Brazed aluminum and welded aluminum have different strengths and applications, depending on the specific requirements of the project. Brazing involves joining aluminum parts using a filler metal that melts at a lower temperature than the base metal, while welding involves melting the base metal itself to create a joint. The strength of brazed aluminum joints can approach that of welded joints, but it depends on factors such as joint design, filler material, and process control. Brazing is often preferred for its ability to join complex shapes and dissimilar metals, while welding is favored for high-stress applications requiring maximum strength. Understanding the differences between these methods is crucial for selecting the right joining technique for aluminum components.
Key Points Explained:
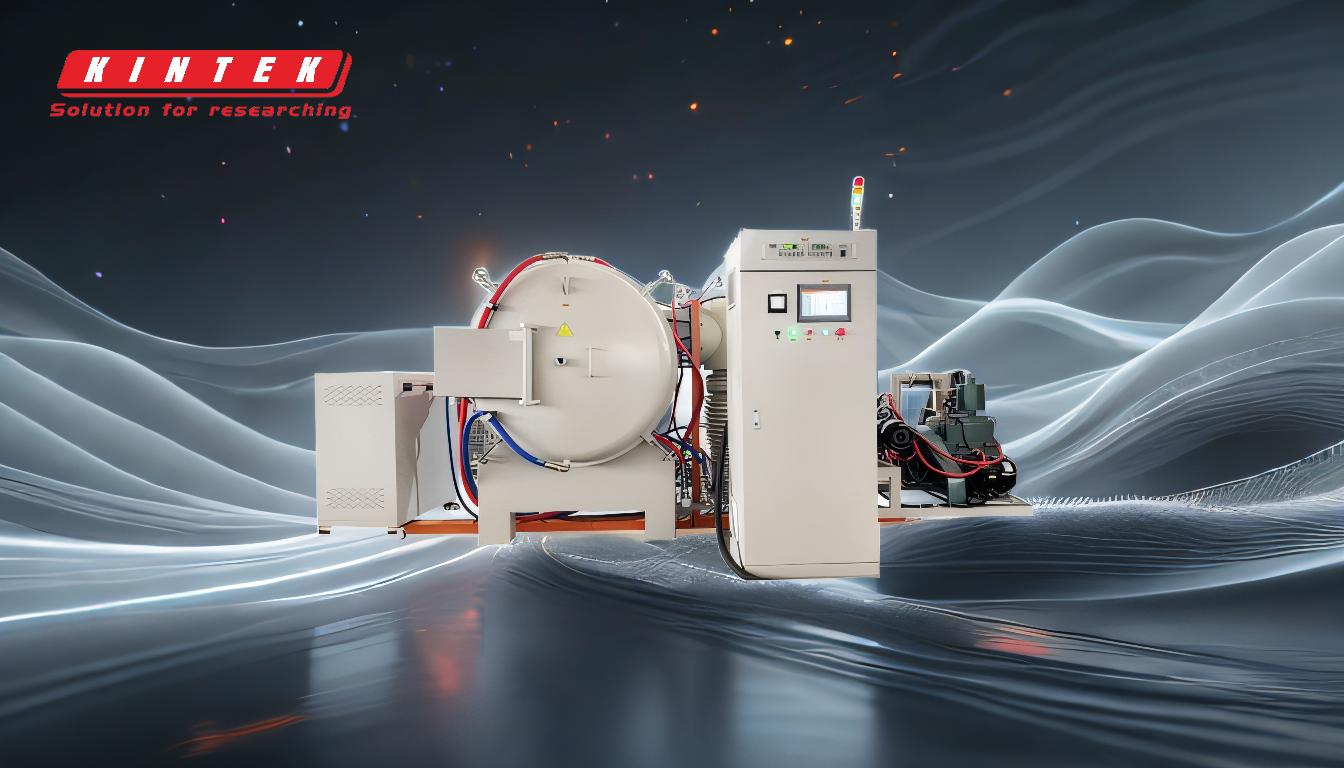
-
Definition and Process of Brazing and Welding:
- Brazing: A joining process where a filler metal (with a melting point below that of the base metal) is heated to flow into the joint by capillary action. It is typically performed at temperatures above 450°C (840°F) but below the melting point of the base metal.
- Welding: A process that involves melting the base metal to create a fusion joint. It requires higher temperatures and often results in a stronger bond compared to brazing.
-
Strength Comparison:
- Brazed joints can achieve up to 70-80% of the strength of the base metal, depending on the filler material and joint design.
- Welded joints generally match or exceed the strength of the base metal, making them suitable for high-stress applications.
- The strength of brazed joints is influenced by factors like joint geometry, surface preparation, and the type of filler metal used.
-
Advantages of Brazing:
- Suitable for joining complex shapes and thin materials.
- Can join dissimilar metals, such as aluminum to copper or steel.
- Produces less distortion and residual stress compared to welding.
- Ideal for applications where heat input must be minimized to avoid damaging sensitive components.
-
Advantages of Welding:
- Provides higher joint strength, making it ideal for structural and load-bearing applications.
- Creates a metallurgical bond, which is often more durable under extreme conditions.
- Suitable for thick materials and high-stress environments.
-
Applications of Brazed and Welded Aluminum:
- Brazing: Commonly used in heat exchangers, automotive radiators, and HVAC systems due to its ability to create leak-proof joints and handle complex geometries.
- Welding: Preferred in aerospace, automotive frames, and structural components where maximum strength is required.
-
Factors Affecting Joint Strength:
- Joint Design: Properly designed joints (e.g., lap joints for brazing) can enhance strength.
- Filler Material: The choice of filler metal (e.g., aluminum-silicon alloys for brazing) impacts the joint's mechanical properties.
- Surface Preparation: Clean, oxide-free surfaces are critical for strong brazed and welded joints.
- Process Control: Consistent heating and cooling rates are essential to avoid defects like porosity or cracking.
-
Limitations of Brazing:
- Lower strength compared to welding, especially in high-stress applications.
- Limited to specific filler metals and base metal combinations.
- Requires precise temperature control to avoid melting the base metal.
-
Limitations of Welding:
- Higher heat input can cause distortion or damage to thin or heat-sensitive materials.
- More challenging to weld dissimilar metals due to differences in melting points and thermal expansion rates.
- Requires skilled operators and specialized equipment.
-
Choosing Between Brazing and Welding:
- Consider the application's strength requirements, material thickness, and joint complexity.
- Evaluate the need for joining dissimilar metals or minimizing heat input.
- Assess the cost and availability of equipment and skilled labor.
-
Future Trends:
- Advances in brazing filler materials and techniques (e.g., vacuum brazing) are improving joint strength and expanding applications.
- Innovations in welding, such as friction stir welding, are enhancing the quality and efficiency of aluminum joints.
By understanding these key points, you can make an informed decision about whether brazed or welded aluminum is the right choice for your specific application.
Summary Table:
Aspect | Brazing | Welding |
---|---|---|
Strength | 70-80% of base metal strength | Matches or exceeds base metal strength |
Process | Uses filler metal, lower temperatures | Melts base metal, higher temperatures |
Advantages | Joins complex shapes, dissimilar metals, less distortion | High strength, durable metallurgical bond, ideal for high-stress applications |
Applications | Heat exchangers, radiators, HVAC systems | Aerospace, automotive frames, structural components |
Limitations | Lower strength, limited filler/base metal combinations | Distortion, challenging for dissimilar metals, requires skilled operators |
Need help choosing between brazed and welded aluminum for your project? Contact our experts today for personalized advice!