Spark plasma sintering (SPS), also known as field-assisted sintering technique (FAST), is a modern sintering method that uses electrical currents to achieve rapid and efficient densification of materials. Unlike traditional sintering, which relies solely on external heating, SPS combines plasma activation, hot pressing, and resistance heating. This results in faster heating and cooling rates, shorter holding times, and lower sintering temperatures. The process involves the generation of localized heat through electrical discharge between powder particles, leading to surface activation, purification, and fusion. SPS is particularly advantageous for sintering difficult materials, such as ceramics and cemented carbides, without the need for additional additives. It produces materials with fine, uniform microstructures and high density, making it a superior alternative to conventional sintering methods.
Key Points Explained:
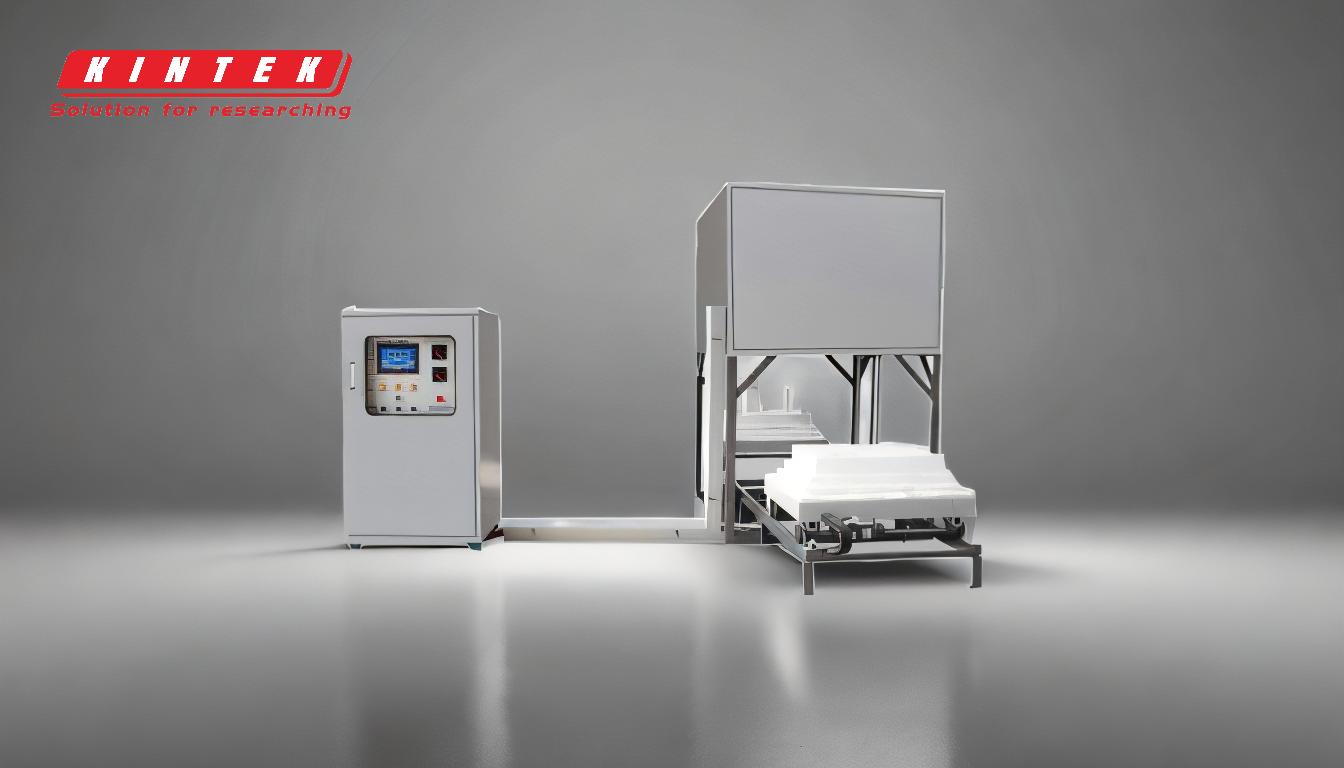
-
Definition and Mechanism of Spark Plasma Sintering (SPS):
- SPS is a sintering technique that uses electrical currents (DC, pulsed DC, or AC) to heat materials both internally and externally. The electrical current passes through a conductive die (typically graphite) and, if the material is conductive, through the ceramic itself. This dual heating mechanism allows for rapid and uniform heating.
- The process integrates plasma activation, hot pressing, and resistance heating. Joule heat generated from hot-pressed sintering, plastic deformation caused by pressure, and the generation of DC pulse voltage between powder particles are key mechanisms in SPS.
-
Unique Features of SPS:
- Fast Heating and Cooling Rates: SPS achieves much faster heating and cooling rates compared to traditional sintering methods. This is due to the direct application of electrical current, which heats the material internally and externally simultaneously.
- Short Sintering Time: Traditional sintering can take hours or even days, whereas SPS can complete the process in just a few minutes.
- Low Sintering Temperature: SPS allows densification at temperatures several hundred degrees lower than conventional sintering, which helps in preserving the microstructure of the material.
- Uniform Heating: The electrical discharge between particles ensures that heating is uniformly distributed throughout the sample volume, leading to consistent material properties.
- Energy Efficiency: SPS is more energy-efficient due to its rapid processing times and lower required temperatures.
-
Advantages of SPS:
- Simple Operation: SPS equipment is relatively easy to operate, with low technical requirements.
- High Production Efficiency: The fast sintering speed and short processing times make SPS highly efficient for industrial applications.
- Improved Material Properties: SPS inhibits the growth of crystal grains, maintaining the microstructure of the original particles. This results in a fine, uniform structure and high density in the final product.
- Versatility: SPS can sinter a wide range of materials, including difficult-to-sinter ceramics and cemented carbides, without the need for additional additives.
-
Applications of SPS:
- SPS is particularly useful for sintering materials that are challenging to densify using conventional methods. This includes special ceramics, cemented carbides, and other powder materials.
- The ability to sinter materials without additives makes SPS ideal for producing high-purity components with enhanced mechanical properties.
-
Comparison with Traditional Sintering:
- Time Efficiency: Traditional sintering can take several hours or even days, while SPS completes the process in minutes.
- Temperature Requirements: SPS operates at significantly lower temperatures, reducing the risk of material degradation.
- Microstructure Control: SPS provides better control over the microstructure, resulting in materials with superior mechanical properties.
In summary, spark plasma sintering is a highly efficient and versatile sintering technique that offers significant advantages over traditional methods. Its ability to rapidly sinter materials at lower temperatures while maintaining fine microstructures makes it an invaluable tool in materials science and engineering.
Summary Table:
Aspect | Spark Plasma Sintering (SPS) | Traditional Sintering |
---|---|---|
Heating Mechanism | Combines plasma activation, hot pressing, and resistance heating | Relies solely on external heating |
Heating/Cooling Rate | Extremely fast | Slow |
Sintering Time | Minutes | Hours to days |
Temperature | Lower (by several hundred degrees) | Higher |
Microstructure | Fine, uniform, and high density | Less control over microstructure |
Energy Efficiency | High | Lower |
Applications | Ideal for ceramics, cemented carbides, and difficult-to-sinter materials | Limited for challenging materials |
Discover how spark plasma sintering can enhance your material processing—contact our experts today!