Measuring the thickness of PVD (Physical Vapor Deposition) coatings is a critical step in ensuring the quality and performance of coated components. The spherical or micro-abrasion wear test, often referred to as the "dimple-grinder" test, is one of the effective methods for measuring PVD coating thickness, especially for coatings ranging from 0.3 to 30 µm. This method involves creating a small, controlled wear scar on the coated surface and then measuring the depth of the scar to determine the coating thickness. Below, we will explore the key aspects of this method and its application in detail.
Key Points Explained:
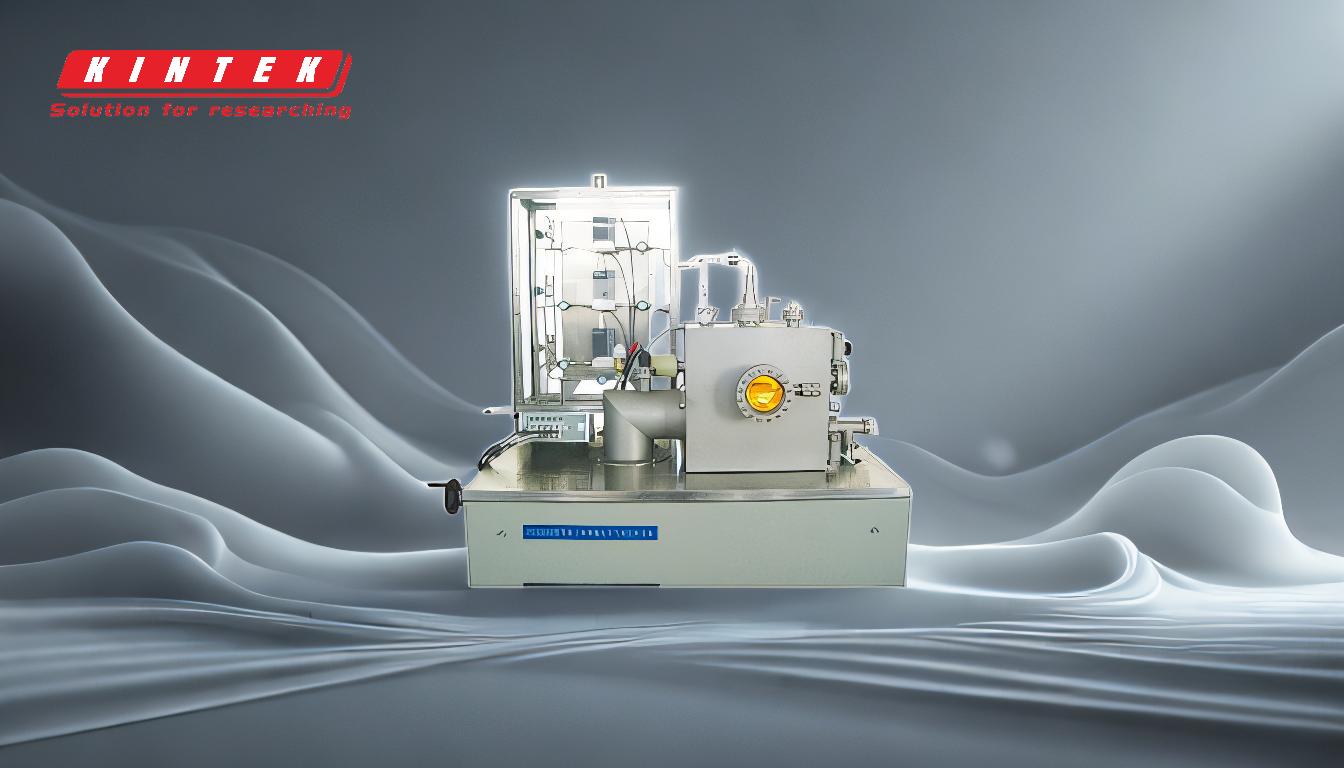
-
Principle of the Spherical or Micro-Abrasion Wear Test
- The test involves using a hard spherical indenter (often made of materials like tungsten carbide or alumina) that is pressed against the coated surface under a controlled load.
- The indenter is rotated or oscillated, creating a small, circular wear scar on the coating.
- The depth of the wear scar is measured using techniques such as optical microscopy, profilometry, or scanning electron microscopy (SEM).
- The coating thickness is determined by analyzing the dimensions of the wear scar and the material removal rate.
-
Advantages of the Dimple-Grinder Test
- High Precision: This method is highly accurate for measuring thin coatings, especially in the range of 0.3 to 30 µm.
- Non-Destructive Nature: While the test involves creating a small wear scar, it is considered minimally invasive and does not significantly damage the component.
- Versatility: It can be used for a wide variety of coatings, including PVD, CVD, and electrochemical coatings.
- Simplicity: The test is relatively simple to perform and does not require complex equipment compared to some other methods.
-
Steps Involved in the Test
- Sample Preparation: The coated sample is cleaned to remove any contaminants that could affect the test results.
- Indentation: The spherical indenter is pressed against the surface with a predefined load and rotated or oscillated to create the wear scar.
- Measurement: The depth and diameter of the wear scar are measured using appropriate techniques.
- Calculation: The coating thickness is calculated based on the geometry of the wear scar and the material properties.
-
Applications of the Method
- This method is widely used in industries where precise coating thickness is critical, such as aerospace, automotive, and tool manufacturing.
- It is particularly useful for measuring the thickness of hard, wear-resistant coatings applied using PVD or CVD techniques.
-
Limitations and Considerations
- Coating Hardness: The method works best for coatings with hardness comparable to or higher than the indenter material. Softer coatings may not produce clear wear scars.
- Surface Roughness: Rough or uneven surfaces can affect the accuracy of the measurements.
- Operator Skill: The test requires careful handling and precise measurement techniques to ensure accurate results.
By understanding the principles and steps involved in the spherical or micro-abrasion wear test, manufacturers and quality control professionals can effectively measure PVD coating thickness and ensure the durability and performance of coated components.
Summary Table:
Aspect | Details |
---|---|
Method | Spherical or micro-abrasion wear test (dimple-grinder test) |
Coating Range | 0.3 to 30 µm |
Key Principle | Create a controlled wear scar and measure its depth |
Measurement Techniques | Optical microscopy, profilometry, SEM |
Advantages | High precision, non-destructive, versatile, simple |
Applications | Aerospace, automotive, tool manufacturing |
Limitations | Coating hardness, surface roughness, operator skill |
Need precise PVD coating thickness measurements? Contact our experts today for tailored solutions!