PVD (Physical Vapor Deposition) coatings are indeed scratch-resistant, thanks to their high hardness and durability. These coatings are applied at the atomic level, allowing precise control over their properties, such as hardness, density, and adhesion. PVD coatings are four times harder than chrome, making them highly resistant to scratches, corrosion, and wear. Their hardness ranges from 1500 to 4500 HV (Vickers), significantly higher than many traditional materials like carbon steel or nickel-plated steel. Additionally, PVD coatings bond strongly to the substrate, ensuring long-lasting performance even in harsh environments. Their low maintenance requirements and decorative finishes further enhance their appeal for both functional and aesthetic applications.
Key Points Explained:
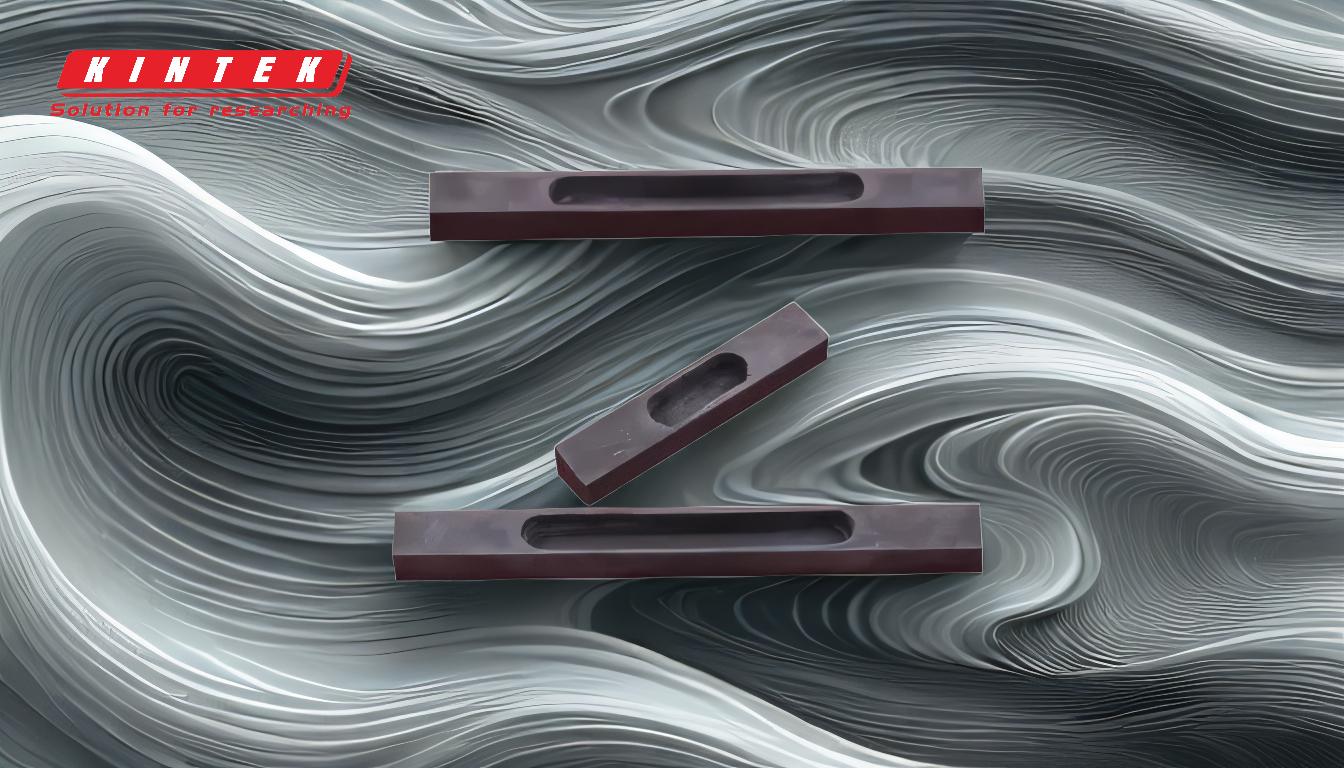
-
High Hardness of PVD Coatings:
- PVD coatings have a hardness range of 1500–4500 HV (Vickers), which is significantly higher than many traditional materials. For comparison:
- Carbon steel: ~250 HV (25 HRC).
- Nickel and chrome-plated steel: 600–1000 HV.
- This high hardness contributes to scratch resistance, as harder materials are less prone to deformation or damage from abrasion.
- PVD coatings have a hardness range of 1500–4500 HV (Vickers), which is significantly higher than many traditional materials. For comparison:
-
Comparison to Chrome:
- PVD coatings are four times harder than chrome, making them more resistant to scratches and wear.
- This increased hardness also enhances their durability in harsh environments, such as coastal areas or industrial settings.
-
Atomic-Level Application:
- PVD coatings are applied at the atomic level, allowing precise control over their structure, density, and stoichiometry.
- This precision enables the creation of coatings with specific attributes, such as high hardness, lubricity, and adhesion, which contribute to scratch resistance.
-
Strong Adhesion to Substrate:
- PVD coatings bond strongly to the substrate, even penetrating it slightly, which ensures long-lasting adhesion.
- This strong bond prevents chipping or peeling, further enhancing scratch resistance and overall durability.
-
Wear and Corrosion Resistance:
- PVD coatings are highly resistant to wear and corrosion, making them suitable for applications exposed to harsh conditions.
- Their low coefficient of friction and chemical resistance also contribute to their longevity and scratch resistance.
-
Environmental and Maintenance Benefits:
- PVD coatings are environmentally friendly and require low maintenance.
- Their resistance to tarnishing, fading, and scratching ensures they retain their appearance and functionality over time.
-
Applications and Versatility:
- PVD coatings are ideal for both functional and decorative purposes, offering a brilliant finish alongside superior scratch resistance.
- They are widely used in industries such as automotive, aerospace, and consumer goods, where durability and aesthetics are critical.
In summary, PVD coatings are highly scratch-resistant due to their exceptional hardness, strong adhesion to substrates, and precise atomic-level application. These properties make them a superior choice for applications requiring durability, longevity, and aesthetic appeal.
Summary Table:
Property | PVD Coatings | Traditional Materials |
---|---|---|
Hardness (HV) | 1500–4500 | Carbon steel: ~250 |
Scratch Resistance | High | Low to moderate |
Wear and Corrosion Resistance | Excellent | Moderate |
Adhesion to Substrate | Strong | Variable |
Maintenance Requirements | Low | High |
Applications | Automotive, Aerospace, Consumer Goods | General use |
Discover how PVD coatings can enhance your product's durability and aesthetics—contact us today!