Yes, it is possible to braze cast iron, and it offers several advantages over other joining methods. Brazing involves heating the cast iron to a temperature below its melting point and using a filler metal with a lower melting point to create a strong joint. This process minimizes the risk of cracking, which is a common issue when welding cast iron due to its brittleness and high carbon content. Additionally, brazing allows for the filling of large gaps and lap joints without the need for external welds, making it a versatile and effective method for joining cast iron components.
Key Points Explained:
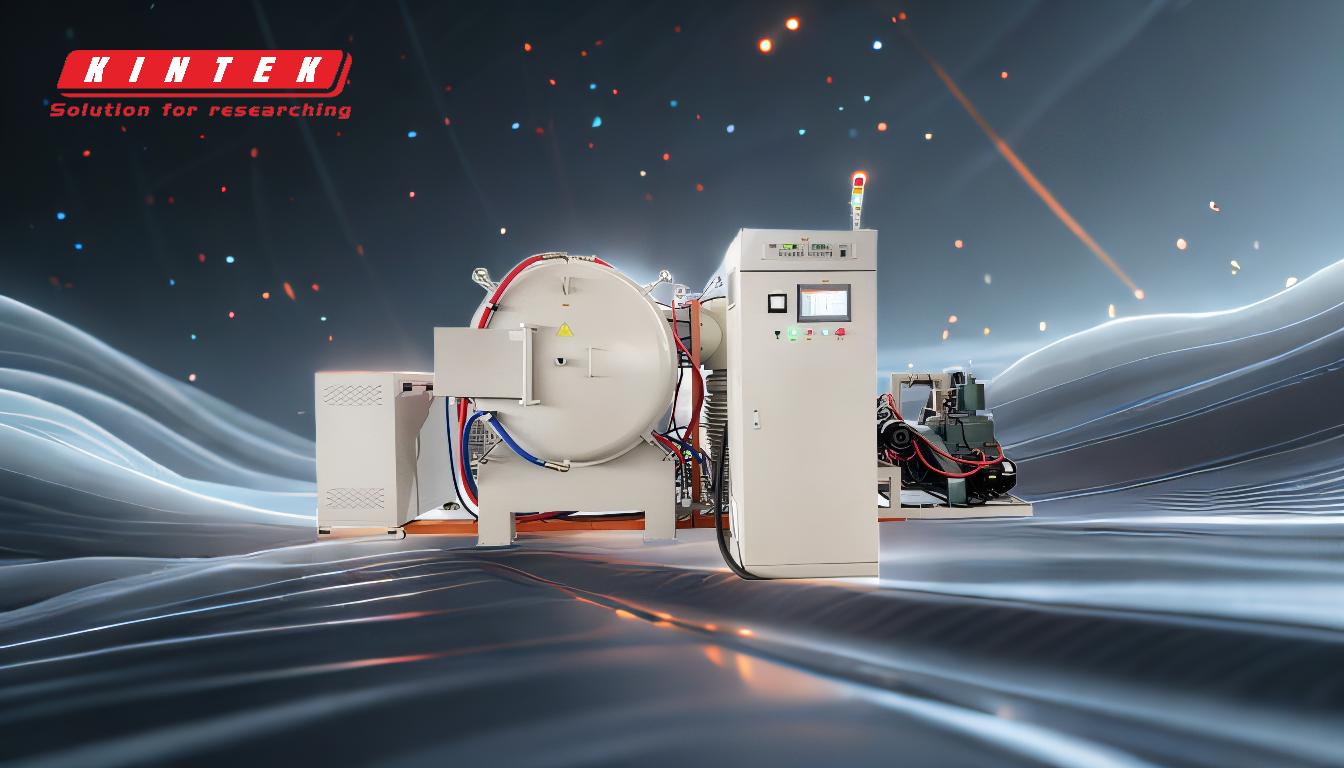
-
Brazing Process for Cast Iron:
- Brazing cast iron involves heating the material to a temperature below its melting point and using a filler metal with a lower melting point to create a joint.
- The filler metal flows into the joint by capillary action, creating a strong bond without melting the base metal.
-
Advantages of Brazing Cast Iron:
- Limited Heating: The base metal does not reach its melting temperature, preserving its properties and reducing the risk of cracking, which is a common issue with welding cast iron.
- Filling Large Joints: Brazing allows for the filling of large lap joints without the need for external welds, making it suitable for applications where large gaps need to be filled.
- Reduced Stress: The lower temperatures used in brazing reduce the thermal stress on the cast iron, minimizing the risk of distortion or warping.
-
Considerations for Brazing Cast Iron:
- Surface Preparation: Proper cleaning and preparation of the cast iron surface are crucial for successful brazing. Any contaminants, such as oil, grease, or rust, must be removed to ensure a strong bond.
- Filler Metal Selection: The choice of filler metal is important. Common filler metals for brazing cast iron include silver-based alloys and copper-based alloys, which have good wetting properties and form strong joints with cast iron.
- Flux Application: A suitable flux must be used to prevent oxidation and promote the flow of the filler metal. The flux should be compatible with both the cast iron and the filler metal.
-
Applications of Brazing Cast Iron:
- Repair and Maintenance: Brazing is often used for repairing cracks or joining broken cast iron parts, such as engine blocks, manifolds, or machine components.
- Manufacturing: In manufacturing, brazing is used to join cast iron parts in assemblies where welding might be impractical due to the risk of cracking or distortion.
-
Comparison with Other Joining Methods:
- Welding: Welding cast iron can lead to cracking due to the high carbon content and brittleness of the material. Brazing, with its lower temperatures, avoids this issue.
- Adhesives: While adhesives can be used to join cast iron, they may not provide the same strength and durability as brazed joints, especially in high-temperature or high-stress applications.
In summary, brazing is a viable and advantageous method for joining cast iron, offering benefits such as reduced risk of cracking, the ability to fill large joints, and lower thermal stress. Proper surface preparation, filler metal selection, and flux application are key to achieving strong and durable brazed joints in cast iron.
Summary Table:
Key Aspect | Details |
---|---|
Process | Heating below melting point; filler metal flows via capillary action. |
Advantages | Reduced cracking, fills large gaps, lowers thermal stress. |
Considerations | Surface prep, filler metal selection, flux application. |
Applications | Repair, maintenance, manufacturing. |
Comparison with Welding | Avoids cracking; lower temperatures reduce distortion. |
Ready to explore brazing solutions for cast iron? Contact our experts today for tailored advice!