Metals are widely used in various industries due to their strength, durability, and conductivity. However, they also come with several disadvantages that can impact their suitability for certain applications. These drawbacks include susceptibility to corrosion, high density, thermal conductivity issues, and environmental concerns. Understanding these limitations is crucial for making informed decisions when selecting materials for specific uses.
Key Points Explained:
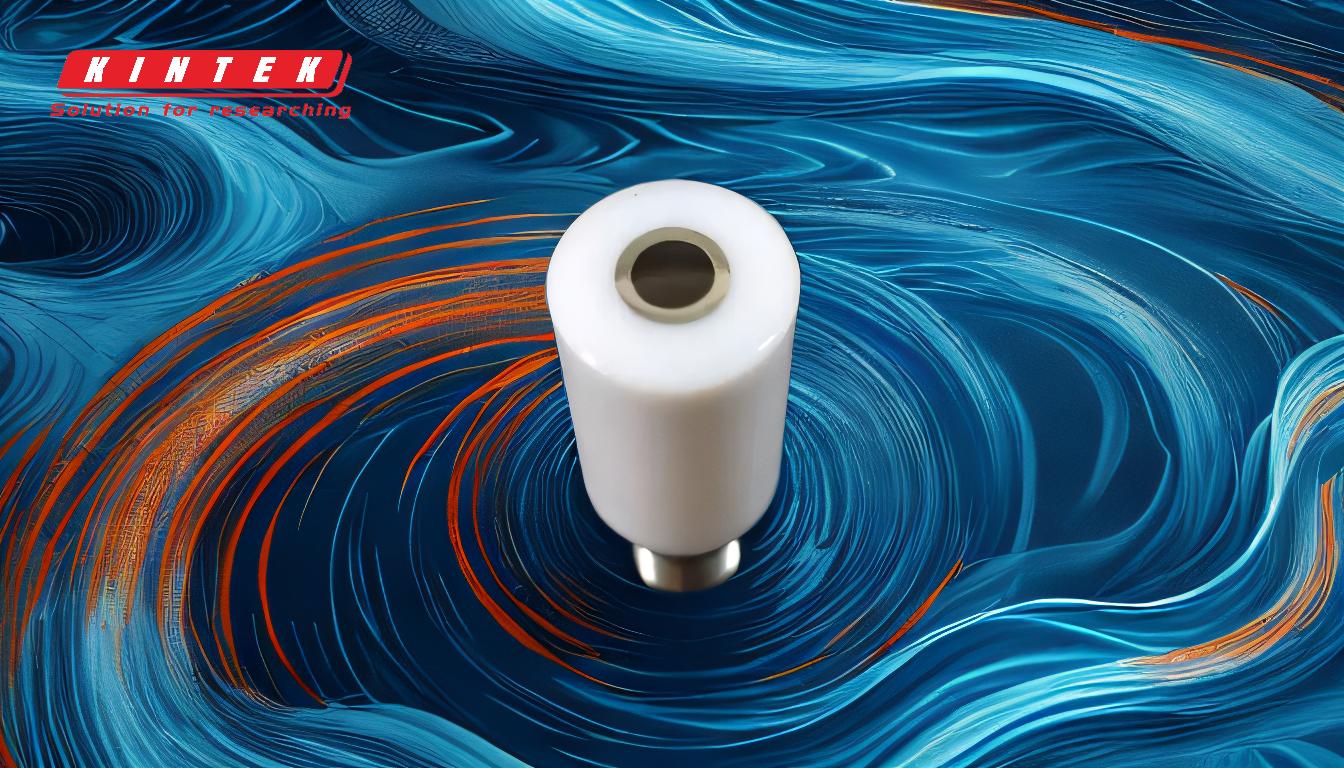
-
Susceptibility to Corrosion
- Metals, especially iron and steel, are prone to corrosion when exposed to moisture, oxygen, or chemicals. This can lead to structural weakening, reduced lifespan, and increased maintenance costs.
- Corrosion-resistant metals like stainless steel or aluminum are available but often come at a higher cost.
- For applications in harsh environments, such as marine or chemical industries, corrosion can be a significant drawback.
-
High Density
- Metals generally have high density, making them heavy compared to materials like plastics or composites.
- This can be a disadvantage in industries like aerospace or automotive, where weight reduction is critical for fuel efficiency and performance.
- Lightweight alternatives, such as titanium or aluminum, are sometimes used, but they may lack the same strength or durability as heavier metals.
-
Thermal Conductivity
- Metals are excellent conductors of heat, which can be a disadvantage in applications where thermal insulation is required.
- For example, in construction, metal components can contribute to heat loss, increasing energy consumption for heating or cooling.
- Insulating coatings or composite materials may be needed to mitigate this issue, adding to the cost and complexity of the design.
-
Environmental Concerns
- The extraction and processing of metals often involve significant energy consumption and environmental impact, including deforestation, water pollution, and greenhouse gas emissions.
- Recycling metals can mitigate some of these issues, but the process is not always efficient or cost-effective.
- The mining of rare metals, such as those used in electronics, can also lead to ethical concerns, including exploitation of labor and environmental degradation.
-
Cost
- Metals can be expensive, particularly when specialized alloys or treatments are required to enhance their properties.
- The cost of raw materials, processing, and transportation can make metal-based solutions less economical compared to alternatives like plastics or ceramics.
- In some cases, the long-term durability of metals may justify the initial investment, but this is not always feasible for budget-conscious projects.
-
Electrical Conductivity
- While electrical conductivity is an advantage in many applications, it can be a disadvantage in others. For example, metals can pose safety risks in electrical insulation or where static electricity is a concern.
- Non-conductive materials may be required in such cases, limiting the use of metals.
-
Difficulty in Machining and Fabrication
- Some metals, such as titanium or hardened steel, are difficult to machine or fabricate, requiring specialized equipment and expertise.
- This can increase production time and costs, making them less suitable for high-volume or low-budget projects.
-
Aesthetic Limitations
- Metals may not offer the same aesthetic versatility as materials like wood, glass, or composites.
- While finishes like painting or plating can enhance appearance, they may not be as durable or customizable as desired.
By considering these disadvantages, purchasers and designers can make more informed decisions about when and where to use metals, balancing their benefits against their limitations. Alternatives like composites, ceramics, or advanced polymers may offer better solutions in certain scenarios, depending on the specific requirements of the application.
Summary Table:
Disadvantage | Explanation |
---|---|
Susceptibility to Corrosion | Metals like iron and steel corrode in moist or chemical environments, leading to structural weakening and higher maintenance costs. |
High Density | Metals are heavy, making them less ideal for industries prioritizing weight reduction, such as aerospace. |
Thermal Conductivity | High heat conductivity can lead to energy inefficiency in applications requiring insulation. |
Environmental Concerns | Metal extraction and processing often cause deforestation, pollution, and high energy use. |
Cost | Metals can be expensive, especially when specialized alloys or treatments are needed. |
Electrical Conductivity | Conductivity can pose safety risks in applications requiring insulation or static control. |
Machining Difficulty | Some metals, like titanium, are hard to machine, increasing production time and costs. |
Aesthetic Limitations | Metals may lack the aesthetic versatility of materials like wood or composites. |
Need help deciding if metal is the right material for your project? Contact our experts today for personalized advice!