Induction heating is highly efficient, with modern systems achieving efficiencies of over 90%. Its efficiency stems from the direct generation of heat within the object being heated, eliminating energy losses associated with external heat sources. Key factors influencing efficiency include the material's properties, system design, and the required temperature variation. Advancements in semiconductor technology and coil design are further enhancing efficiency. Induction heating is fast, precise, and clean, making it suitable for applications where contamination or precise temperature control is critical. However, efficiency can vary depending on the specific application and system design.
Key Points Explained:
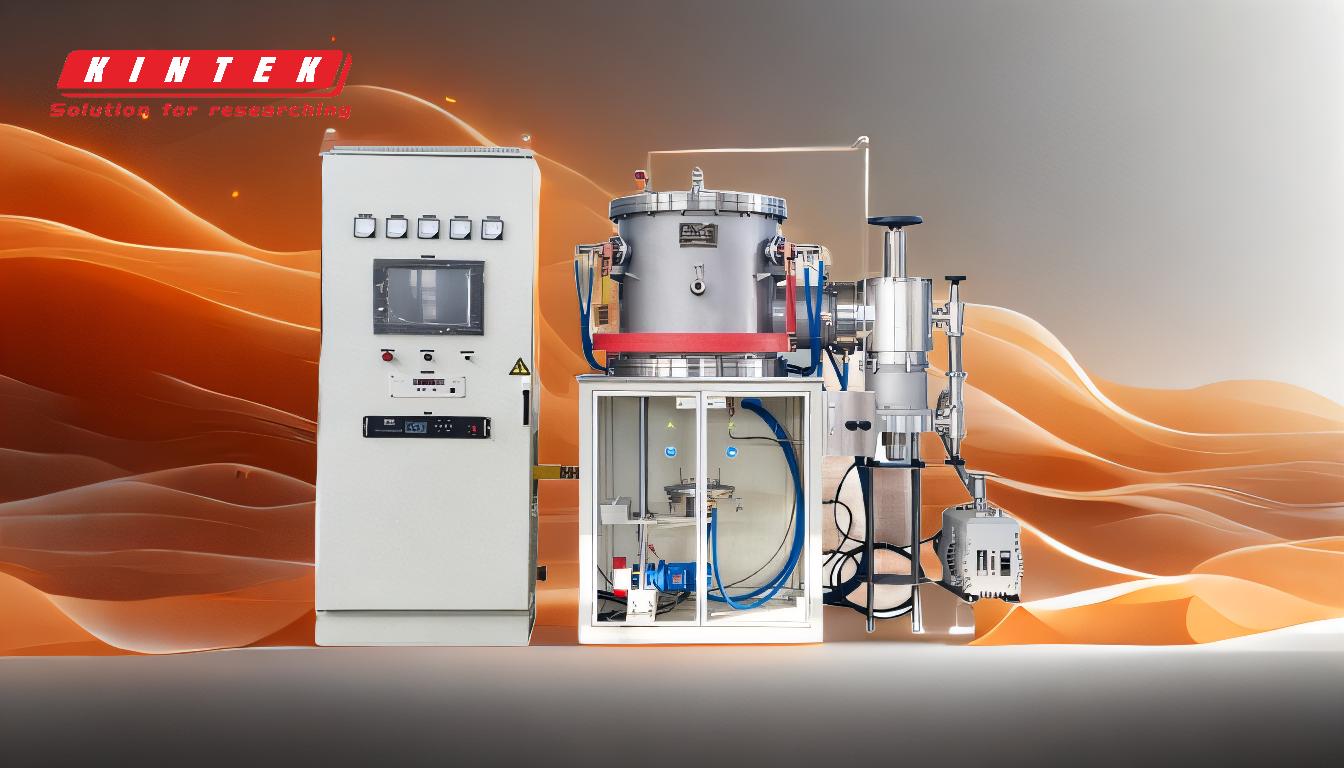
-
High Efficiency (Over 90%):
- Induction heating systems are known for their high efficiency, often exceeding 90%. This is because heat is generated directly within the object being heated, minimizing energy losses that occur in traditional heating methods like gas or electric furnaces, where heat must be transferred through convection or radiation.
-
Direct Heat Generation:
- Unlike conventional heating methods, induction heating generates heat directly within the material through induced electrical currents. This eliminates the need for external heat sources and reduces energy waste, making the process inherently more efficient.
-
Rapid Heating:
- Induction heating is fast, as the heat is generated internally and does not rely on slow heat transfer mechanisms. This rapid heating capability is particularly beneficial in industrial applications where time efficiency is critical.
-
Precise Control:
- The process allows for precise control over heating power and temperature, enabling targeted heating at specific depths or areas. This precision reduces energy waste and ensures optimal heating for the application.
-
No External Contact:
- Since induction heating does not require physical contact with the object, it is ideal for applications where contamination must be avoided. This feature also contributes to the system's efficiency and cleanliness.
-
Factors Affecting Efficiency:
- Material Properties: The type of material, its resistivity, size, and thickness significantly influence heating efficiency. Conductive materials with higher resistivity heat faster.
- Frequency of Alternating Current: Higher frequencies result in lower heating depths, which can be tailored to the application's requirements.
- Inductor Coil Design: Advanced coil designs improve efficiency by optimizing the magnetic field and heat distribution.
- Power Supply Capacity: The power supply must account for the material's specific heat, mass, and required temperature rise, as well as heat losses due to conduction, convection, and radiation.
-
Advancements in Technology:
- Ongoing advancements in semiconductor technology and coil design are driving improvements in induction heating efficiency. These innovations aim to enhance system performance, reliability, and energy utilization.
-
Comparison with Traditional Heating Methods:
- Induction heating outperforms traditional methods like gas furnaces, electric furnaces, and salt baths in terms of speed, precision, and energy efficiency. Traditional methods rely on slower heat transfer mechanisms, which are less efficient and harder to control.
-
Application-Specific Efficiency:
- The efficiency of an induction heating system can vary depending on the application. Factors such as the required temperature variation, part characteristics, and system design play a crucial role in determining overall efficiency.
-
Environmental and Safety Benefits:
- Induction heating is clean and safe, as it does not involve fuel combustion or external heat sources. This reduces environmental impact and enhances workplace safety, further contributing to its overall efficiency.
In summary, induction heating is a highly efficient and versatile heating method, offering significant advantages over traditional techniques. Its efficiency is influenced by material properties, system design, and technological advancements, making it a preferred choice for many industrial and commercial applications.
Summary Table:
Key Feature | Description |
---|---|
High Efficiency (Over 90%) | Heat generated directly within the object, minimizing energy losses. |
Direct Heat Generation | Eliminates external heat sources, reducing energy waste. |
Rapid Heating | Fast internal heat generation, ideal for time-sensitive applications. |
Precise Control | Targeted heating at specific depths or areas, reducing energy waste. |
No External Contact | Avoids contamination, enhancing cleanliness and efficiency. |
Factors Affecting Efficiency | Material properties, frequency, coil design, and power supply capacity. |
Advancements in Technology | Semiconductor and coil design improvements enhance performance and reliability. |
Environmental Benefits | Clean and safe, with no fuel combustion or external heat sources. |
Ready to explore the benefits of induction heating for your application? Contact our experts today to learn more!