Metal fabrication is a critical process in various industries, offering both significant advantages and notable disadvantages. On the positive side, it enables the creation of durable, high-strength components that are essential for construction, automotive, and aerospace applications. Techniques like welding, cutting, and machining allow for precise customization, meeting specific design requirements. However, the process also has drawbacks, including high energy consumption, material waste, and the need for skilled labor. Additionally, certain fabrication methods can introduce structural weaknesses or require costly equipment. Understanding these pros and cons is essential for making informed decisions in manufacturing and design.
Key Points Explained:
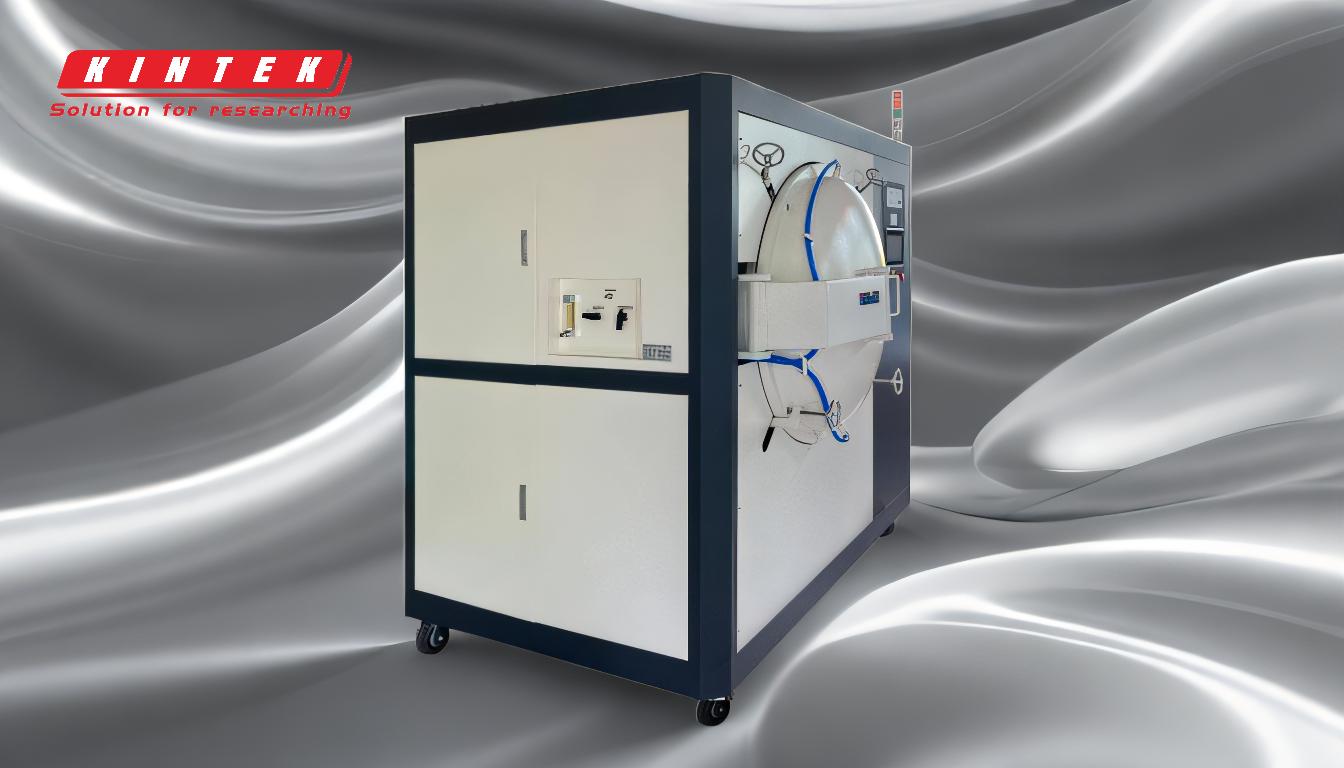
-
Advantages of Metal Fabrication
- Durability and Strength: Metal-fabricated products are known for their durability and ability to withstand harsh conditions, making them ideal for heavy-duty applications.
- Customization: Techniques such as welding, bending, and machining allow for precise customization, ensuring that components meet exact specifications.
- Versatility: Metal fabrication can be applied to a wide range of metals, including steel, aluminum, and titanium, catering to diverse industry needs.
- Scalability: The process supports both small-scale and large-scale production, making it adaptable to various project sizes.
-
Disadvantages of Metal Fabrication
- High Energy Consumption: Many fabrication processes, such as welding and forging, require significant energy, leading to higher operational costs and environmental impact.
- Material Waste: Cutting and machining often result in material waste, which can increase costs and require additional recycling efforts.
- Skilled Labor Requirement: Metal fabrication demands skilled workers for precise operations, which can be a challenge in regions with a shortage of trained professionals.
- Equipment Costs: Advanced machinery and tools are often necessary, leading to high initial investment and maintenance expenses.
- Potential Weaknesses: Certain fabrication methods, like welding, can introduce stress points or weaknesses in the metal structure if not performed correctly.
-
Balancing Pros and Cons
- To maximize the benefits of metal fabrication, it's crucial to select the appropriate techniques and materials for each project. For example, using lightweight metals like aluminum can reduce energy consumption while maintaining strength.
- Implementing lean manufacturing principles can help minimize waste and improve efficiency.
- Investing in training programs for workers can address the skilled labor shortage and enhance the quality of fabricated products.
By carefully weighing these advantages and disadvantages, manufacturers can optimize their processes and achieve better outcomes in metal fabrication projects.
Summary Table:
Aspect | Advantages | Disadvantages |
---|---|---|
Durability & Strength | High-strength components ideal for heavy-duty applications. | Certain methods may introduce structural weaknesses. |
Customization | Precise techniques like welding and machining meet exact specifications. | Requires skilled labor, which can be costly or hard to find. |
Versatility | Works with various metals (steel, aluminum, titanium) for diverse needs. | High energy consumption in processes like welding and forging. |
Scalability | Supports both small- and large-scale production. | Material waste from cutting and machining increases costs. |
Equipment | Advanced tools enable high-quality fabrication. | High initial investment and maintenance costs for machinery. |
Need help optimizing your metal fabrication process? Contact our experts today for tailored solutions!