Physical Vapor Deposition (PVD) is a versatile technology used across various industries to create thin, durable coatings on a wide range of materials. These coatings enhance the performance, durability, and functionality of products in industries such as aerospace, automotive, electronics, and more. PVD is particularly valued for its ability to produce high-quality, corrosion-resistant, and wear-resistant coatings, making it indispensable in modern manufacturing and engineering applications.
Key Points Explained:
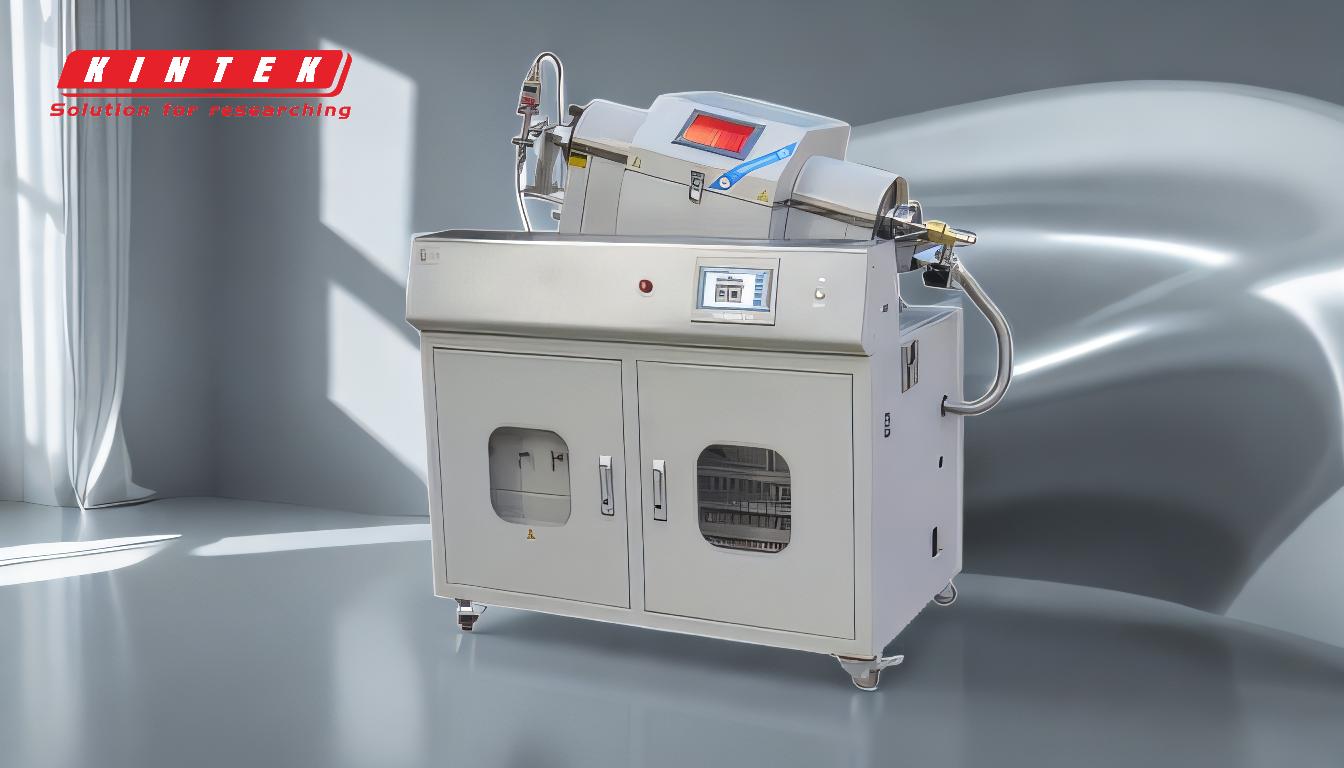
-
Aerospace Industry:
- PVD coatings are extensively used in the aerospace industry to enhance the durability and performance of components. These coatings provide resistance to corrosion, wear, and high temperatures, which are critical for aircraft and spacecraft parts. For example, turbine blades and engine components are often coated with PVD to withstand extreme operational conditions.
-
Automotive Industry:
- In the automotive sector, PVD is used to coat various components such as engine parts, decorative trims, and functional surfaces. The coatings improve wear resistance, reduce friction, and enhance the aesthetic appeal of automotive parts. PVD is also used in the production of cutting tools and molds, which are essential for manufacturing high-precision automotive components.
-
Electronics and Semiconductors:
- PVD plays a crucial role in the electronics industry, particularly in the deposition of thin films on semiconductors. These thin films are essential for the fabrication of integrated circuits, sensors, and other electronic devices. PVD is also used in the production of thin-film solar cells, where it helps deposit photovoltaic materials onto substrates, enhancing the efficiency of solar energy conversion.
-
Optics and Jewelry:
- PVD coatings are widely used in the optics industry to create anti-reflective, scratch-resistant, and durable coatings on lenses and mirrors. In the jewelry industry, PVD is used to apply decorative and protective coatings on watches, rings, and other accessories, enhancing their appearance and longevity.
-
Architectural Applications:
- PVD is employed in architectural ironmongery, panels, and sheets to provide durable, corrosion-resistant, and aesthetically pleasing finishes. These coatings are used on building facades, window frames, and other structural elements, ensuring long-term performance and visual appeal.
-
Firearms and Defense:
- In the firearms and defense industry, PVD coatings are used to enhance the durability and performance of weapons and equipment. The coatings provide resistance to wear, corrosion, and environmental factors, ensuring reliability and longevity in demanding conditions.
-
Food Packaging and Window Tint:
- PVD is also used in the production of thin-film applications such as window tint and food packaging. These coatings improve the barrier properties of packaging materials, extending the shelf life of food products. In window tinting, PVD coatings provide UV protection, energy efficiency, and aesthetic enhancement.
-
Cutting Tools and Molds:
- PVD coatings are applied to cutting tools and molds to improve their hardness, wear resistance, and overall performance. This is particularly important in industries that require high-precision machining and long-lasting tooling solutions.
-
Microwave Plasma Chemical Vapor Deposition:
- While PVD is distinct from microwave plasma chemical vapor deposition, both technologies are used in advanced material processing. PVD focuses on physical processes like sputtering and evaporation, whereas microwave plasma CVD involves chemical reactions to deposit thin films. Both methods are complementary in applications requiring high-performance coatings and thin films.
-
Advantages of PVD:
- PVD offers several advantages, including the ability to coat a wide range of materials (ceramics, metals, glass), the production of durable and high-purity coatings, and the capability to coat complex and precision surfaces. These benefits make PVD a preferred choice in industries requiring high-performance materials and coatings.
In summary, PVD is a critical technology in modern manufacturing, offering solutions for enhancing the performance, durability, and functionality of products across a wide range of industries. Its applications are diverse, from aerospace and automotive to electronics and jewelry, making it an indispensable tool in the development of advanced materials and coatings.
Summary Table:
Industry | Applications |
---|---|
Aerospace | Turbine blades, engine components (corrosion, wear, and high-temperature resistance) |
Automotive | Engine parts, decorative trims, cutting tools, molds (wear resistance, aesthetics) |
Electronics & Semiconductors | Thin films for ICs, sensors, solar cells (efficiency enhancement) |
Optics & Jewelry | Anti-reflective lenses, scratch-resistant coatings, decorative jewelry finishes |
Architecture | Building facades, window frames (durable, corrosion-resistant finishes) |
Firearms & Defense | Weapons, equipment (wear, corrosion, and environmental resistance) |
Food Packaging & Window Tint | Barrier coatings for packaging, UV protection for window tinting |
Cutting Tools & Molds | High-precision machining tools (hardness, wear resistance) |
Interested in how PVD can benefit your industry? Contact us today to learn more!