Compression molding is a widely used manufacturing process, particularly in industries like automotive manufacturing, where it is employed to create interior components and trim covers. This method involves using heat and compression to shape raw materials such as metal, plastic compounds, or rubber into molds. While it offers several advantages, such as cost-effectiveness and efficiency, it also comes with its own set of challenges, including the risk of defects and potential damage to molds. Understanding both the advantages and disadvantages of compression molding is crucial for making informed decisions in manufacturing processes.
Key Points Explained:
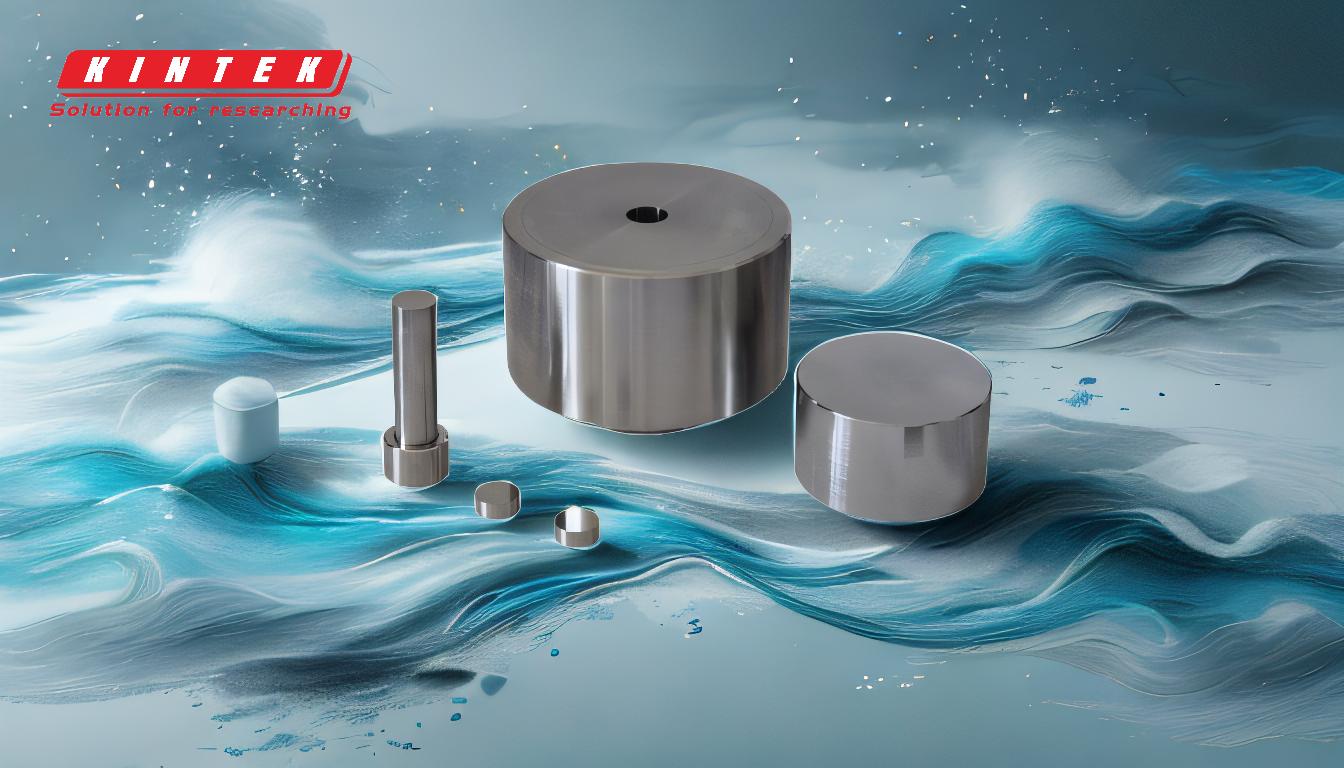
-
Advantages of Compression Molding:
- Cost-Effectiveness: Compression molding is known for its ability to keep overall project costs to a minimum. The process reduces material waste and labor costs, making it an economical choice for large-scale production.
- Efficiency: Supported by hydraulic presses, compression molding is a fast and efficient process. The use of hydraulic presses ensures that the material is evenly distributed and that the mold is filled quickly and accurately.
- Versatility: This method is suitable for a wide range of materials, including metal, plastic compounds, and rubber. It is particularly ideal for creating interior applications and trim covers in automotive manufacturing.
- Minimal Material Waste: The process is designed to minimize material waste, as excess material flows out of special grooves in the mold, known as mold flash. This helps in reducing the overall cost of production.
-
Disadvantages of Compression Molding:
- Risk of Defects: One of the primary challenges in compression molding is accurately cutting or weighing enough rubber stock for each cavity. Too little stock or incorrect placement can lead to defects such as flow lines, blisters, or unfilled parts. Excessive rubber can cause heavy flash, which is difficult to remove.
- Potential Damage to Molds: Molds can be damaged during the compression molding process. This can occur due to the high pressure and temperature required to shape the material, leading to increased maintenance costs and potential downtime.
- Higher Individual Part Costs: While the overall project costs can be kept to a minimum, individual part costs in compression molding can be higher compared to other techniques. This is due to the precision required in the process and the potential for defects that may require rework or additional quality control measures.
- Complexity in Material Handling: The process requires well-shaped un-branched rubber stock to be placed in each cavity of the mold. Any deviation in the shape or placement of the stock can lead to defects, making the material handling process more complex and time-consuming.
-
Applications and Considerations:
- Automotive Industry: Compression molding is widely used in the automotive industry for manufacturing various interior components, such as sun visors and gear knobs. The process is ideal for creating parts that require a high level of detail and precision.
- Material Selection: The choice of material is crucial in compression molding. Materials must be able to withstand the high pressure and temperature required for the process. Additionally, the material must be able to flow evenly to fill the mold cavity without causing defects.
- Process Optimization: To maximize the benefits of compression molding, it is essential to optimize the process. This includes accurately measuring and placing the material, maintaining the correct temperature and pressure, and ensuring that the molds are in good condition to prevent damage.
In conclusion, compression molding offers several advantages, including cost-effectiveness, efficiency, and versatility, making it a popular choice for various manufacturing applications, particularly in the automotive industry. However, it also presents challenges such as the risk of defects, potential damage to molds, and higher individual part costs. Understanding these advantages and disadvantages is crucial for making informed decisions and optimizing the compression molding process for specific applications.
Summary Table:
Aspect | Advantages | Disadvantages |
---|---|---|
Cost-Effectiveness | Reduces material waste and labor costs, ideal for large-scale production. | Higher individual part costs due to precision and potential defects. |
Efficiency | Fast and efficient with hydraulic presses for even material distribution. | Risk of defects like flow lines, blisters, or unfilled parts. |
Versatility | Suitable for metals, plastics, and rubber; ideal for automotive components. | Complex material handling and potential damage to molds. |
Material Waste | Minimizes waste through mold flash grooves. | Heavy flash from excessive material can be difficult to remove. |
Ready to optimize your compression molding process? Contact our experts today for tailored solutions!