DLC (Diamond-Like Carbon) coatings are renowned for their exceptional hardness, low friction, and wear resistance, making them highly suitable for protective applications. However, while DLC coatings are highly scratch-resistant due to their hardness and smooth surface, they are not entirely scratch-proof. The scratch resistance of DLC coatings depends on factors such as the specific composition of the coating, the deposition method, and the application environment. Although they significantly reduce the likelihood of scratches compared to untreated surfaces, they can still be damaged under extreme conditions or when exposed to materials harder than the coating itself.
Key Points Explained:
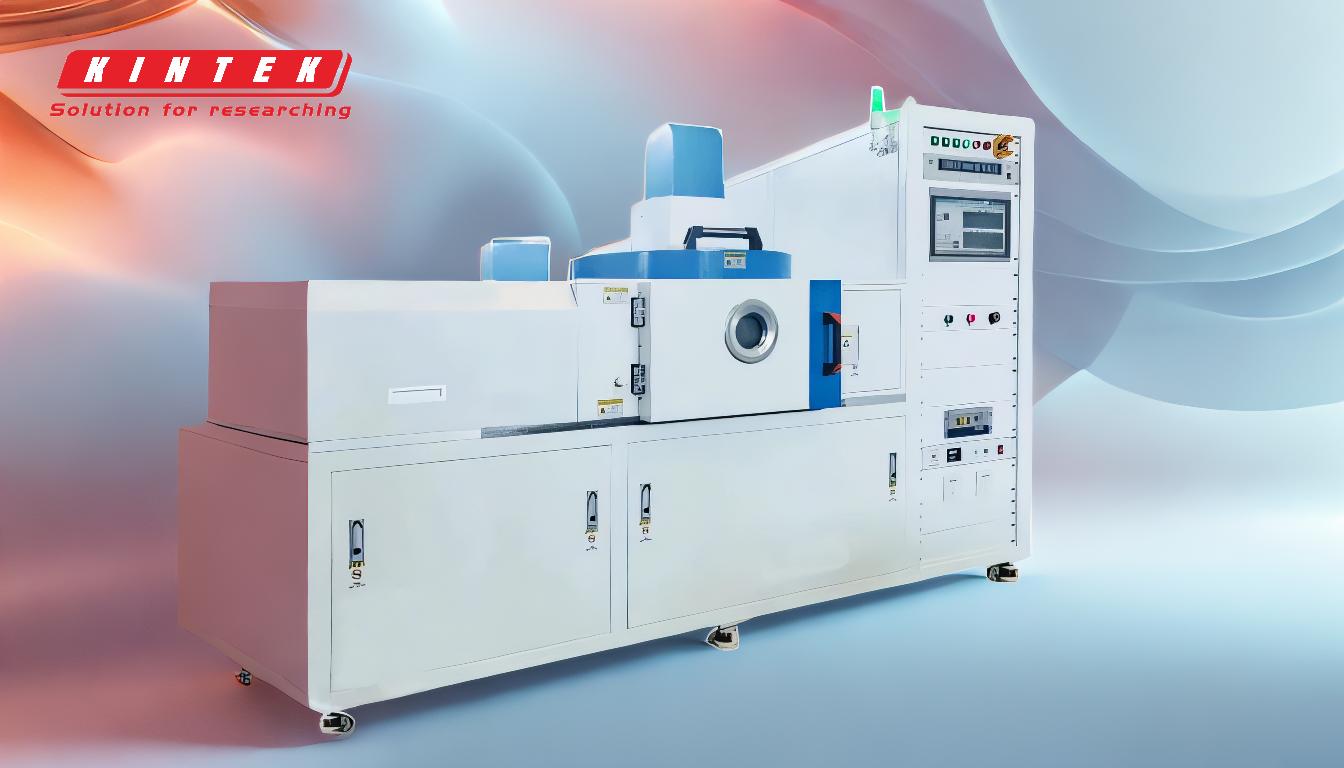
-
High Hardness and Scratch Resistance:
- DLC coatings are characterized by their high hardness, which is a result of the significant fraction of sp3 (diamond-like) carbon bonds in their structure. This hardness makes them highly resistant to scratches and wear.
- The hardness of DLC coatings can vary depending on the deposition method and the specific composition of the coating. For example, coatings with a higher proportion of sp3 bonds tend to be harder and more scratch-resistant.
-
Not Entirely Scratch-Proof:
- While DLC coatings are highly scratch-resistant, they are not completely scratch-proof. Under extreme conditions, such as contact with materials harder than the coating (e.g., diamond or certain ceramics), scratches can still occur.
- The scratch resistance of DLC coatings also depends on the thickness of the coating, the substrate material, and the application environment. For instance, in high-stress or abrasive environments, the coating may eventually wear down.
-
Low Coefficient of Friction:
- DLC coatings have a low coefficient of friction, which reduces the likelihood of scratches caused by sliding or rubbing against other surfaces. This property is particularly beneficial in applications where sliding contact is frequent, such as in automotive components or cutting tools.
- The low friction also contributes to the overall durability of the coating, as it minimizes wear and tear over time.
-
Chemical Inertness and Corrosion Resistance:
- DLC coatings are chemically inert and resistant to corrosion, which helps maintain their integrity and scratch resistance in harsh environments. This makes them suitable for use in industries such as aerospace, medical devices, and industrial machinery.
- The chemical stability of DLC coatings ensures that they do not degrade easily when exposed to acids, bases, or other corrosive substances, further enhancing their durability.
-
Deposition Methods and Customization:
- The properties of DLC coatings, including their scratch resistance, can be tailored by controlling the deposition parameters and gas phase composition during the coating process. For example, Plasma-Assisted Chemical Vapor Deposition (PACVD) is a common method used to produce DLC coatings with specific hardness and friction characteristics.
- By adjusting the deposition process, manufacturers can optimize the coating for specific applications, balancing hardness, friction, and other properties to meet the desired performance requirements.
-
Applications and Limitations:
- DLC coatings are widely used in applications that require enhanced durability, reduced friction, and improved appearance, such as in automotive components, cutting tools, and decorative finishes.
- While DLC coatings offer significant advantages in terms of scratch resistance, they are not suitable for all applications. For example, in environments where extreme hardness or impact resistance is required, other coatings or materials may be more appropriate.
-
Comparison to Diamond Coatings:
- Diamond coatings, which are composed entirely of sp3 bonds, are harder and more scratch-resistant than DLC coatings. However, diamond coatings are more expensive and challenging to produce, making DLC coatings a more cost-effective alternative for many applications.
- DLC coatings strike a balance between performance and cost, offering high scratch resistance and durability without the high expense associated with diamond coatings.
In conclusion, while DLC coatings are highly scratch-resistant due to their hardness, low friction, and chemical inertness, they are not entirely scratch-proof. Their performance depends on factors such as composition, deposition method, and application environment. For most practical purposes, DLC coatings provide excellent protection against scratches and wear, making them a valuable choice for a wide range of industrial and decorative applications.
Summary Table:
Property | Details |
---|---|
Hardness | High due to sp3 carbon bonds; varies with composition and deposition method. |
Scratch Resistance | Highly resistant but not scratch-proof; can be damaged by harder materials. |
Friction | Low coefficient of friction, reducing wear and scratches. |
Chemical Resistance | Chemically inert and corrosion-resistant, ideal for harsh environments. |
Applications | Automotive, cutting tools, aerospace, medical devices, and decorative uses. |
Limitations | Not suitable for extreme hardness or impact resistance. |
Interested in enhancing your materials with DLC coatings? Contact our experts today to learn more!