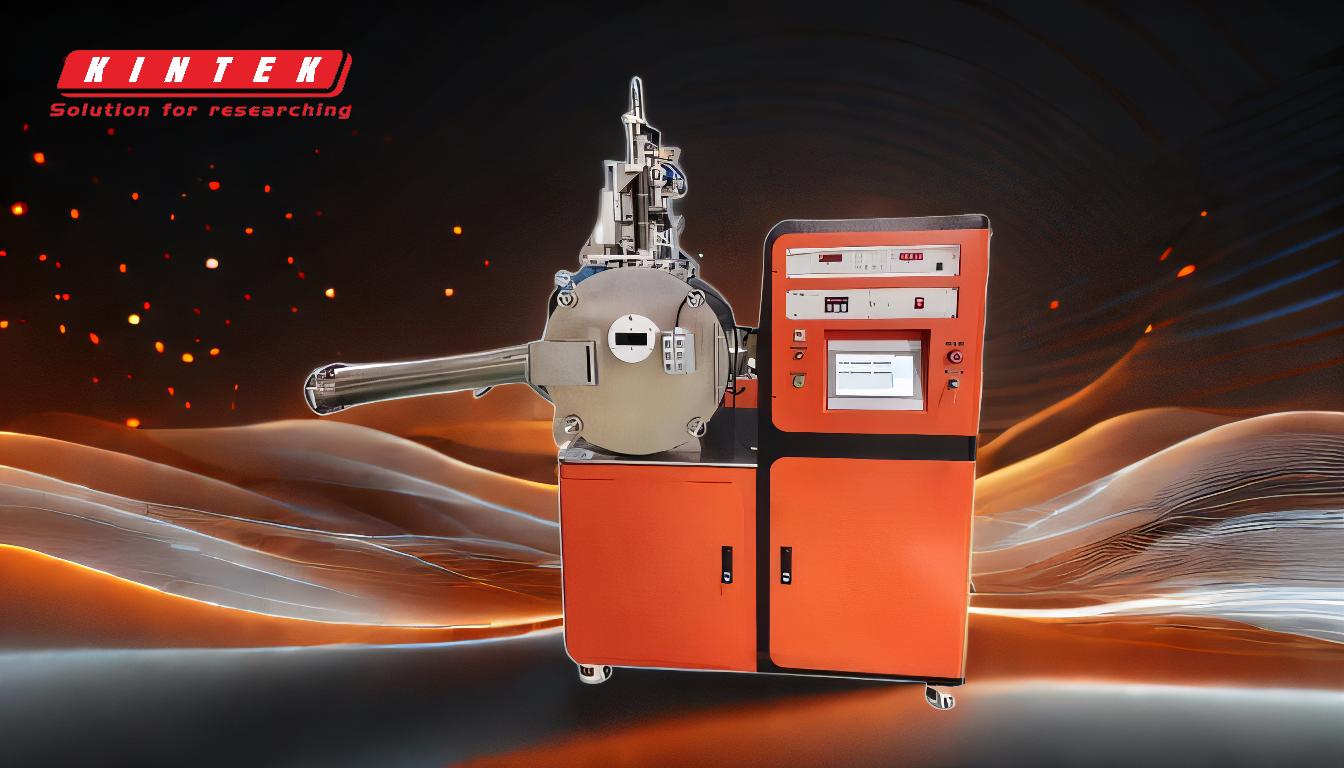
-
Basic Principle of Evaporation in Deposition:
- Evaporation involves heating a source material in a vacuum until it vaporizes.
- The vaporized particles travel directly to the substrate and condense back into a solid state, forming a thin film.
- This process is widely used in microfabrication and industrial applications like metalized plastic film production.
-
Types of Evaporation Sources:
- Evaporation Boats: Used for vaporizing solid materials, typically made of high-temperature-resistant materials like tungsten or molybdenum.
- Effusion Cells: Designed for liquid or gaseous materials, allowing controlled evaporation.
- Crucibles: Hold solid materials and are heated to vaporize the contents.
- Filaments: Resistive wires or foils that heat metals directly.
- Basket Heaters: Allow direct loading of source materials without a crucible, simplifying the process.
-
Evaporation Techniques:
- Thermal Evaporation: Involves heating the source material using resistive heating until it vaporizes. Suitable for materials with low melting points.
- Electron Beam Evaporation: Uses a high-energy electron beam to vaporize the material, ideal for high-melting-point materials.
- Sputter Deposition: Utilizes a plasma or ion beam to knock atoms off the source material, which then deposit onto the substrate.
- Laser Beam Evaporation: Employs a laser to vaporize the material, offering precise control.
- Arc Evaporation: Uses an electric arc to vaporize the source material, often used for hard coatings.
- Molecular Beam Epitaxy: A highly controlled technique for growing crystalline films layer by layer.
- Ion Plating Evaporation: Combines evaporation with ion bombardment to enhance film adhesion and density.
-
Process Conditions:
- The process occurs in a vacuum to minimize contamination and ensure the vapor particles travel directly to the substrate.
- The vacuum environment also prevents oxidation and other chemical reactions that could degrade the film quality.
-
Applications:
- Microfabrication: Used to create thin films for semiconductors, optical coatings, and sensors.
- Macro-Scale Productions: Includes applications like metalized plastic films for packaging and decorative purposes.
-
Advantages and Limitations:
- Advantages: High purity of deposited films, ability to deposit a wide range of materials, and precise control over film thickness.
- Limitations: Requires a vacuum environment, which can be costly and complex. Some techniques, like electron beam evaporation, may require specialized equipment.
By understanding these key points, one can appreciate the complexity and versatility of evaporation techniques in thin-film deposition, making it a cornerstone of modern manufacturing and technology.
Summary Table:
Aspect | Details |
---|---|
Basic Principle | Heating source material in a vacuum to vaporize and condense into thin films. |
Evaporation Sources | Boats, crucibles, filaments, effusion cells, basket heaters. |
Techniques | Thermal, electron beam, sputter, laser, arc, molecular beam epitaxy, ion plating. |
Process Conditions | Conducted in a vacuum to minimize contamination and ensure direct deposition. |
Applications | Microfabrication (semiconductors, sensors), macro-scale (metalized films). |
Advantages | High purity, precise thickness control, versatile material deposition. |
Limitations | Requires vacuum environment, specialized equipment, and higher costs. |
Discover how evaporation techniques can elevate your thin-film fabrication—contact our experts today!