PVD (Physical Vapor Deposition) coating is a highly advanced and versatile surface treatment technology that significantly enhances the durability, hardness, and wear resistance of materials. It operates at relatively low temperatures, reducing the risk of thermal damage to substrates, and produces thin, precise coatings that preserve the sharpness of tools and reduce cutting forces. PVD coatings are known for their high hardness, scratch resistance, and corrosion resistance, making them ideal for applications in cutting tools, jewelry, watches, and industrial components exposed to harsh environments. The process creates compressive stress during cooling, which prevents crack formation and expansion, further enhancing its suitability for demanding applications like interrupted cutting processes. Additionally, PVD coatings can replicate the appearance of expensive metals, offering aesthetic benefits without compromising durability.
Key Points Explained:
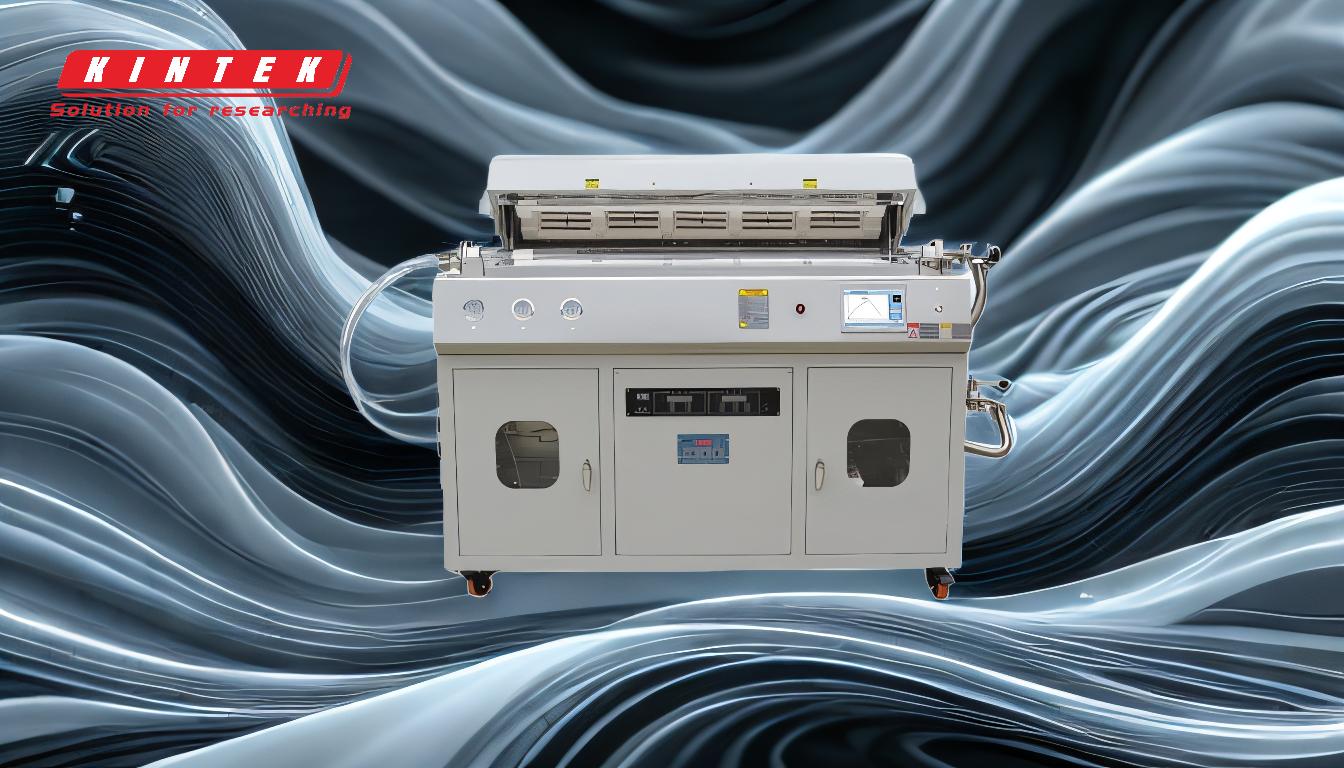
-
High Hardness and Wear Resistance:
- PVD coatings are known for their exceptional hardness, often exceeding that of traditional coatings like chrome. This makes them highly resistant to wear and abrasion, which is critical for cutting tools and industrial components subjected to heavy use. The hardness of PVD coatings ensures longer tool life and reduced maintenance costs.
-
Low-Temperature Process:
- PVD coating operates at temperatures around 500 °C, much lower than other coating methods. This minimizes the risk of thermal distortion or damage to the substrate, making it suitable for materials that cannot withstand high temperatures, such as high-speed steel (HSS) and certain plastics.
-
Thin and Precise Coatings:
- The coatings produced by PVD are extremely thin, typically ranging from 0.5 to 5 microns. This thinness preserves the sharpness of cutting tools and reduces cutting forces and heat generation during machining. The precision of PVD coatings also makes them ideal for applications requiring tight tolerances, such as fine blanking tools and optical components.
-
Compressive Stress Formation:
- During the cooling phase of the PVD process, compressive stress is formed within the coating. This stress helps prevent crack formation and expansion, making PVD coatings particularly suitable for interrupted cutting processes like milling, where tools are subjected to repeated impact and stress.
-
Corrosion and Oxidation Resistance:
- PVD coatings are highly resistant to corrosion and oxidation, making them ideal for use in harsh environments, such as coastal areas or industrial settings. This resistance ensures that coated components maintain their performance and appearance over time, even when exposed to moisture, chemicals, or extreme temperatures.
-
Aesthetic Versatility:
- PVD coatings can replicate the appearance of expensive metals like copper, brass, bronze, and gold, offering aesthetic benefits without the high cost or maintenance requirements of these materials. This makes PVD a popular choice for jewelry, watches, and decorative finishes, where both durability and visual appeal are important.
-
Suitability for Various Applications:
- PVD coatings are widely used in industries ranging from manufacturing to jewelry. They are ideal for cutting tools, plastic injection molding components, and optical coatings due to their precision and durability. Additionally, PVD coatings are suitable for both high-volume production and small batch manufacturing, offering flexibility and cost-effectiveness.
-
Enhanced Durability and Longevity:
- PVD coatings are four times harder than chrome, making them more resistant to scratches and wear. This durability ensures that coated components last longer, even in demanding applications. The longevity of PVD coatings reduces the need for frequent replacements, lowering overall production costs.
-
Environmental and Economic Benefits:
- The PVD process is performed under vacuum conditions, which minimizes environmental impact by reducing emissions and waste. Additionally, the durability and precision of PVD coatings contribute to lower production costs and faster turnaround times, making it an economically viable solution for various industries.
In summary, PVD coating is a powerful technology that enhances the performance, durability, and appearance of materials across a wide range of applications. Its unique combination of high hardness, low-temperature processing, and aesthetic versatility makes it a preferred choice for industries seeking advanced surface treatment solutions.
Summary Table:
Key Features | Details |
---|---|
Hardness | Exceeds traditional coatings like chrome; 4x harder than chrome. |
Wear Resistance | Highly resistant to abrasion, ensuring longer tool life. |
Temperature Tolerance | Operates at ~500 °C, minimizing thermal damage to substrates. |
Coating Thickness | Thin (0.5–5 microns), preserving tool sharpness and reducing cutting forces. |
Corrosion Resistance | Ideal for harsh environments like coastal or industrial settings. |
Aesthetic Versatility | Replicates expensive metals like gold, brass, and copper. |
Applications | Cutting tools, jewelry, watches, and industrial components. |
Upgrade your materials with PVD coating’s unmatched strength and durability—contact us today to learn more!