Sputtering deposition is a specific type of Physical Vapor Deposition (PVD). While all sputtering processes fall under the broader category of PVD, not all PVD methods are sputtering. PVD encompasses various techniques, including sputtering, thermal evaporation, and electron-beam evaporation, each differing in how the source material is vaporized and deposited onto a substrate. Sputtering uniquely uses energetic ions to dislodge atoms from a target material, creating a vapor that condenses into a thin film on the substrate. This method avoids melting the material and operates at lower temperatures, making it suitable for temperature-sensitive applications. Other PVD methods, like thermal evaporation, rely on heating the material to generate vapor.
Key Points Explained:
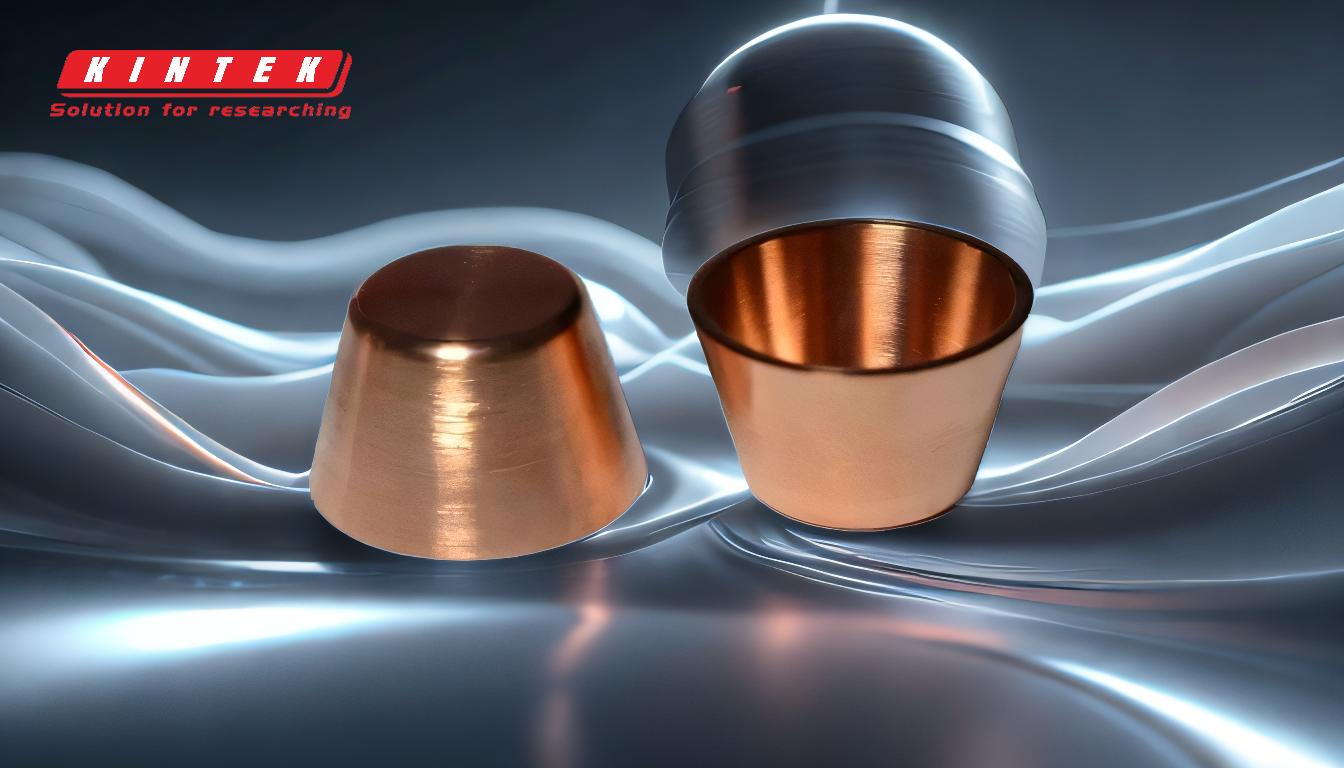
-
Sputtering Deposition is a Subset of PVD
- Sputtering deposition is one of several techniques within the Physical Vapor Deposition (PVD) family. PVD is a broad term that includes any process where a solid material is vaporized in a vacuum and then deposited as a thin film on a substrate. Sputtering is distinct because it uses energetic ions to eject atoms from a target material, rather than relying on thermal energy or evaporation.
-
Mechanism of Sputtering vs. Other PVD Methods
- Sputtering: Involves bombarding a target material with energetic ions (typically argon ions) in a plasma environment. The ions physically knock atoms off the target, creating a vapor that condenses onto the substrate. This process does not require melting the target material.
- Other PVD Methods (e.g., Thermal Evaporation): These methods rely on heating the source material until it vaporizes. The vapor then condenses on the substrate to form a thin film. This process often involves higher temperatures compared to sputtering.
-
Temperature Considerations
- Sputtering operates at relatively low temperatures, making it suitable for coating temperature-sensitive materials such as plastics, organics, and certain metals.
- Other PVD methods, like thermal evaporation, require higher temperatures to vaporize the source material, which can limit their use with heat-sensitive substrates.
-
Material Compatibility
- Sputtering is versatile and can be used with a wide range of materials, including metals, ceramics, and alloys. The process does not rely on the material's melting point, allowing for the deposition of materials that are difficult to evaporate thermally.
- Thermal evaporation and similar PVD methods are better suited for materials that can be easily vaporized at high temperatures.
-
Process Characteristics
- Sputtering: A dry, low-temperature process that uses gases (typically argon) to generate a plasma. The ejected atoms from the target material form a uniform and dense thin film on the substrate.
- Other PVD Methods: Often involve higher temperatures and may require more complex equipment, such as electron beams or resistive heating elements, to achieve vaporization.
-
Applications
- Sputtering is widely used in industries requiring precise and uniform thin films, such as semiconductor manufacturing, optical coatings, and decorative finishes. Its ability to coat temperature-sensitive materials expands its applicability.
- Other PVD methods are commonly used in applications where high-temperature processes are acceptable, such as metallization in microelectronics or protective coatings on tools.
-
Advantages of Sputtering Over Other PVD Methods
- Lower process temperatures reduce the risk of damaging heat-sensitive substrates.
- Better adhesion and uniformity of the deposited film due to the energetic nature of the sputtered atoms.
- Ability to deposit a wider variety of materials, including those with high melting points.
-
Limitations of Sputtering
- Sputtering can be slower compared to thermal evaporation, especially for materials with low sputtering yields.
- The process requires a vacuum environment and specialized equipment, which can increase costs.
In summary, while sputtering deposition is a type of PVD, it is distinct from other PVD methods due to its unique mechanism of using energetic ions to dislodge atoms from a target material. This makes it a preferred choice for applications requiring low-temperature processing and compatibility with a wide range of materials.
Summary Table:
Aspect | Sputtering Deposition | Other PVD Methods |
---|---|---|
Mechanism | Uses energetic ions to dislodge atoms from a target material. | Relies on heating the source material to generate vapor. |
Temperature | Operates at lower temperatures, suitable for heat-sensitive materials. | Requires higher temperatures, limiting use with heat-sensitive substrates. |
Material Compatibility | Compatible with metals, ceramics, and alloys; does not rely on melting point. | Best suited for materials that can be easily vaporized at high temperatures. |
Applications | Used in semiconductor manufacturing, optical coatings, and decorative finishes. | Common in metallization and protective coatings where high temperatures are acceptable. |
Advantages | Lower temperatures, better adhesion, and ability to deposit a wide range of materials. | Faster for materials with low sputtering yields. |
Limitations | Slower for some materials; requires vacuum environment and specialized equipment. | Higher temperatures may damage heat-sensitive substrates. |
Discover how sputtering deposition can enhance your thin film processes—contact our experts today!