Magnetron sputtering is a versatile thin-film deposition technique that allows for the coating of various materials with precise control over thickness and uniformity. The thickness of the sputtered films can range from a few nanometers to several micrometers, depending on the application, target material, and process parameters. Factors such as target-substrate distance, ion energy, gas pressure, and temperature play a significant role in determining the final thickness and uniformity of the deposited film. This technique is widely used in industries requiring high-quality coatings, such as semiconductors, optics, and wear-resistant surfaces.
Key Points Explained:
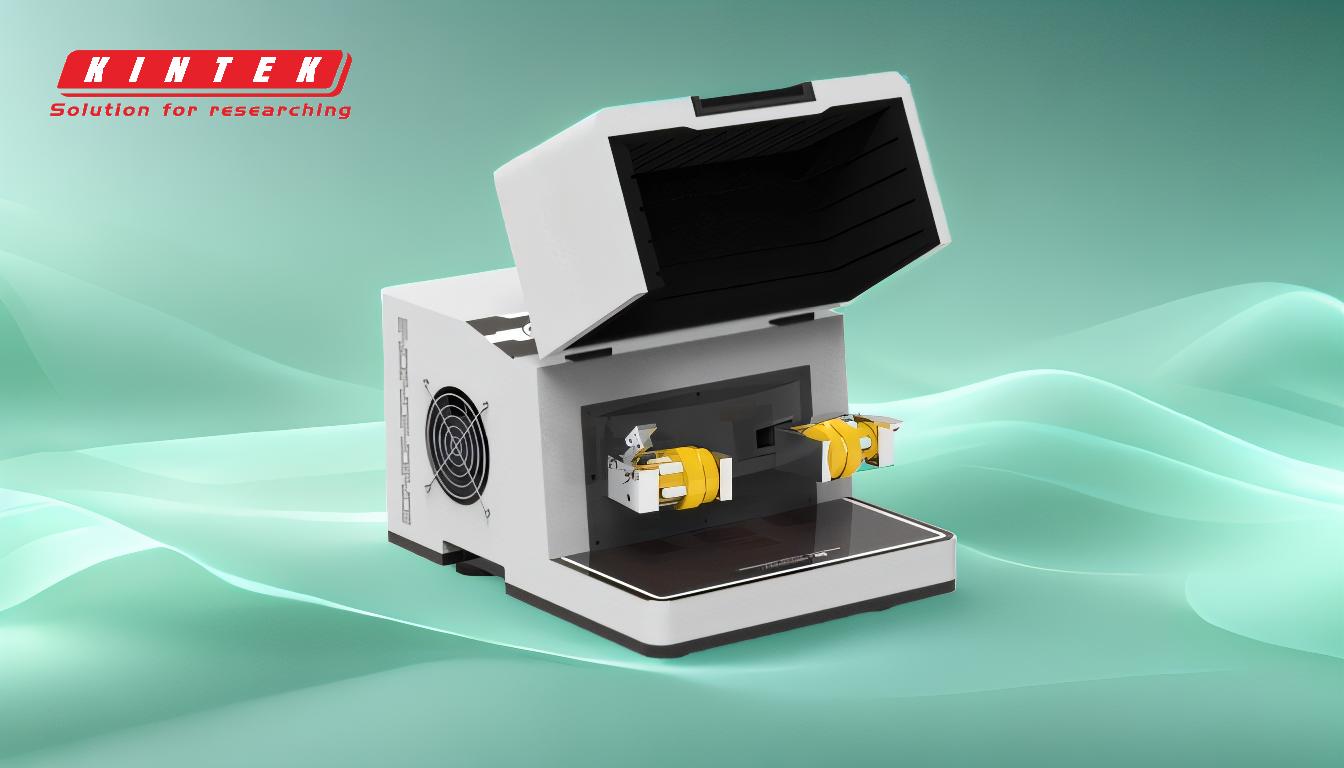
-
Thickness Range in Magnetron Sputtering:
- Magnetron sputtering can produce thin films with thicknesses ranging from nanometers to micrometers. This flexibility makes it suitable for a wide array of applications, from optical coatings to semiconductor devices.
- The thickness depends on the deposition time, target material, and process conditions. For example, a longer deposition time generally results in a thicker film.
-
Factors Influencing Thickness and Uniformity:
- Target-Substrate Distance: The distance between the target and the substrate affects the deposition rate and uniformity. A shorter distance typically results in higher deposition rates but may compromise uniformity.
- Ion Energy: Higher ion energy increases the sputtering rate, leading to thicker films. However, excessively high energy can damage the substrate or alter film properties.
- Gas Pressure: The pressure of the sputtering gas (usually argon) influences the mean free path of the sputtered particles. Optimal pressure ensures efficient deposition and uniform thickness.
- Temperature: Substrate temperature can affect film adhesion and crystallinity, indirectly influencing thickness uniformity.
- Target Erosion Area: The erosion profile of the target material affects the distribution of sputtered particles, impacting film uniformity.
-
Advantages of Magnetron Sputtering for Thickness Control:
- High Precision: Magnetron sputtering allows for precise control over film thickness, making it ideal for applications requiring nanoscale accuracy.
- Uniform Deposition: The use of magnetic fields to trap secondary electrons near the target surface enhances plasma density, leading to more uniform deposition.
- Versatility: It can deposit a wide range of materials, including metals, alloys, and ceramics, with consistent thickness and quality.
-
Comparison with Other Deposition Techniques:
- Compared to electron beam deposition, magnetron sputtering offers better control over film thickness and uniformity, especially for exotic materials and heat-sensitive substrates.
- Diode sputtering, an earlier technique, had limitations in deposition rates and uniformity, which were overcome by the introduction of magnetron sputtering in 1974.
-
Applications Requiring Specific Thicknesses:
- Optical Coatings: Thin films with precise thicknesses are essential for anti-reflective coatings, mirrors, and filters.
- Semiconductor Devices: Uniform thin films are critical for integrated circuits and microelectronic components.
- Wear-Resistant Coatings: Thicker films are often required for applications like cutting tools and mechanical parts.
In summary, magnetron sputtering is a highly adaptable and precise technique for depositing thin films with controlled thickness and uniformity. Its ability to handle a wide range of materials and applications, combined with its high deposition rates and improved plasma stability, makes it a preferred choice in many industries.
Summary Table:
Aspect | Details |
---|---|
Thickness Range | Nanometers to micrometers |
Key Influencing Factors | Target-substrate distance, ion energy, gas pressure, temperature |
Advantages | High precision, uniform deposition, versatility |
Applications | Optical coatings, semiconductor devices, wear-resistant coatings |
Need precise thin-film solutions? Contact us today to learn more about magnetron sputtering!