Brazing and soldering are both metal-joining techniques, but they differ significantly in terms of strength, application, and versatility. Brazing is generally considered superior to soldering for applications requiring stronger, more durable joints. It is widely used in industries such as cookware, automotive, and HVAC systems due to its ability to create joints as strong as the base metals themselves. Additionally, brazing offers advantages like high joint strength, excellent consistency, and the ability to handle complex geometries. Vacuum brazing further enhances the process by preventing oxidation and maintaining a clean appearance. Brazing is particularly advantageous for materials like cast iron, as it minimizes heating, preserves the base metal's properties, and reduces the risk of cracking.
Key Points Explained:
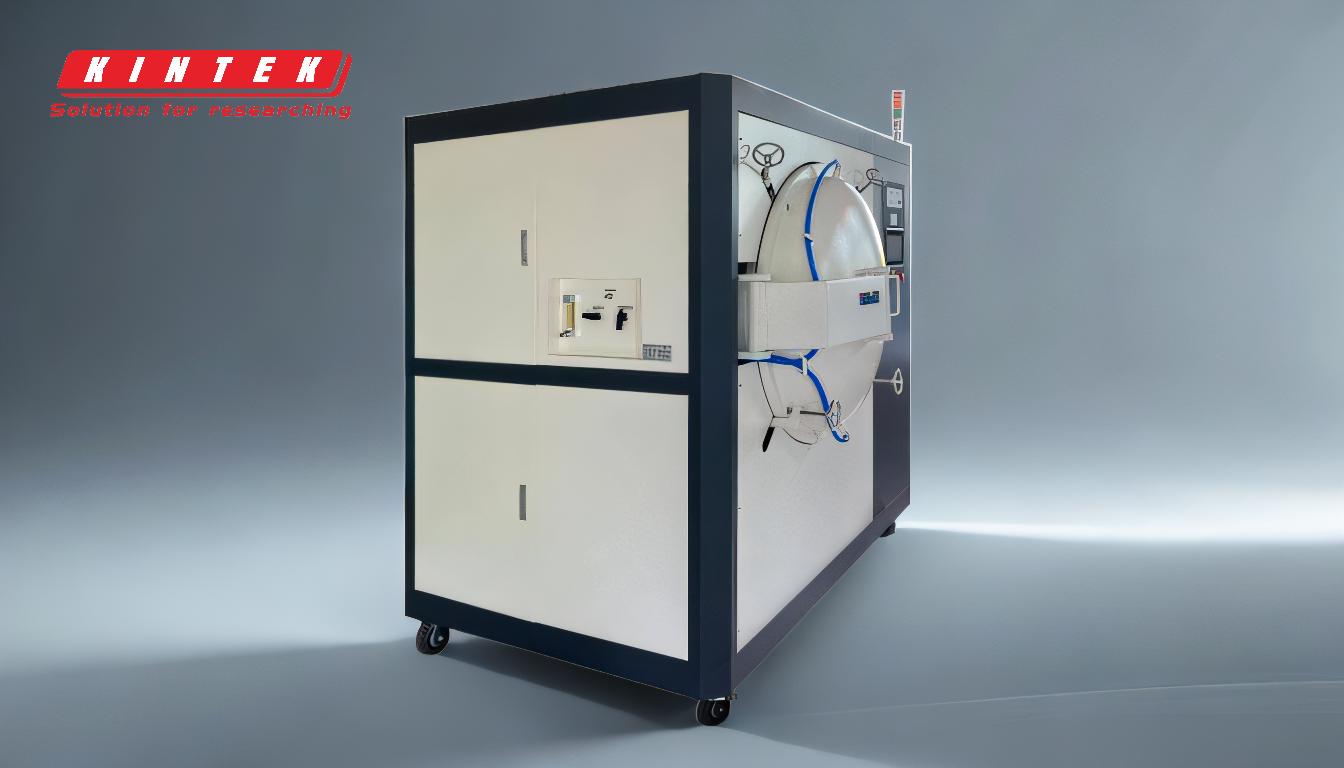
-
Strength of Joints:
- Brazing produces joints that are as strong as the base metals, making it ideal for applications requiring durability and reliability. This is a significant advantage over soldering, which typically creates weaker joints.
-
Versatility and Industry Applications:
- Brazing is widely used across various industries, including cookware, automotive, and HVAC systems. Its versatility makes it a preferred choice for clients seeking robust metal-joining solutions.
-
Vacuum Brazing Benefits:
- Vacuum brazing keeps the finished part free from oxidation, ensuring a clean appearance. This process also maintains high joint strength and excellent part-to-part consistency in both appearance and size.
-
Complex Joining Geometries:
- Brazing allows for the joining of complex geometries, which can be challenging with soldering. This capability is crucial for industries requiring intricate designs and precise assemblies.
-
Advantages for Cast Iron:
- Brazing cast iron involves limited heating, which prevents the base metal from reaching its melting temperature. This preserves the metal's properties and reduces the risk of cracking. Additionally, brazing can fill large lap joints without the need for external welds.
-
Reduced Risk of Cracking:
- The controlled heating process in brazing minimizes the risk of cracking, especially in materials like cast iron. This makes brazing a safer and more reliable option for joining such materials.
In summary, brazing offers numerous advantages over soldering, including stronger joints, greater versatility, and the ability to handle complex geometries. Its benefits are particularly evident in industries requiring durable and reliable metal-joining solutions.
Summary Table:
Aspect | Brazing | Soldering |
---|---|---|
Joint Strength | As strong as base metals, ideal for durability | Weaker joints, less durable |
Industry Applications | Cookware, automotive, HVAC systems | Limited to less demanding applications |
Oxidation Prevention | Vacuum brazing prevents oxidation, ensuring clean appearance | Oxidation may occur, affecting appearance |
Complex Geometries | Capable of joining intricate designs | Limited ability for complex geometries |
Material Compatibility | Ideal for cast iron, preserves base metal properties | Less suitable for materials like cast iron |
Risk of Cracking | Minimized due to controlled heating | Higher risk of cracking in certain materials |
Upgrade your metal-joining process with brazing—contact us today to learn more!