PVD (Physical Vapor Deposition) coatings are known for their exceptional durability and longevity, but whether they are "permanent" depends on the definition of permanence and the specific application conditions. While PVD coatings can last anywhere from 10 years to hundreds of years, their lifespan is influenced by factors such as the substrate material, coating thickness, environmental conditions, and maintenance. These coatings are highly resistant to corrosion, oxidation, scratching, and wear, making them suitable for demanding applications. However, they are not indestructible and can degrade over time under extreme conditions or improper maintenance. Proper application and care are crucial to maximizing their lifespan.
Key Points Explained:
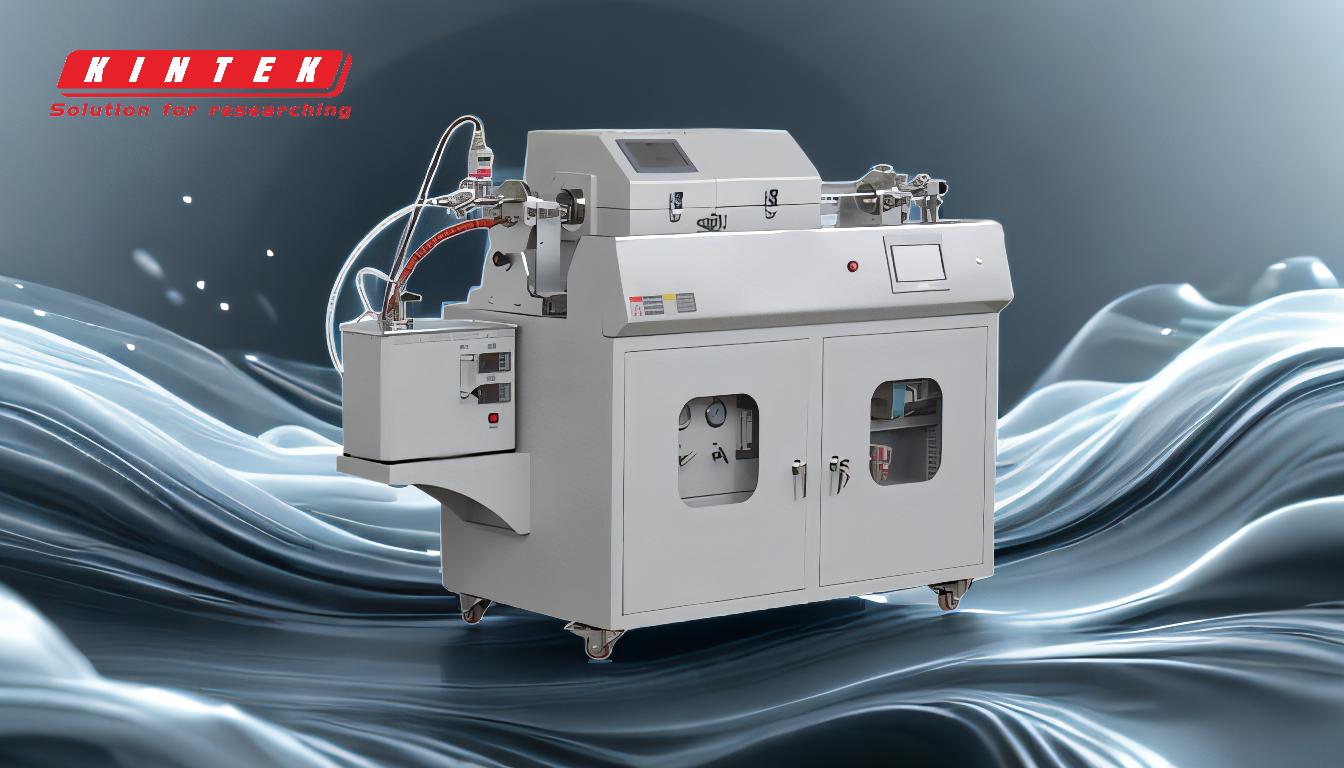
-
Durability and Longevity of PVD Coatings:
- PVD coatings are extremely durable and can last from 10 years to hundreds of years, depending on the application and environmental conditions.
- Their longevity is attributed to their hardness, corrosion resistance, and ability to bond strongly with the substrate.
- For example, in the jewelry industry, PVD coatings can last up to 10 years with proper maintenance.
-
Factors Affecting PVD Coating Lifespan:
- Substrate Material: The underlying material plays a significant role in determining the coating's performance. For instance, TiN coatings on Ti-6Al-4V alloy can increase fatigue limits and endurance.
- Coating Thickness: PVD coatings are very thin (0.5 to 5 microns), but their thinness contributes to their durability and resistance to wear.
- Application Conditions: The vacuum environment during PVD application eliminates contamination, forms a strong bond with the substrate, and prevents oxidation and degradation.
- Environmental Exposure: Exposure to harsh conditions, such as extreme temperatures, moisture, or abrasion, can affect the coating's lifespan.
-
Resistance Properties of PVD Coatings:
- Corrosion and Oxidation Resistance: PVD coatings are highly resistant to corrosion and oxidation, making them ideal for applications in harsh environments.
- Scratch and Wear Resistance: The hardness of PVD coatings provides excellent resistance to scratching and abrasion, ensuring long-lasting protection.
- Temperature and Impact Tolerance: These coatings can withstand high temperatures and have robust impact strength, making them suitable for demanding industrial applications.
-
Limitations of PVD Coatings:
- While PVD coatings are highly durable, they are not indestructible. Over time, they can degrade under extreme conditions or improper maintenance.
- The thinness of the coating, while beneficial for durability, can also make it susceptible to damage if subjected to excessive mechanical stress or abrasion.
-
Applications and Maintenance:
- PVD coatings are widely used in industries such as jewelry, automotive, aerospace, and manufacturing due to their durability and protective properties.
- Proper application and maintenance are critical to maximizing the lifespan of PVD coatings. For example, avoiding exposure to harsh chemicals or abrasive materials can help preserve the coating.
In conclusion, while PVD coatings are not technically "permanent," they offer exceptional durability and longevity under the right conditions. Their resistance to corrosion, oxidation, and wear makes them a superior choice for many applications, but their lifespan ultimately depends on factors such as substrate material, coating thickness, and environmental exposure. Proper application and maintenance are key to ensuring their long-term performance.
Summary Table:
Key Aspect | Details |
---|---|
Lifespan | 10 years to hundreds of years, depending on conditions |
Resistance Properties | Corrosion, oxidation, scratching, wear, and high-temperature resistance |
Factors Affecting Lifespan | Substrate material, coating thickness, environmental conditions, maintenance |
Applications | Jewelry, automotive, aerospace, manufacturing |
Limitations | Susceptible to degradation under extreme conditions or improper maintenance |
Maximize the lifespan of your PVD coatings—contact our experts today for tailored solutions!