PVD (Physical Vapor Deposition) finish is generally considered good due to its ability to produce durable, high-quality coatings with excellent adhesion and uniformity. It is particularly advantageous for temperature-sensitive materials, as it operates at lower temperatures compared to CVD (Chemical Vapor Deposition). PVD coatings are also environmentally friendly, as they do not involve harmful chemicals or produce atmospheric pollution. However, PVD does have some limitations, such as the need for very low vacuum conditions and potential material restrictions. Overall, PVD is a versatile and effective finishing method, especially for applications requiring precise, thin-film coatings.
Key Points Explained:
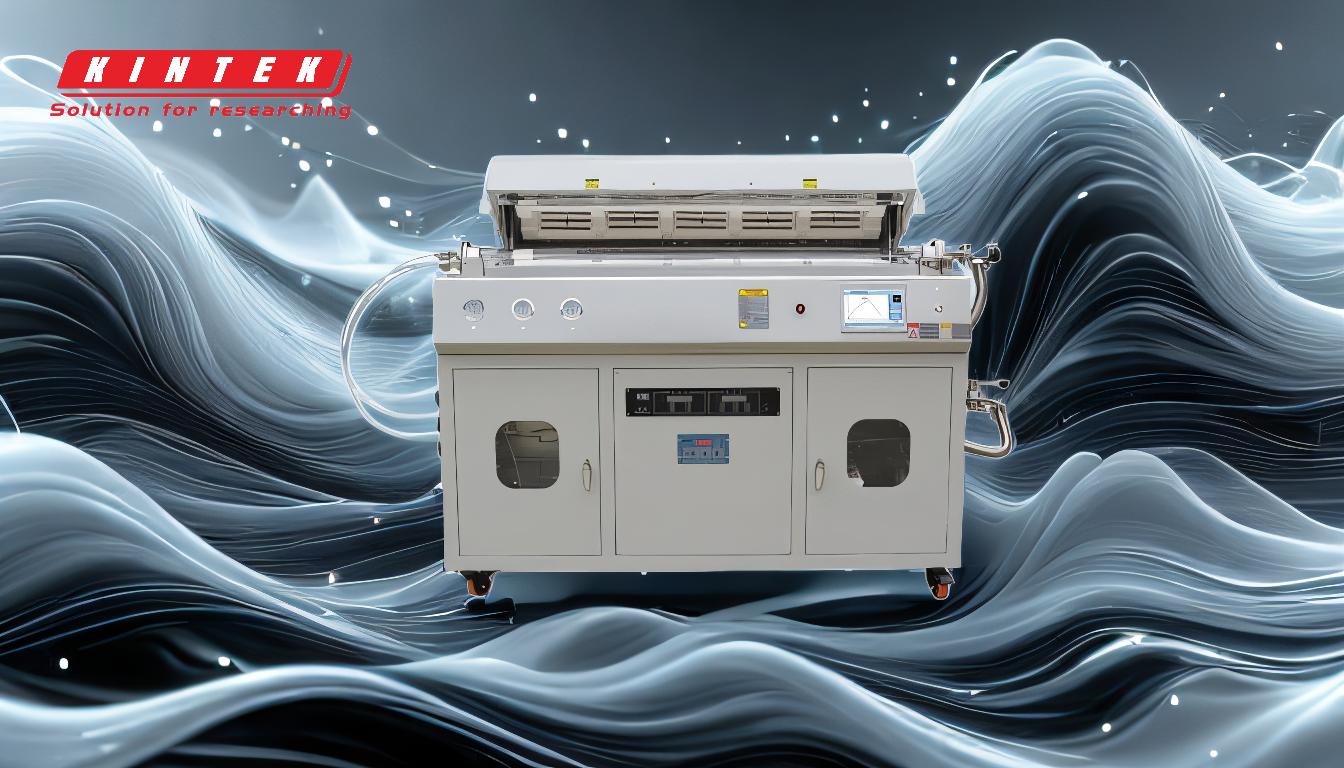
-
Durability and Quality of PVD Coatings
- PVD coatings are known for their durability and high-quality finish. They provide excellent adhesion to the substrate, ensuring long-lasting performance even under harsh conditions.
- The process allows for the deposition of thin films ranging from a few nanometers to several microns in thickness, making it suitable for a wide range of applications.
-
Lower Temperature Processing
- Unlike CVD, which requires heating the substrate to temperatures as high as 900 °C, PVD operates at much lower temperatures. This makes it ideal for coating temperature-sensitive materials that would otherwise degrade under high heat.
- This lower temperature processing also reduces the risk of thermal damage to the substrate, preserving its structural integrity.
-
Environmental Benefits
- PVD is an environmentally friendly process. It does not involve the use of harmful chemicals or produce atmospheric pollution, making it a sustainable choice for coating applications.
- The higher material utilization in PVD also minimizes waste, contributing to its eco-friendly profile.
-
Limitations of PVD
- One of the main disadvantages of PVD is the need for very low vacuum conditions, which can increase the complexity and cost of the process.
- PVD may also have limitations when it comes to coating certain materials, as not all materials are compatible with the process.
- Additionally, there can be unnecessary coating in the chamber, which may require additional cleaning and maintenance.
-
Comparison with CVD
- While CVD has the advantage of less material waste due to selective heating, it is not suitable for temperature-sensitive materials. PVD fills this gap by providing a low-temperature alternative.
- Both PVD and CVD have their own strengths and weaknesses, and the choice between the two often depends on the specific requirements of the application.
-
Applications of PVD
- PVD is widely used in industries such as aerospace, automotive, medical devices, and electronics, where high-performance coatings are essential.
- Its ability to produce precise, uniform coatings makes it ideal for applications requiring high levels of accuracy and durability.
In summary, PVD finish is a highly effective and versatile method for producing durable, high-quality coatings, especially for temperature-sensitive materials. While it does have some limitations, its environmental benefits and suitability for a wide range of applications make it a preferred choice in many industries.
Summary Table:
Aspect | Details |
---|---|
Durability | High-quality, long-lasting coatings with excellent adhesion. |
Temperature Sensitivity | Operates at lower temperatures, ideal for heat-sensitive materials. |
Environmental Benefits | No harmful chemicals or atmospheric pollution; minimizes waste. |
Limitations | Requires very low vacuum conditions; material compatibility restrictions. |
Applications | Aerospace, automotive, medical devices, electronics, and more. |
Ready to explore how PVD coatings can enhance your projects? Contact us today for expert advice!