Deposition systems are critical tools in the semiconductor industry, used to deposit thin films of materials onto substrates to create the intricate layers required for semiconductor devices. These systems are essential for processes like creating conductive pathways, insulating layers, and other functional components in integrated circuits (ICs) and other microelectronic devices. Deposition systems can be categorized into two main types: physical vapor deposition (PVD) and chemical vapor deposition (CVD). PVD involves physically transferring material from a source to a substrate, while CVD relies on chemical reactions to deposit materials. Both methods have unique advantages and are chosen based on the specific requirements of the semiconductor manufacturing process.
Key Points Explained:
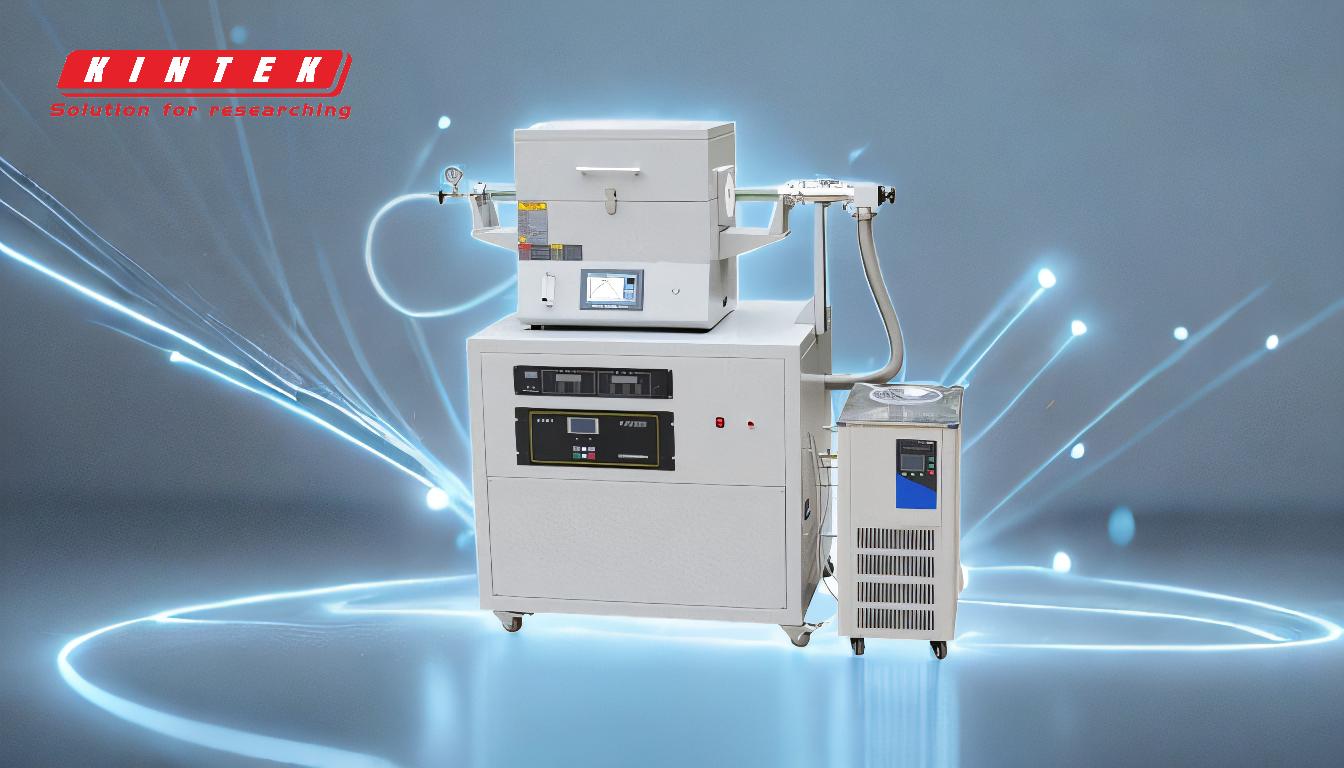
-
Purpose of Deposition Systems:
- Deposition systems are used to create thin films of materials on semiconductor wafers. These films can be conductive, insulating, or semiconducting, depending on the application.
- They are essential for building the layered structures in ICs, such as transistors, capacitors, and interconnects.
-
Types of Deposition Systems:
-
Physical Vapor Deposition (PVD):
- PVD systems deposit materials by physically transferring atoms from a source to a substrate. Common PVD techniques include sputtering and evaporation.
- Sputtering involves bombarding a target material with ions to eject atoms, which then deposit onto the substrate.
- Evaporation heats the material until it vaporizes, and the vapor condenses onto the substrate.
- PVD is often used for depositing metals and alloys, such as aluminum, copper, and titanium.
-
Chemical Vapor Deposition (CVD):
- CVD systems use chemical reactions to deposit materials. Precursor gases are introduced into a reaction chamber, where they react to form a solid film on the substrate.
- CVD can produce high-quality, uniform films and is used for depositing materials like silicon dioxide, silicon nitride, and polysilicon.
- Variations of CVD include plasma-enhanced CVD (PECVD) and low-pressure CVD (LPCVD), which offer enhanced control over film properties.
-
-
Applications in Semiconductor Manufacturing:
- Interconnects: Deposition systems are used to create the conductive pathways that connect different components in an IC. Metals like copper and aluminum are commonly deposited using PVD.
- Insulating Layers: Materials like silicon dioxide and silicon nitride are deposited using CVD to create insulating layers between conductive elements.
- Gate Electrodes: Polysilicon and metal gates are deposited using CVD and PVD, respectively, to form the gate electrodes in transistors.
- Barrier Layers: Thin films of materials like titanium nitride are deposited to prevent diffusion between layers and improve adhesion.
-
Key Considerations for Choosing a Deposition System:
- Material Compatibility: The choice of deposition system depends on the material to be deposited. For example, PVD is preferred for metals, while CVD is better suited for dielectric materials.
- Film Quality: CVD typically produces films with better step coverage and uniformity, making it ideal for complex geometries.
- Process Temperature: CVD often requires higher temperatures, which may not be suitable for temperature-sensitive substrates.
- Throughput and Cost: PVD systems generally offer higher throughput and lower cost, making them attractive for high-volume manufacturing.
-
Emerging Trends in Deposition Systems:
- Atomic Layer Deposition (ALD): ALD is a precise deposition technique that allows for the deposition of ultra-thin, highly uniform films. It is gaining popularity for applications requiring precise thickness control, such as in advanced memory devices.
- 3D Deposition: As semiconductor devices become more complex, deposition systems are being adapted to handle 3D structures, such as fin field-effect transistors (FinFETs) and 3D NAND flash memory.
- Eco-Friendly Processes: There is a growing focus on developing deposition processes that use less hazardous chemicals and reduce environmental impact.
-
Challenges in Deposition Technology:
- Uniformity and Defects: Achieving uniform film thickness and minimizing defects is critical, especially as device dimensions shrink.
- Material Purity: Contaminants in deposited films can degrade device performance, so maintaining high material purity is essential.
- Integration with Other Processes: Deposition systems must be compatible with other semiconductor manufacturing processes, such as lithography and etching.
In summary, deposition systems are indispensable in the semiconductor industry, enabling the creation of the complex, multi-layered structures that form the backbone of modern electronics. The choice between PVD and CVD depends on the specific requirements of the material and application, and ongoing advancements in deposition technology continue to push the boundaries of semiconductor manufacturing.
Summary Table:
Aspect | Details |
---|---|
Purpose | Create thin films for conductive, insulating, and semiconducting layers. |
Types | PVD (Physical Vapor Deposition) and CVD (Chemical Vapor Deposition). |
Applications | Interconnects, insulating layers, gate electrodes, and barrier layers. |
Key Considerations | Material compatibility, film quality, process temperature, throughput, cost. |
Emerging Trends | ALD, 3D deposition, eco-friendly processes. |
Challenges | Uniformity, material purity, integration with other processes. |
Discover the right deposition system for your semiconductor needs—contact our experts today!