Creating an inert atmosphere involves displacing reactive gases, particularly oxygen, with non-reactive gases like nitrogen, argon, or carbon dioxide. This process is essential in applications such as laboratory experiments, industrial furnaces, and material processing to prevent oxidation or unwanted chemical reactions. The two primary methods for achieving this are purging and evacuation and backfilling. Purging involves flowing inert gas into a vessel to displace oxygen, while evacuation and backfilling involves removing air and replacing it with the desired inert gas. The choice of gas and method depends on the application, cost, and required purity of the atmosphere.
Key Points Explained:
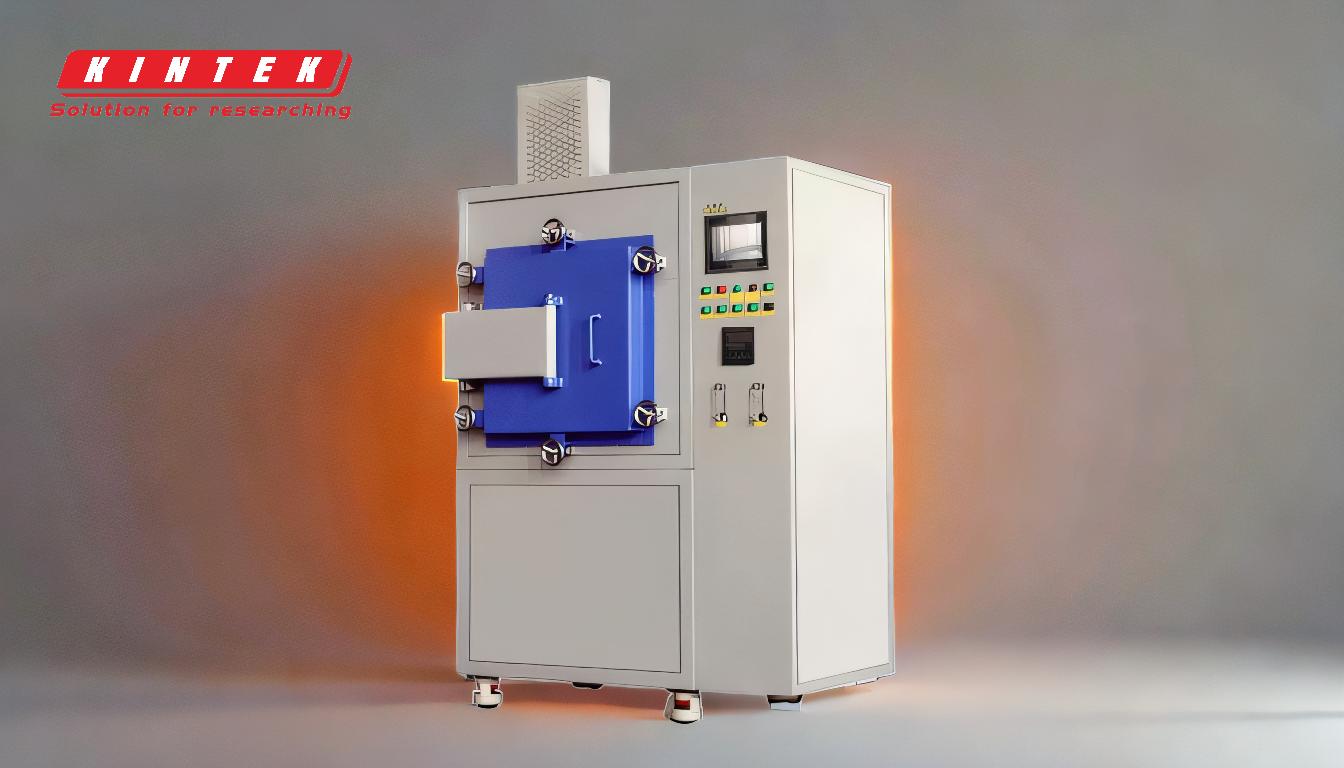
-
Purpose of an Inert Atmosphere
- An inert atmosphere is used to protect materials or samples from reacting with oxygen or other reactive gases in the environment.
- Common applications include preventing oxidation in metal or ceramic processing, safeguarding sensitive chemical reactions, and preserving the integrity of materials in industrial furnaces.
- Inert gases like nitrogen, argon, and carbon dioxide are non-reactive and ideal for this purpose.
-
Common Inert Gases
- Nitrogen (N₂): Widely used due to its high natural abundance, low cost, and high diffusion rate. Suitable for most applications where extreme purity is not required.
- Argon (Ar): Preferred for applications requiring higher purity or where nitrogen might react with the material (e.g., certain metals like titanium).
- Carbon Dioxide (CO₂): Used in specific applications, such as food packaging or fire suppression, but less common in high-temperature or chemical processing.
- Other gases like helium or hydrogen may be used in specialized scenarios, but they are less common due to cost or reactivity concerns.
-
Methods for Creating an Inert Atmosphere
-
Purging:
- Involves continuously flowing inert gas into a vessel to displace oxygen and other reactive gases.
- This method is simpler and more cost-effective but may result in a less pure atmosphere compared to evacuation and backfilling.
- Suitable for applications where moderate purity is acceptable, such as in large industrial furnaces.
-
Evacuation and Backfilling:
- A vacuum pump is used to remove air from the vessel, creating a slight vacuum (up to 0.1 MPa).
- Inert gas is then introduced to replace the removed air, resulting in a purer atmosphere.
- This method is more effective for applications requiring high purity, such as in laboratory experiments or sensitive material processing.
-
Purging:
-
Equipment and Setup
- Vacuum Pump: A rotary vane oil-filled vacuum pump is commonly used to create a slight vacuum in the vessel before introducing inert gas.
- Gas Delivery System: Inert gas is delivered through tubes or hoses connected to the vessel. Flow meters and regulators ensure precise control of gas flow.
- Sealing Mechanism: Proper sealing is critical to maintain the inert atmosphere. Rubber stoppers, septa, or specialized valves are used to prevent gas leakage.
- Monitoring Tools: Oxygen sensors or gas analyzers may be used to verify the purity of the inert atmosphere.
-
Step-by-Step Process for Creating an Inert Atmosphere
-
Preparation:
- Ensure the vessel or furnace is clean and dry. Flame or oven drying may be necessary to remove moisture.
- Assemble the gas delivery system, vacuum pump, and sealing mechanisms.
-
Evacuation (if using evacuation and backfilling):
- Use the vacuum pump to remove air from the vessel, creating a slight vacuum.
-
Gas Introduction:
- Introduce the inert gas (nitrogen or argon) into the vessel. For purging, flow the gas continuously; for backfilling, fill the vessel to the desired pressure.
-
Sealing:
- Seal the vessel tightly to prevent gas leakage. Use rubber stoppers, septa, or valves as needed.
-
Verification:
- Use oxygen sensors or gas analyzers to confirm the absence of oxygen and the purity of the inert atmosphere.
-
Preparation:
-
Applications of Inert Atmospheres
- Laboratory Experiments: Protecting sensitive chemical reactions from oxygen or moisture.
- Industrial Furnaces: Preventing oxidation during the processing of metals, ceramics, or other materials.
- Food Packaging: Extending shelf life by replacing oxygen with inert gases like nitrogen or carbon dioxide.
- Electronics Manufacturing: Protecting components from oxidation during soldering or other processes.
-
Considerations for Equipment and Consumable Purchasers
- Gas Selection: Choose the appropriate gas based on cost, reactivity, and application requirements. Nitrogen is cost-effective for most applications, while argon is better for high-purity needs.
- Purity Requirements: Determine the required purity level and select the method (purging or evacuation and backfilling) accordingly.
- Equipment Quality: Invest in reliable vacuum pumps, gas delivery systems, and sealing mechanisms to ensure consistent performance.
- Safety: Ensure proper handling and storage of inert gases, as they can displace oxygen and pose asphyxiation risks in confined spaces.
By understanding these key points, purchasers and users can effectively create and maintain inert atmospheres tailored to their specific needs.
Summary Table:
Key Aspect | Details |
---|---|
Purpose | Prevent oxidation and unwanted chemical reactions in materials or samples. |
Common Inert Gases | Nitrogen (N₂), Argon (Ar), Carbon Dioxide (CO₂). |
Methods | Purging (continuous gas flow) or Evacuation and Backfilling (vacuum + gas). |
Applications | Labs, industrial furnaces, food packaging, electronics manufacturing. |
Equipment | Vacuum pumps, gas delivery systems, sealing mechanisms, oxygen sensors. |
Considerations | Gas selection, purity requirements, equipment quality, and safety. |
Need help creating an inert atmosphere for your application? Contact our experts today!