Brazing and welding are both essential joining techniques, but they differ significantly in terms of cost, application, and process. Brazing involves using a filler metal to join materials without melting the base metals, typically at temperatures above 840°F. It is known for producing strong joints that are as robust as the base materials themselves. Welding, on the other hand, involves melting the base metals to fuse them together, often requiring higher temperatures and more specialized equipment. The cost comparison between brazing and welding depends on factors such as material compatibility, joint design, labor, and equipment requirements. Generally, brazing can be more cost-effective for certain applications due to lower energy consumption, reduced material waste, and the ability to join dissimilar materials.
Key Points Explained:
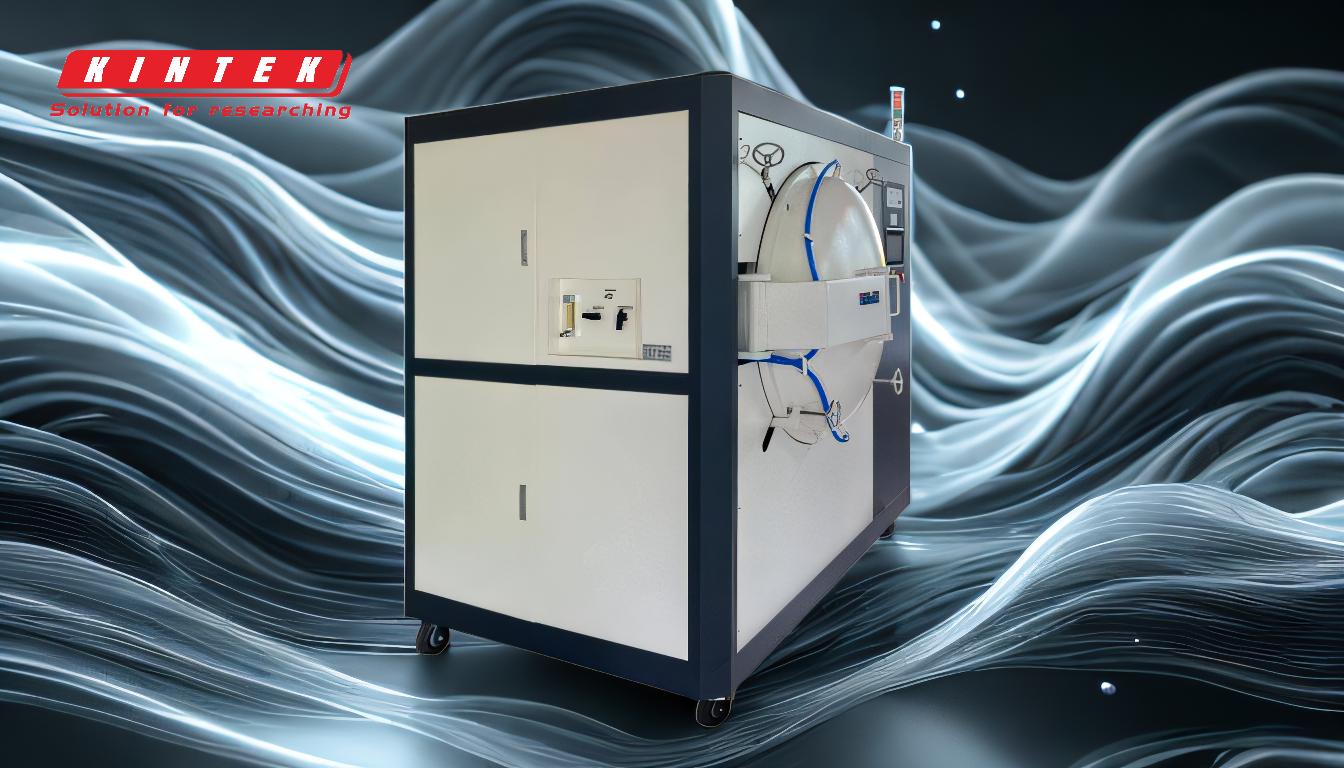
-
Process and Temperature Requirements:
- Brazing operates at lower temperatures compared to welding, typically above 840°F but below the melting point of the base materials. This reduces energy consumption and minimizes the risk of thermal distortion.
- Welding requires significantly higher temperatures to melt the base metals, which can lead to higher energy costs and potential material deformation.
-
Material Compatibility:
- Brazing is highly versatile and can join dissimilar materials, such as metals and ceramics, which is often challenging or impossible with welding.
- Welding is generally limited to similar materials, as the process relies on melting and fusing the base metals.
-
Joint Strength and Durability:
- Brazed joints are as strong as the base metals and are highly durable, making them suitable for applications in industries like automotive, HVAC, and cookware.
- Welded joints can be stronger than the base materials in some cases, but they may also introduce weaknesses due to heat-affected zones and residual stresses.
-
Equipment and Labor Costs:
- Brazing typically requires less expensive equipment and can be performed with simpler tools, reducing initial investment costs.
- Welding often necessitates specialized and costly equipment, such as arc welders or laser welders, along with skilled labor, which can increase overall expenses.
-
Application-Specific Considerations:
- Brazing is ideal for intricate designs and thin materials, as it produces clean, precise joints without significant material distortion.
- Welding is better suited for heavy-duty applications where high strength and structural integrity are paramount, such as in construction or heavy machinery.
-
Cost-Effectiveness:
- Brazing can be more economical for certain applications due to lower energy usage, reduced material waste, and the ability to join dissimilar materials.
- Welding may incur higher costs due to energy consumption, equipment maintenance, and the need for skilled operators.
In conclusion, while welding is often perceived as the go-to method for strong, permanent joints, brazing offers a cost-effective alternative for many applications, particularly when joining dissimilar materials or working with intricate designs. The choice between brazing and welding ultimately depends on the specific requirements of the project, including material compatibility, joint strength, and budget constraints.
Summary Table:
Aspect | Brazing | Welding |
---|---|---|
Temperature | Lower (above 840°F, below base metal melting point) | Higher (melts base metals) |
Material Compatibility | Can join dissimilar materials (e.g., metals and ceramics) | Limited to similar materials |
Joint Strength | As strong as base metals, durable for industries like automotive and HVAC | Can be stronger but may introduce weaknesses due to heat-affected zones |
Equipment Cost | Less expensive, simpler tools | Specialized, costly equipment (e.g., arc welders, laser welders) |
Labor Cost | Lower, less skilled labor required | Higher, skilled operators needed |
Applications | Ideal for intricate designs, thin materials, and dissimilar material joins | Best for heavy-duty applications requiring high structural integrity |
Cost-Effectiveness | More economical for certain applications (lower energy, reduced waste) | Higher costs due to energy, equipment, and skilled labor |
Need help choosing between brazing and welding? Contact our experts today for tailored solutions!