PVD (Physical Vapor Deposition) and gold plating are two distinct methods of applying a gold coating to materials, each with its own advantages and limitations. PVD is a high-temperature process that creates a durable, corrosion-resistant, and scratch-resistant coating, making it ideal for applications requiring longevity and resilience. Gold plating, on the other hand, is more cost-effective, offers better coating uniformity, and is suitable for intricate designs due to its ability to cover recessed areas. The choice between PVD and gold plating depends on the specific requirements of the application, such as durability, cost, and design complexity.
Key Points Explained:
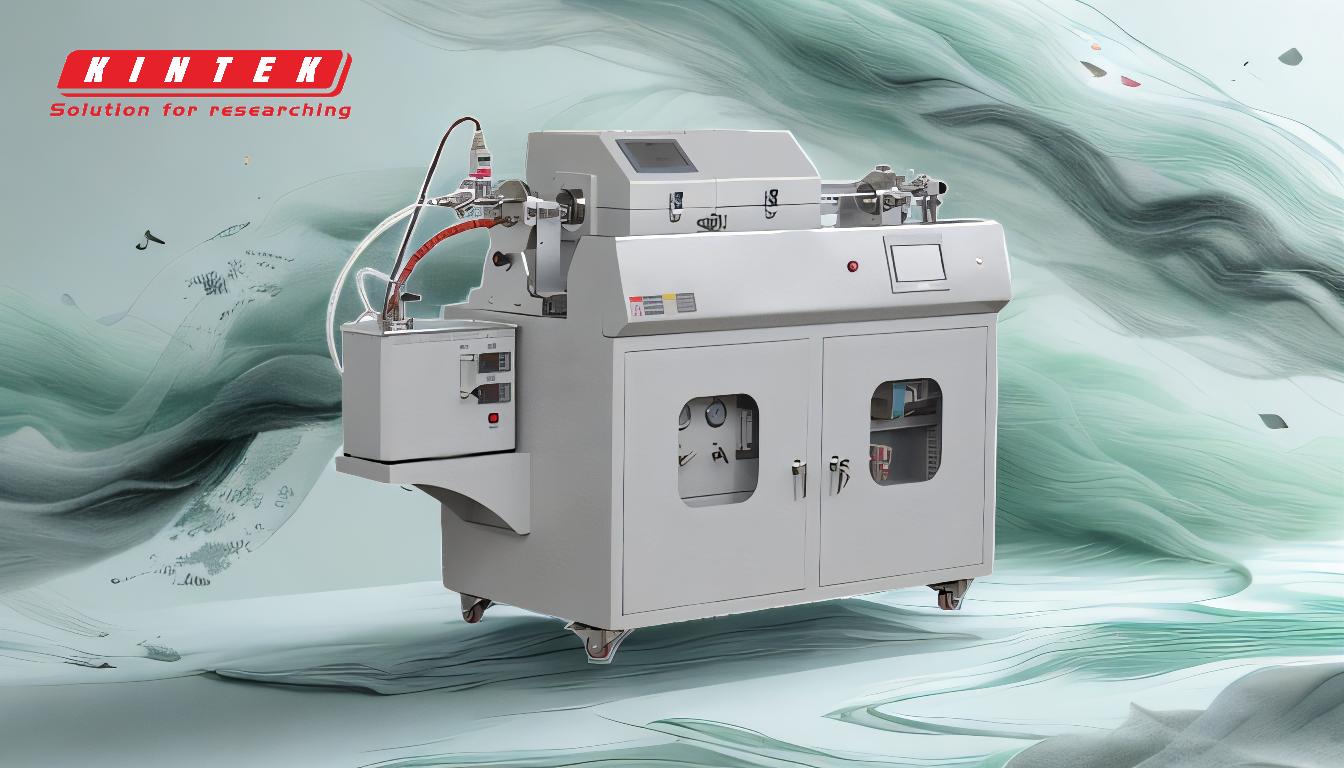
-
Durability and Resistance:
- PVD: PVD coatings are highly durable, offering superior resistance to corrosion, scratching, and tarnishing. The atomic bond formed during the PVD process ensures that the coating adheres securely to the base material, making it long-lasting. PVD-coated jewelry, for example, can last 3 years or more with everyday wear.
- Gold Plating: Gold plating is less durable compared to PVD. Scratches can reveal the base material, and the coating is more prone to wear and tear. Electroplated jewelry typically lasts about 1 year with regular use.
-
Cost and Energy Consumption:
- PVD: The PVD process is generally more expensive due to the high temperatures and sophisticated equipment required. It also consumes more energy compared to gold plating.
- Gold Plating: Gold plating is less expensive and consumes less energy, making it a more cost-effective option for applications where extreme durability is not a primary concern.
-
Coating Uniformity and Flexibility:
- PVD: While PVD provides a durable coating, it may not achieve the same level of uniformity as gold plating, especially in recessed or intricate areas.
- Gold Plating: Gold plating offers better coating uniformity and can cover recessed areas more effectively. It also allows for more flexibility in achieving varied thicknesses and selective plating.
-
Applications and Suitability:
- PVD: PVD is ideal for applications requiring high durability and resistance to environmental factors. It is commonly used in jewelry, cutting tools, and other items that need to withstand harsh conditions.
- Gold Plating: Gold plating is suitable for applications where cost and design flexibility are more important than extreme durability. It is often used in electronics, decorative items, and jewelry where intricate designs are required.
-
Environmental Impact:
- PVD: PVD is considered more environmentally friendly as it does not produce hazardous byproducts. It is also more resistant to high temperatures and abrasions, making it a sustainable choice for certain applications.
- Gold Plating: While gold plating is less energy-intensive, it involves the use of electrolyte solutions and electrical currents, which may have environmental implications depending on the disposal and handling of these materials.
In conclusion, whether PVD is better than gold plating depends on the specific needs of the application. For high-durability, long-lasting, and environmentally friendly solutions, PVD is the superior choice. However, for cost-effective, flexible, and uniform coatings, gold plating may be more appropriate.
Summary Table:
Feature | PVD | Gold Plating |
---|---|---|
Durability | Highly durable, corrosion-resistant, scratch-resistant | Less durable, prone to wear and tear |
Cost | More expensive, higher energy consumption | Cost-effective, lower energy consumption |
Uniformity | May lack uniformity in recessed areas | Better coating uniformity, covers intricate designs effectively |
Applications | Ideal for high-durability needs (jewelry, cutting tools) | Suitable for cost-sensitive, intricate designs (electronics, decor) |
Environmental Impact | Environmentally friendly, no hazardous byproducts | Uses electrolyte solutions, potential environmental implications |
Still unsure which coating method is right for your needs? Contact our experts today for personalized advice!