Rapid sintering techniques are advanced methods used to accelerate the sintering process, which is crucial for manufacturing components with high precision, complex geometries, and improved material properties. These techniques leverage innovative heating and pressure application methods to reduce processing time while maintaining or enhancing material quality. Examples include Spark Plasma Sintering (SPS), Microwave Sintering, and Direct Metal Laser Sintering (DMLS). These methods are particularly beneficial in industries requiring high-performance materials, such as aerospace, automotive, and medical devices, as they enable faster production cycles and better control over material properties.
Key Points Explained:
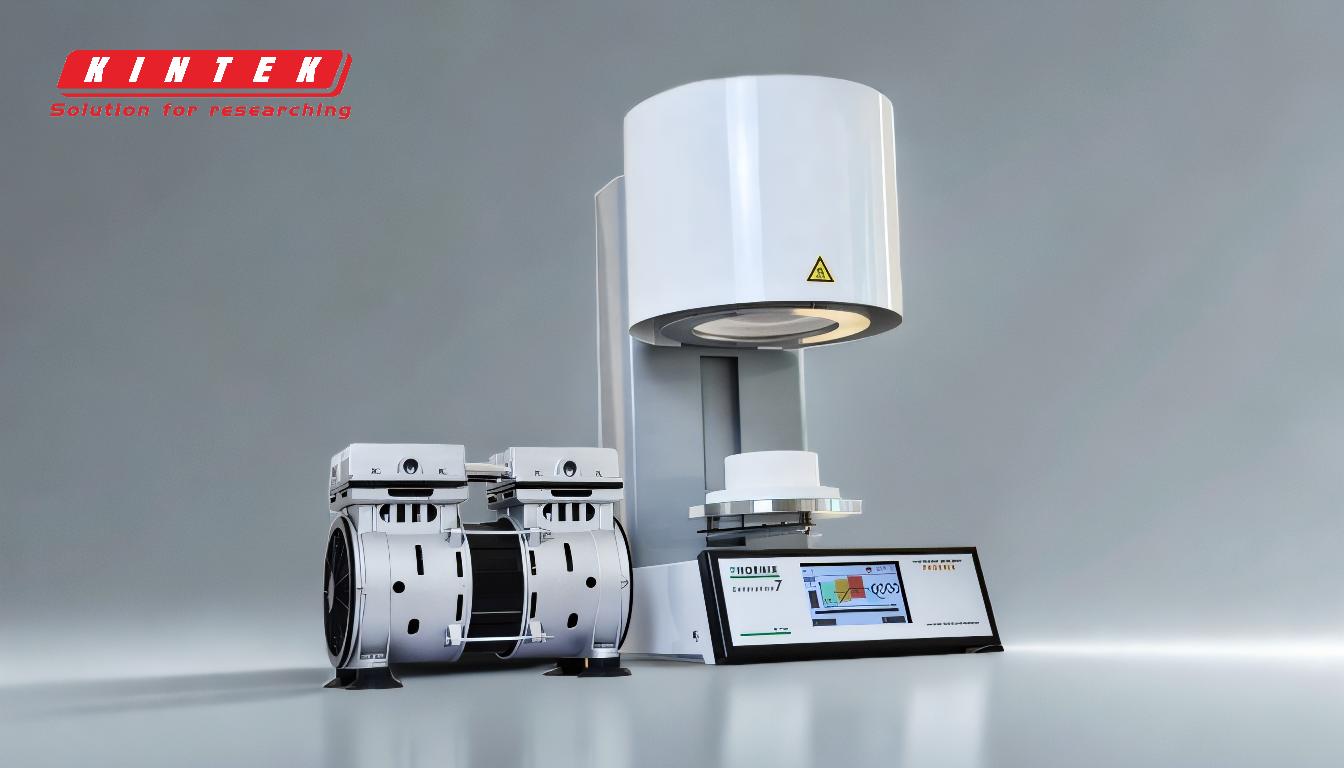
-
Definition of Rapid Sintering Techniques:
- Rapid sintering techniques are advanced processes designed to speed up the sintering of powdered materials, reducing the time required to achieve densification and bonding.
- These methods often combine heat, pressure, and sometimes electric or electromagnetic energy to accelerate atomic diffusion and material consolidation.
-
Types of Rapid Sintering Techniques:
-
Spark Plasma Sintering (SPS):
- Uses a pulsed electric current to generate heat and pressure simultaneously, enabling rapid densification of materials.
- Ideal for producing high-density components with fine microstructures, such as ceramics, metals, and composites.
-
Microwave Sintering:
- Utilizes microwave energy to heat materials uniformly and rapidly, reducing processing time significantly.
- Commonly used for ceramics and some metals, offering energy efficiency and improved material properties.
-
Direct Metal Laser Sintering (DMLS):
- A 3D printing technique that uses a high-powered laser to fuse metal powder layer by layer, creating complex geometries with high precision.
- Widely used in aerospace and medical industries for prototyping and production of intricate parts.
-
Spark Plasma Sintering (SPS):
-
Advantages of Rapid Sintering Techniques:
-
Reduced Processing Time:
- Rapid sintering methods significantly shorten the time required for densification compared to conventional sintering.
-
Improved Material Properties:
- Enhanced mechanical, thermal, and electrical properties due to finer microstructures and reduced porosity.
-
Energy Efficiency:
- Techniques like microwave sintering and SPS consume less energy by targeting heat directly to the material.
-
Complex Geometries:
- Methods like DMLS enable the production of intricate designs that are difficult or impossible to achieve with traditional methods.
-
Reduced Processing Time:
-
Applications of Rapid Sintering:
-
Aerospace:
- Production of lightweight, high-strength components such as turbine blades and structural parts.
-
Medical Devices:
- Manufacturing of biocompatible implants and prosthetics with precise geometries.
-
Automotive:
- Creation of durable and lightweight parts for engines and chassis.
-
Electronics:
- Fabrication of components with tailored electrical and thermal properties.
-
Aerospace:
-
Comparison with Conventional Sintering:
-
Time Efficiency:
- Rapid sintering techniques can reduce processing times from hours to minutes.
-
Material Quality:
- Enhanced control over microstructure and density, leading to superior mechanical properties.
-
Cost-Effectiveness:
- While initial equipment costs may be higher, the reduction in processing time and energy consumption can lower overall production costs.
-
Time Efficiency:
-
Challenges and Considerations:
-
Equipment Costs:
- Rapid sintering technologies often require specialized and expensive equipment.
-
Material Compatibility:
- Not all materials are suitable for rapid sintering, and some may require specific modifications.
-
Process Control:
- Achieving consistent results requires precise control over parameters such as temperature, pressure, and energy input.
-
Equipment Costs:
By leveraging rapid sintering techniques, manufacturers can achieve faster production cycles, improved material performance, and the ability to create complex designs, making these methods invaluable in modern industrial applications.
Summary Table:
Aspect | Details |
---|---|
Definition | Advanced processes to speed up sintering, combining heat, pressure, and energy for faster densification. |
Types | Spark Plasma Sintering (SPS), Microwave Sintering, Direct Metal Laser Sintering (DMLS). |
Advantages | Reduced processing time, improved material properties, energy efficiency, complex geometries. |
Applications | Aerospace, medical devices, automotive, electronics. |
Comparison | Faster than conventional sintering, better material quality, cost-effective in the long run. |
Challenges | High equipment costs, material compatibility, precise process control required. |
Ready to enhance your manufacturing process? Contact us today to learn more about rapid sintering solutions!