Induction brazing and gas brazing are two widely used methods in the manufacturing industry, each with its own set of advantages and disadvantages. The choice between the two depends on various factors such as the specific application, material properties, and production requirements. Induction brazing is often favored for its precision, speed, and ability to produce high-quality joints, while gas brazing is appreciated for its simplicity, lower initial costs, and versatility. Understanding the key differences between these methods can help in making an informed decision based on the specific needs of a project.
Key Points Explained:
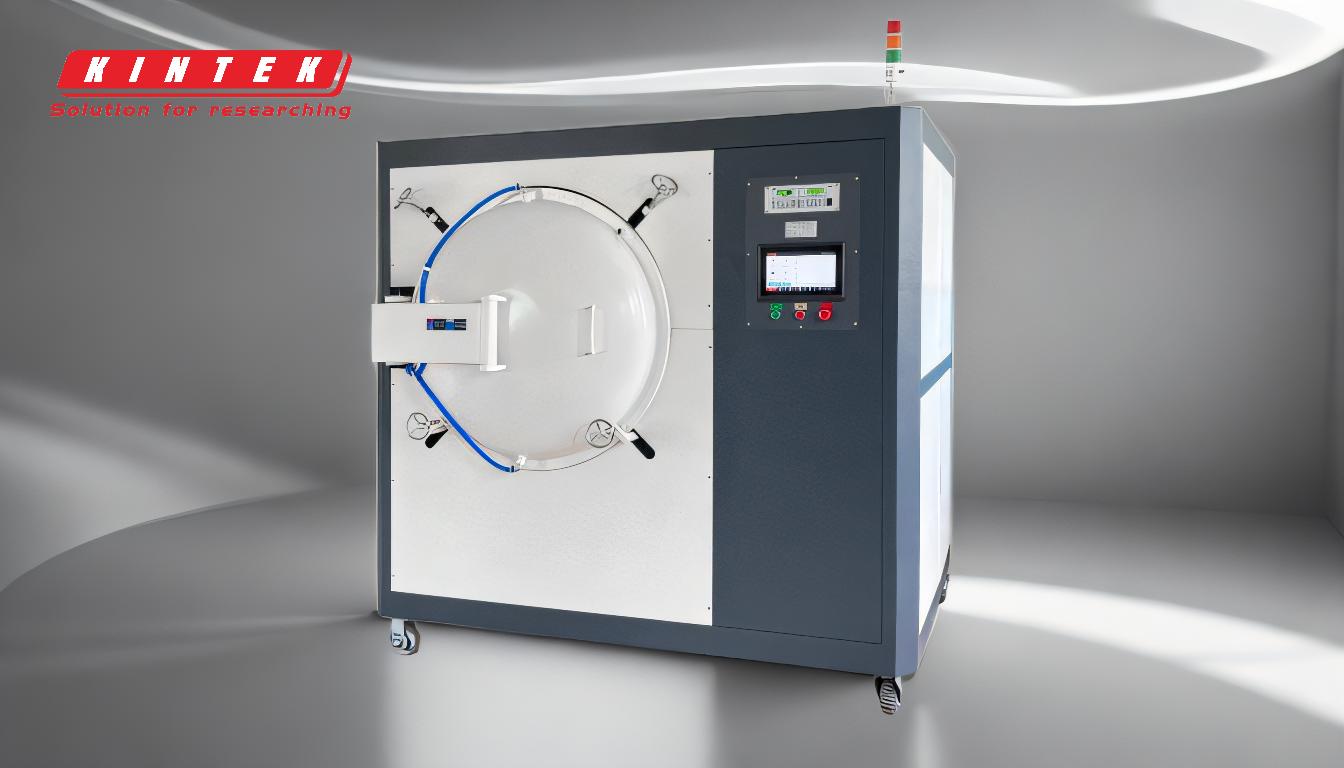
-
Quality of Joints:
- Induction Brazing: This method is known for producing high-quality joints with excellent strength and cleanliness. The localized heating ensures that only the specific area to be brazed is heated, reducing the risk of thermal distortion and contamination. This results in a more precise and reliable joint.
- Gas Brazing: While gas brazing can also produce strong joints, the quality may not be as consistent as with induction brazing. The broader heat application can sometimes lead to uneven heating and potential contamination from the flame, affecting the overall quality of the joint.
-
Productivity:
- Induction Brazing: Induction brazing is generally faster than gas brazing due to the rapid heating capabilities of induction coils. This can significantly increase productivity, especially in high-volume production settings. The process is also more repeatable, which is beneficial for maintaining consistent quality in mass production.
- Gas Brazing: Gas brazing tends to be slower because it relies on the manual or semi-automatic application of heat using a gas flame. This can lead to longer cycle times and lower productivity, particularly in large-scale operations.
-
Cost Considerations:
- Induction Brazing: The initial setup cost for induction brazing can be higher due to the need for specialized equipment such as induction coils and power supplies. However, the long-term benefits, including higher productivity and lower energy consumption, can offset these initial costs.
- Gas Brazing: Gas brazing typically has lower initial costs since it requires less specialized equipment. However, the ongoing costs of gas and the potential for higher labor costs due to slower processing times can add up over time.
-
Application Suitability:
- Induction Brazing: This method is particularly well-suited for applications requiring precise and localized heating, such as in the aerospace and electronics industries. It is also ideal for materials that are sensitive to oxidation or thermal distortion.
- Gas Brazing: Gas brazing is more versatile and can be used on a wider range of materials and joint configurations. It is often preferred for larger components or in situations where the initial cost of equipment is a significant consideration.
-
Environmental and Safety Considerations:
- Induction Brazing: Induction brazing is generally considered safer and more environmentally friendly since it does not involve open flames or combustible gases. This reduces the risk of fire and exposure to harmful fumes.
- Gas Brazing: Gas brazing involves the use of flammable gases, which can pose safety risks if not properly managed. Additionally, the combustion process can produce harmful emissions, requiring proper ventilation and safety measures.
In summary, induction brazing offers superior quality and productivity but comes with higher initial costs. Gas brazing, while more cost-effective initially, may not provide the same level of precision and consistency. The choice between the two methods should be based on the specific requirements of the application, including the desired quality, production volume, and budget constraints.
Summary Table:
Aspect | Induction Brazing | Gas Brazing |
---|---|---|
Quality of Joints | High-quality, precise, and clean | Strong but less consistent |
Productivity | Faster, ideal for high-volume production | Slower, manual or semi-automatic |
Cost Considerations | Higher initial cost, lower long-term costs | Lower initial cost, higher ongoing costs |
Application Suitability | Precise heating, ideal for sensitive materials | Versatile, suitable for larger components |
Environmental & Safety | Safer, no open flames or harmful emissions | Requires proper ventilation, safety risks |
Need help choosing the right brazing method for your project? Contact our experts today!