A rotary kiln is divided into distinct zones based on the temperature and the specific processes occurring within each zone. These zones are designed to optimize the thermal treatment of materials, ensuring efficient heating, drying, or chemical reactions. The primary zones include the pre-heating zone, high-temperature heating zone, and, in some cases, additional zones like drying and roasting sections, depending on the material being processed. Each zone is carefully controlled to achieve the desired outcome, with temperature settings tailored to the specific requirements of the process.
Key Points Explained:
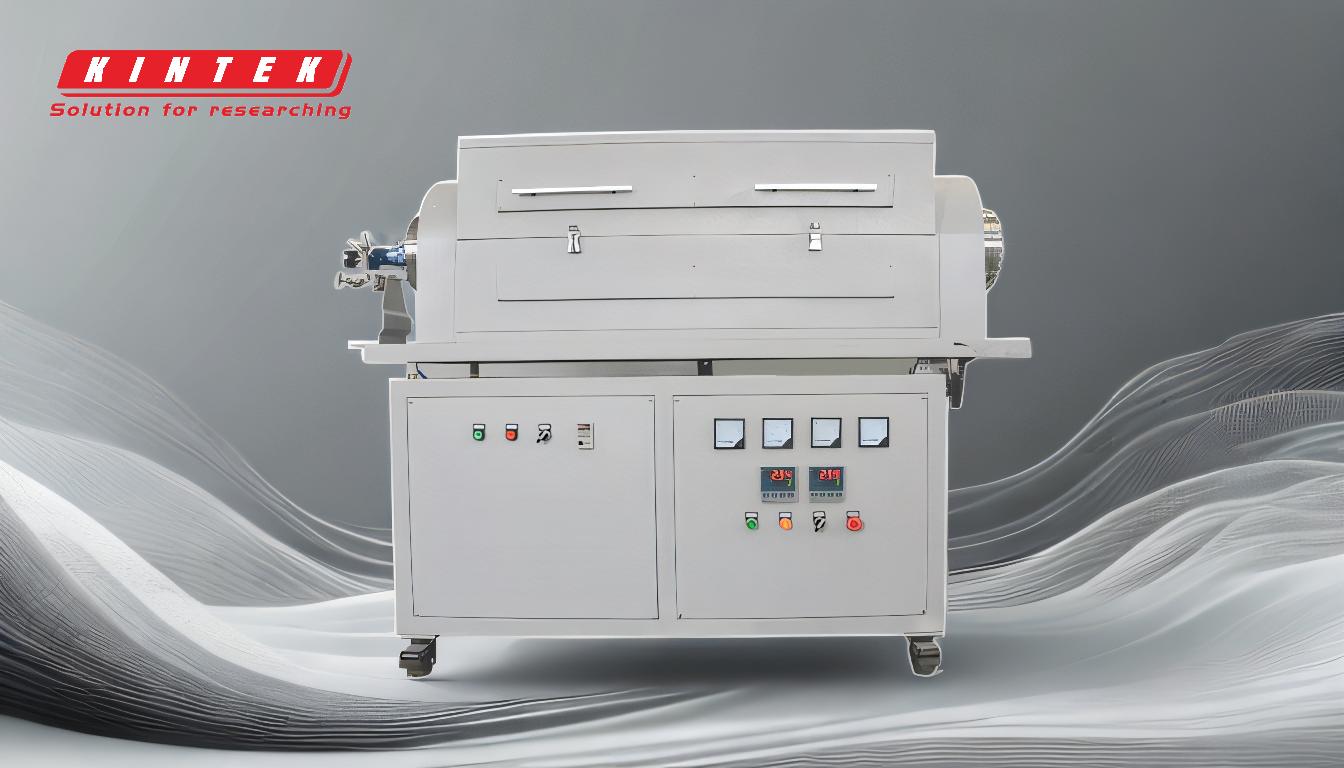
-
Pre-Heating Zone:
- Function: This zone is responsible for gradually increasing the temperature of the material before it enters the high-temperature zone. It helps in reducing thermal shock and ensures uniform heating.
- Temperature Range: The pre-heating zone typically operates at lower temperatures compared to the high-temperature zone, often ranging from ambient temperature to a few hundred degrees Celsius.
- Process: In this zone, moisture is evaporated, and the material is prepared for the more intense heating that occurs in the subsequent zones. This is particularly important for materials that are sensitive to rapid temperature changes.
- Customization: The temperature and duration in the pre-heating zone can be adjusted based on the specific material being processed, ensuring optimal conditions for the next stages.
-
High-Temperature Heating Zone:
- Function: This is the core zone where the material undergoes the most significant thermal treatment. It is designed to achieve the highest temperatures required for the process, such as calcination, sintering, or chemical reactions.
- Temperature Range: The high-temperature zone can reach temperatures well above 1000°C, depending on the material and the process requirements.
- Process: In this zone, the material is subjected to intense heat, which may cause chemical changes, phase transitions, or the removal of volatile components. The design of this zone ensures that the heat is evenly distributed to avoid hotspots or uneven processing.
- Customization: Similar to the pre-heating zone, the high-temperature zone can be divided into multiple sub-zones, each with its own temperature setting. This allows for precise control over the heating process, ensuring that the material is processed correctly.
-
Drying Section (Optional):
- Function: In some rotary kilns, especially those used for processing materials like nickel ore, a dedicated drying section may be included. This section is designed to remove moisture from the material before it enters the heating zones.
- Temperature Range: The drying section operates at relatively low temperatures, typically below 200°C, to avoid damaging the material.
- Process: The material is exposed to hot gases or air, which evaporate the moisture. This step is crucial for materials that are wet or have high moisture content, as it prevents issues like clumping or uneven heating in the subsequent zones.
-
Roasting Section (Optional):
- Function: In processes like nickel ore processing, a roasting section may be included. This section is designed to facilitate chemical reactions, such as oxidation or reduction, at specific temperatures.
- Temperature Range: The roasting section operates at high temperatures, often between 600°C to 900°C, depending on the desired chemical reaction.
- Process: The material is exposed to controlled atmospheres (e.g., oxidizing or reducing) to achieve the desired chemical transformation. This section is critical for processes where the chemical composition of the material needs to be altered.
-
Cooling Zone (Optional):
- Function: In some rotary kilns, a cooling zone may be included at the end of the process. This zone is designed to gradually reduce the temperature of the processed material before it is discharged.
- Temperature Range: The cooling zone operates at lower temperatures, gradually bringing the material down to a safe handling temperature.
- Process: The material is cooled using air or other cooling mediums, ensuring that it does not suffer from thermal shock or damage due to rapid cooling.
-
Customization Based on Material:
- Material-Specific Zones: The zones in a rotary kiln are often customized based on the material being processed. For example, in the case of nickel ore, the kiln may include a drying section, a heating section, and a roasting section, each tailored to the specific needs of the material.
- Temperature Control: Each zone can have multiple temperature settings, allowing for precise control over the heating process. This is particularly important for materials that require specific thermal treatments to achieve the desired properties.
In summary, the different zones in a rotary kiln are designed to provide controlled thermal treatment of materials, ensuring that each stage of the process is optimized for the specific material and desired outcome. The zones can be customized based on the material being processed, with temperature settings and durations adjusted to meet the process requirements. This flexibility makes rotary kilns highly versatile and effective for a wide range of industrial applications.
Summary Table:
Zone | Function | Temperature Range | Key Processes |
---|---|---|---|
Pre-Heating Zone | Gradually increases material temperature to reduce thermal shock. | Ambient to a few hundred °C | Moisture evaporation, uniform heating preparation. |
High-Temperature Zone | Core zone for intense thermal treatment (calcination, sintering, reactions). | Above 1000°C | Chemical changes, phase transitions, volatile component removal. |
Drying Section | Removes moisture before heating (optional). | Below 200°C | Moisture evaporation, prevents clumping or uneven heating. |
Roasting Section | Facilitates chemical reactions like oxidation or reduction (optional). | 600°C to 900°C | Chemical transformation under controlled atmospheres. |
Cooling Zone | Gradually reduces material temperature before discharge (optional). | Lower temperatures | Prevents thermal shock or damage during rapid cooling. |
Discover how a rotary kiln can enhance your material processing—contact our experts today!