The thickness of the lining in an induction furnace is a critical factor that depends on several variables, including the type of furnace, the material being melted, and the operating temperature. While the provided references do not specify exact lining thicknesses, they highlight the importance of the lining in protecting the furnace and ensuring efficient operation. The lining must withstand extreme temperatures, thermal shock, and chemical reactions with molten metals. Typically, the thickness is designed to balance thermal insulation, structural integrity, and the furnace's capacity. For precise lining thickness, consulting manufacturer specifications or industry standards is recommended.
Key Points Explained:
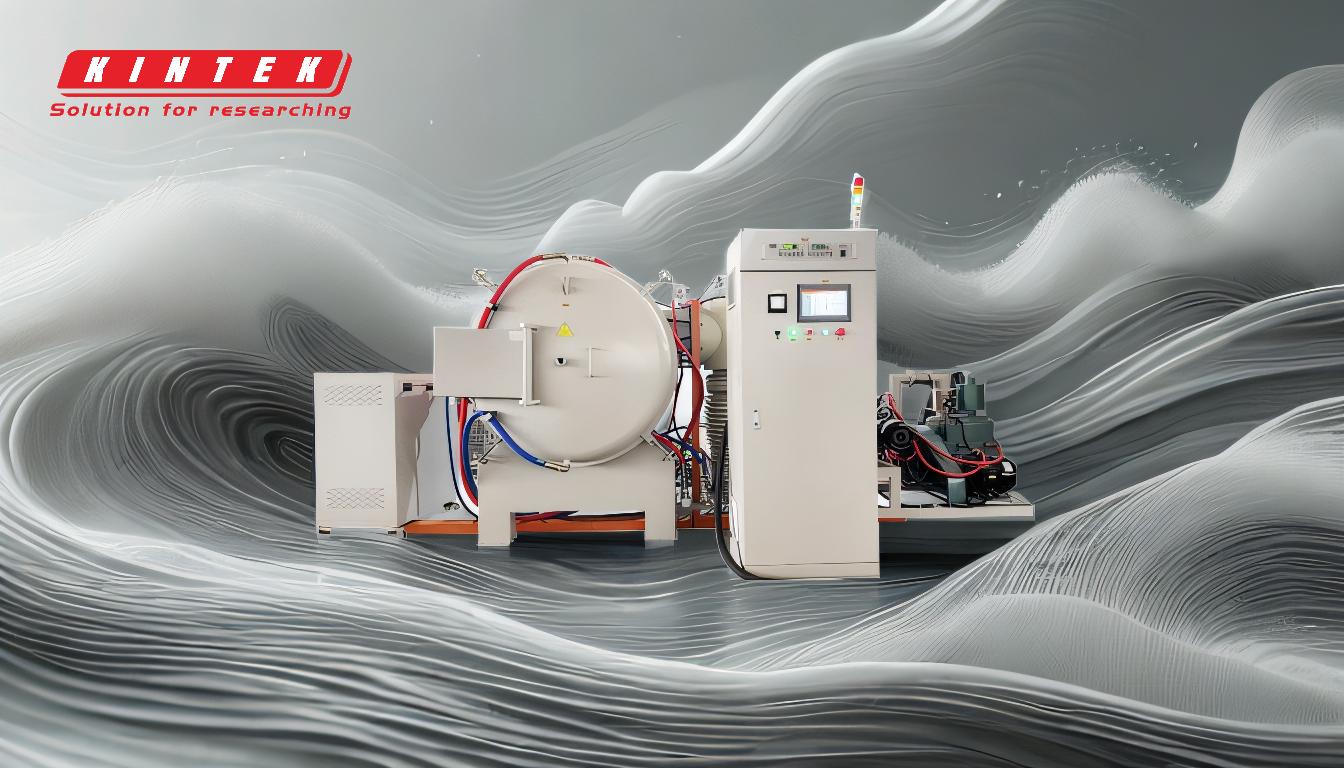
-
Purpose of the Induction Furnace Lining:
- The lining in an induction furnace serves as a barrier between the molten metal and the furnace's structural components, such as the coil. It protects the furnace body from damage caused by high temperatures and chemical reactions.
- It ensures that the molten metal is contained safely, preventing leaks or contamination.
-
Factors Influencing Lining Thickness:
- Material Being Melted: Different metals and alloys require linings with specific properties, such as resistance to chemical reactions or thermal shock. For example, melting steel may require a thicker or more robust lining compared to melting aluminum.
- Operating Temperature: Induction furnaces can reach temperatures up to 1800°C or more. The lining must be thick enough to provide adequate insulation and withstand these extreme temperatures.
- Furnace Type and Size: Larger furnaces or those designed for continuous operation may require thicker linings to ensure durability and longevity.
- Thermal and Mechanical Stress: The lining must resist thermal cycling and mechanical stress caused by the stirring action of the molten metal.
-
Typical Lining Materials:
- Linings are often made from refractory materials such as alumina, silica, or magnesia, chosen for their high melting points and resistance to wear.
- The choice of material and its thickness are tailored to the specific application, ensuring optimal performance and safety.
-
Design Considerations:
- The lining thickness is a balance between providing sufficient insulation and maintaining the furnace's internal capacity.
- Thicker linings offer better insulation and durability but may reduce the furnace's effective working volume.
- Thinner linings may increase capacity but require more frequent maintenance or replacement.
-
Practical Implications for Purchasers:
- When selecting an induction furnace, purchasers should consider the lining's thickness and material in relation to their specific melting requirements.
- Consulting with manufacturers or industry experts can help determine the optimal lining specifications for a given application.
- Regular inspection and maintenance of the lining are essential to ensure safe and efficient furnace operation.
In conclusion, while the exact thickness of an induction furnace lining is not specified in the references, it is clear that the lining's design is tailored to the furnace's operational requirements. Factors such as material type, operating temperature, and furnace size play a significant role in determining the appropriate lining thickness. For precise details, purchasers should refer to manufacturer guidelines or seek expert advice.
Summary Table:
Factor | Impact on Lining Thickness |
---|---|
Material Being Melted | Thicker linings for metals like steel; thinner for aluminum due to varying chemical resistance. |
Operating Temperature | Higher temperatures require thicker linings for better insulation and durability. |
Furnace Type and Size | Larger or continuous-operation furnaces need thicker linings for longevity. |
Thermal/Mechanical Stress | Linings must resist stress from thermal cycling and molten metal stirring. |
Lining Materials | Alumina, silica, or magnesia are chosen for high melting points and wear resistance. |
Need help determining the right lining thickness for your induction furnace? Contact our experts today for tailored advice!