Induction heating is an excellent method for forging due to its precision, efficiency, and ability to provide consistent and localized heating. Unlike traditional heating methods, induction heating generates heat directly within the material through electromagnetic induction, ensuring rapid and uniform heating. This method is particularly advantageous for forging because it allows for precise temperature control, reduces energy consumption, and minimizes contamination risks. Additionally, induction heating supports automation, making it suitable for high-volume production environments. Its ability to heat specific depths and areas of a workpiece makes it ideal for forging complex shapes and materials. Overall, induction heating enhances productivity, quality, and environmental sustainability in forging processes.
Key Points Explained:
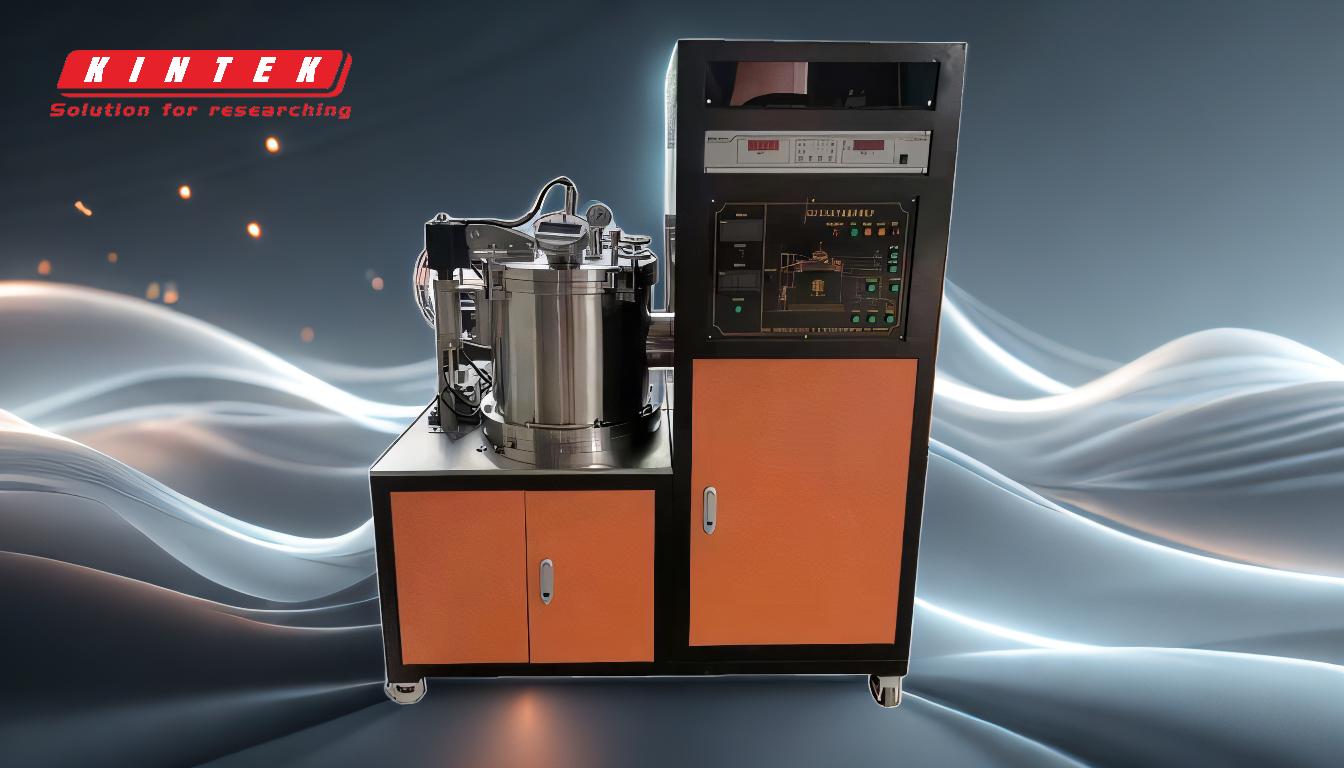
-
Direct and Localized Heating:
- Induction heating generates heat directly within the surface of the conductive material through electromagnetic induction. This eliminates the need for external heat sources like flames or furnaces, reducing heat loss and improving energy efficiency.
- The localized heating capability is particularly beneficial for forging, as it allows specific areas of the workpiece to be heated without affecting the entire material. This is crucial for forging complex shapes or parts that require precise temperature control.
-
Precise Temperature Control:
- Induction heating systems offer exceptional control over the heating process, enabling operators to achieve and maintain precise temperatures. This is critical in forging, where material properties and structural integrity depend on accurate heating.
- The ability to adjust the frequency of the current allows for control over the depth of heating, ensuring that the material is heated uniformly and to the required depth for forging.
-
Rapid Heating and Improved Productivity:
- Induction heating is significantly faster than traditional heating methods, as it eliminates the need for preheating furnaces or extended heat transfer times. This rapid heating reduces cycle times and increases throughput in forging operations.
- The speed and efficiency of induction heating make it ideal for high-volume production environments, where time and energy savings translate into cost reductions.
-
Consistency and Repeatability:
- Induction heating ensures consistent and repeatable results, which are essential for producing high-quality forged parts. The uniform heating process minimizes variations in material properties, leading to better performance and reliability of the final product.
- This consistency is particularly important in industries like aerospace and automotive, where forged components must meet strict quality standards.
-
Clean and Non-Polluting Process:
- Induction heating is an environmentally friendly method, as it does not produce flames, fumes, or other pollutants. This makes it a cleaner alternative to gas furnaces or other combustion-based heating methods.
- The absence of direct contact between the workpiece and any external heat source also eliminates the risk of contamination, ensuring the purity and quality of the forged material.
-
Automation and Integration:
- Induction heating systems can be easily integrated into automated forging processes, enabling seamless operation and reducing the need for manual intervention. This is particularly advantageous in modern manufacturing, where automation is key to improving efficiency and reducing labor costs.
- The ability to automate the heating process also enhances safety by minimizing human exposure to high temperatures and hazardous environments.
-
Versatility and Adaptability:
- Induction heating is suitable for a wide range of materials, including metals with low resistivity, refractory metals, and specialized alloys. This versatility makes it a valuable tool for forging applications across various industries.
- The technology can also be adapted for specialized processes, such as surface hardening, brazing, and welding, further expanding its utility in forging operations.
-
Energy Efficiency and Cost Savings:
- Induction heating is highly energy-efficient, as it minimizes heat loss and focuses energy directly on the workpiece. This reduces overall energy consumption and lowers operational costs.
- The efficiency of induction heating also translates into shorter processing times, which further reduces energy usage and enhances the economic viability of forging operations.
-
Future Potential and Technological Advancements:
- As induction heating technology continues to advance, its applications in forging and other industrial processes are expected to expand. Innovations in process optimization and material science will further enhance its capabilities and efficiency.
- The development of new materials and alternative energy solutions will also drive the adoption of induction heating in emerging industries, solidifying its role as a key technology in modern manufacturing.
In conclusion, induction heating is a highly effective and advantageous method for forging, offering precision, efficiency, and environmental benefits. Its ability to provide localized and consistent heating, combined with its adaptability and potential for automation, makes it an ideal choice for modern forging operations.
Summary Table:
Advantage | Description |
---|---|
Direct and Localized Heating | Generates heat directly within the material, reducing heat loss and energy waste. |
Precise Temperature Control | Ensures accurate heating for consistent material properties and structural integrity. |
Rapid Heating | Faster than traditional methods, reducing cycle times and increasing productivity. |
Consistency and Repeatability | Delivers uniform heating for high-quality, reliable forged parts. |
Clean and Non-Polluting | No flames or fumes, making it environmentally friendly and contamination-free. |
Automation and Integration | Easily integrated into automated processes for efficiency and safety. |
Versatility | Suitable for a wide range of materials and specialized processes. |
Energy Efficiency | Minimizes energy consumption and operational costs. |
Future Potential | Continues to advance, expanding applications in modern manufacturing. |
Ready to optimize your forging process with induction heating? Contact us today to learn more!