Induction welding and brazing are distinct processes, though they share some similarities in terms of joining metals. Induction welding involves using electromagnetic induction to generate heat directly within the workpiece, melting the base materials to form a metallurgical bond. Brazing, on the other hand, uses a filler material with a lower melting point than the base materials, which flows into the joint via capillary action and solidifies to form a strong bond. While both methods are used to join metals, they differ in terms of temperature, process mechanics, and the resulting joint characteristics.
Key Points Explained:
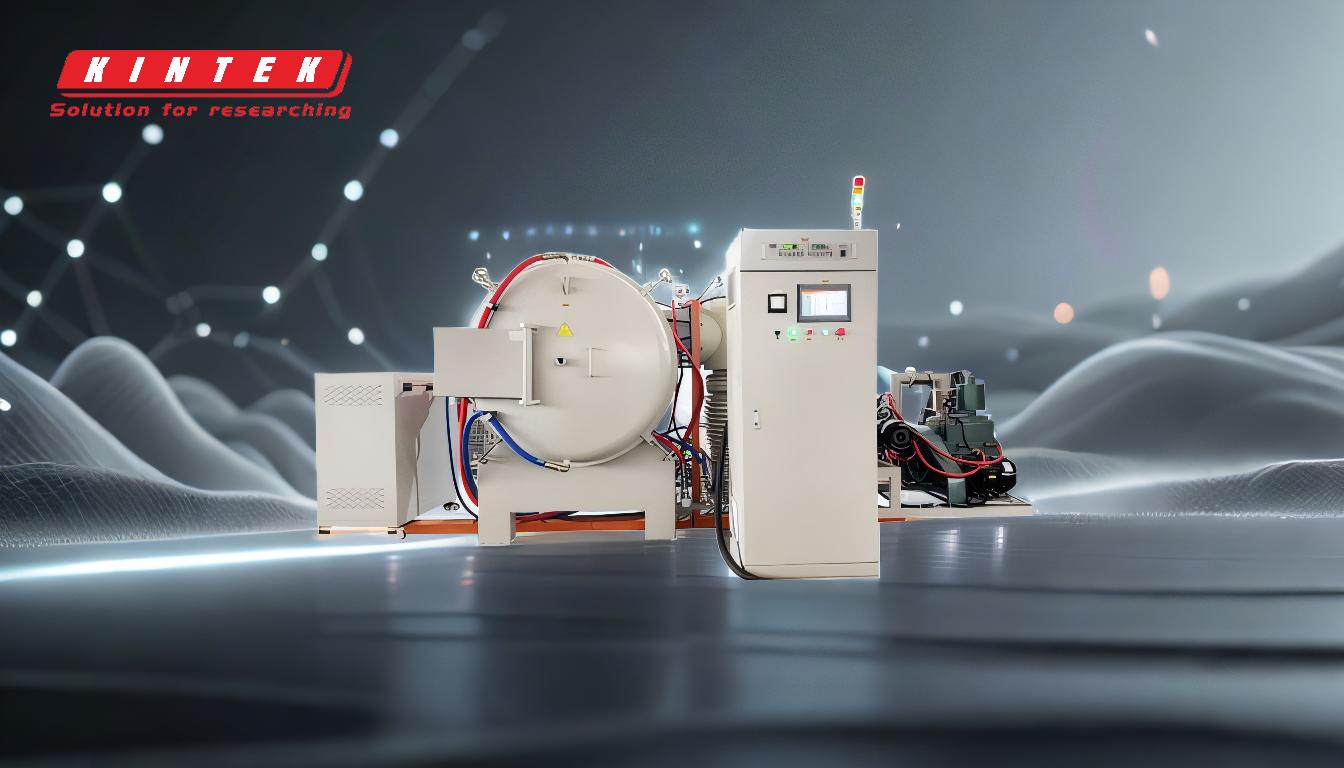
-
Definition and Process Mechanics:
- Induction Welding: This process uses electromagnetic induction to heat the workpiece directly. The heat is generated within the material, allowing for precise control over the welding process. It is commonly used for high-strength applications where a metallurgical bond is required.
- Brazing: Brazing involves heating a filler material (typically above 840°F or 450°C) until it melts and flows into the joint between two base materials. The filler material solidifies upon cooling, creating a strong bond without melting the base materials.
-
Temperature and Heat Application:
- Induction Welding: Requires high temperatures to melt the base materials, often exceeding the melting point of the metals being joined. The heat is localized and intense, which can lead to thermal distortion if not carefully controlled.
- Brazing: Operates at lower temperatures compared to welding, as only the filler material needs to melt. This results in less thermal distortion and stress on the base materials, making it suitable for delicate or complex assemblies.
-
Joint Characteristics:
- Induction Welding: Produces a metallurgical bond, where the base materials are fused together. This results in a joint that is as strong as or stronger than the base materials themselves.
- Brazing: Creates a joint where the filler material bonds to the base materials without melting them. The strength of the joint depends on the filler material and the quality of the bond formed.
-
Applications and Suitability:
- Induction Welding: Ideal for applications requiring high-strength joints, such as in the automotive, aerospace, and manufacturing industries. It is particularly useful for joining metals that are difficult to weld using traditional methods.
- Brazing: Suitable for joining dissimilar metals, thin materials, or components with complex geometries. It is widely used in industries like electronics, plumbing, and HVAC, where precision and minimal thermal distortion are critical.
-
Advantages and Limitations:
- Induction Welding: Offers high precision and control, with the ability to create strong, durable joints. However, it requires specialized equipment and can be more expensive due to the high energy consumption.
- Brazing: Provides a cost-effective solution for joining metals with minimal thermal distortion. It is versatile and can be used with a wide range of materials. However, the joint strength may not match that of a welded joint, and the process may require additional surface preparation.
In conclusion, while induction welding and brazing are both effective methods for joining metals, they serve different purposes and are suited to different applications. Induction welding is best for high-strength, metallurgical bonds, whereas brazing is ideal for creating strong, precise joints with minimal thermal distortion.
Summary Table:
Aspect | Induction Welding | Brazing |
---|---|---|
Process Mechanics | Uses electromagnetic induction to heat the workpiece directly. | Uses a filler material that melts and flows into the joint via capillary action. |
Temperature | High temperatures to melt base materials, often exceeding their melting points. | Lower temperatures, only the filler material melts. |
Joint Characteristics | Produces a metallurgical bond, fusing base materials together. | Creates a bond with filler material, without melting the base materials. |
Applications | Ideal for high-strength joints in automotive, aerospace, and manufacturing industries. | Suitable for joining dissimilar metals, thin materials, or complex geometries. |
Advantages | High precision, strong, durable joints. | Cost-effective, minimal thermal distortion, versatile. |
Limitations | Requires specialized equipment, high energy consumption. | Joint strength may not match welded joints, requires surface preparation. |
Need help choosing the right metal joining process? Contact our experts today for personalized advice!