Plastic pyrolysis, while a promising technology for waste management and resource recovery, faces several significant disadvantages. These include high energy consumption, substantial capital costs, technical challenges in process control and scalability, environmental and health risks from toxic by-products, and economic and logistical hurdles. The process demands sophisticated equipment, efficient separation of end products, and careful handling of variable feed materials. Additionally, the release of harmful pollutants and the accumulation of metals and ash in reactors further complicate its implementation. Despite its potential, these challenges make plastic pyrolysis less attractive for widespread adoption without further technological advancements.
Key Points Explained:
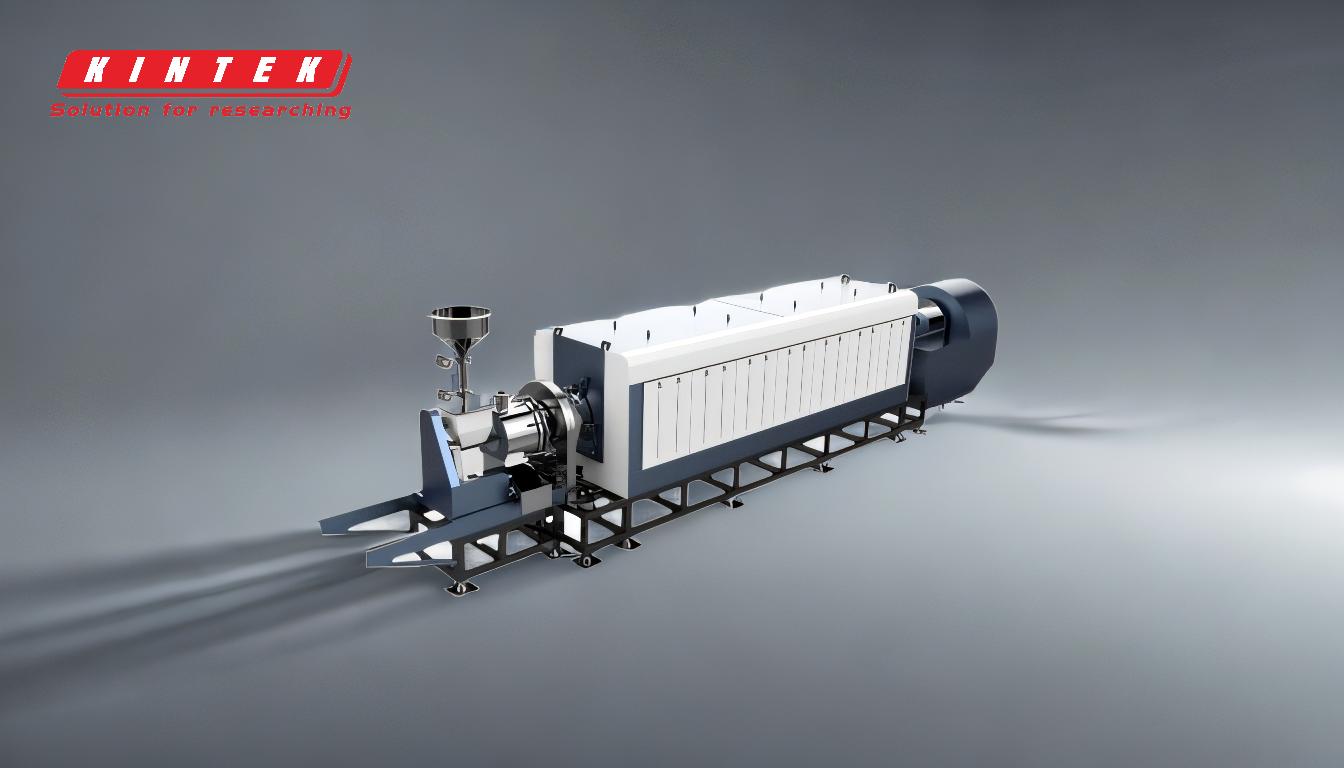
-
High Energy Consumption:
- Plastic pyrolysis is an energy-intensive process, requiring significant amounts of energy to maintain the high temperatures necessary for breaking down plastic waste.
- This high energy demand can lead to increased operational costs and may offset some of the environmental benefits of recycling plastic.
-
Substantial Capital Costs:
- The initial investment required for setting up pyrolysis plants is considerable. This includes the cost of purchasing and installing specialized reactors, monitoring systems, and separation equipment.
- These high capital costs can be a barrier to entry for many organizations, particularly in developing regions where funding may be limited.
-
Technical Challenges:
- Process Control: Maintaining the specific process conditions required for efficient pyrolysis is challenging. This includes controlling temperature, pressure, and reaction times to ensure optimal decomposition of plastics.
- Feedstock Variability: The process must handle a wide range of plastic types and contaminants, which can affect the consistency and quality of the end products.
- Reactor Design: Current reactor designs may not be efficient enough, leading to energy losses and reduced yields. Improvements in reactor technology are needed to enhance the overall efficiency of the process.
-
Environmental and Health Risks:
- Toxic By-products: The high-temperature pyrolysis process can produce harmful by-products, including toxic gases and residues. These by-products can pose significant health risks to workers and nearby communities.
- Pollutant Release: The process can release pollutants such as nitrous oxides and sulfur dioxides, which contribute to air pollution and have negative environmental impacts.
-
Economic and Logistical Hurdles:
- Separation and Purification: Efficiently separating and purifying the end products (such as bio-oil, gas, and char) is crucial but challenging. This step is necessary to ensure the quality and marketability of the recovered materials.
- Scalability: Scaling up pyrolysis technology to handle large volumes of plastic waste is difficult. The technology is still in its developmental stages, and there are limited examples of large-scale, successful implementations.
-
Global Adoption and Regulatory Concerns:
- Limited Adoption: Despite its potential, pyrolysis technology has not been widely adopted globally. This is due to a combination of technical, economic, and regulatory challenges.
- Regulatory Barriers: In some regions, stringent environmental regulations may limit the adoption of pyrolysis, particularly if the process is seen as contributing to pollution or health risks.
-
Impact on Other Waste Management Processes:
- Competition with Other Methods: The adoption of pyrolysis could potentially impact other waste-to-fuel processes, such as solid waste-to-fuel technologies. This could lead to economic disruptions in the waste management sector.
- Dependence on Imported Waste: Some countries rely on importing waste for their waste-to-energy processes. The adoption of pyrolysis could disrupt these existing supply chains and economic models.
In conclusion, while plastic pyrolysis offers a promising solution for managing plastic waste and recovering valuable resources, it is not without significant disadvantages. Addressing these challenges through technological innovation, regulatory support, and economic incentives will be crucial for realizing the full potential of this technology.
Summary Table:
Key Disadvantages | Details |
---|---|
High Energy Consumption | Requires significant energy to maintain high temperatures, increasing costs. |
Substantial Capital Costs | High initial investment for reactors, monitoring systems, and equipment. |
Technical Challenges | Difficulties in process control, feedstock variability, and reactor design. |
Environmental & Health Risks | Toxic by-products and pollutants pose risks to health and the environment. |
Economic & Logistical Hurdles | Challenges in product separation, scalability, and regulatory barriers. |
Want to learn more about overcoming the challenges of plastic pyrolysis? Contact our experts today for tailored solutions!