A muffle furnace is a versatile and essential piece of equipment in various industries, offering high-temperature processing capabilities with excellent temperature uniformity and protection from aggressive atmospheres. Its advantages include durability, rapid heating, and the ability to handle a wide range of materials, making it suitable for applications like ashing, elemental analysis, and thermal processing. However, it also has some disadvantages, such as longer warm-up times compared to open-flame methods and limited accessibility to the interior, which requires careful material placement. Despite these drawbacks, its practicality, low maintenance costs, and resistance to harsh conditions make it a valuable tool in laboratories, industrial settings, and research units.
Key Points Explained:
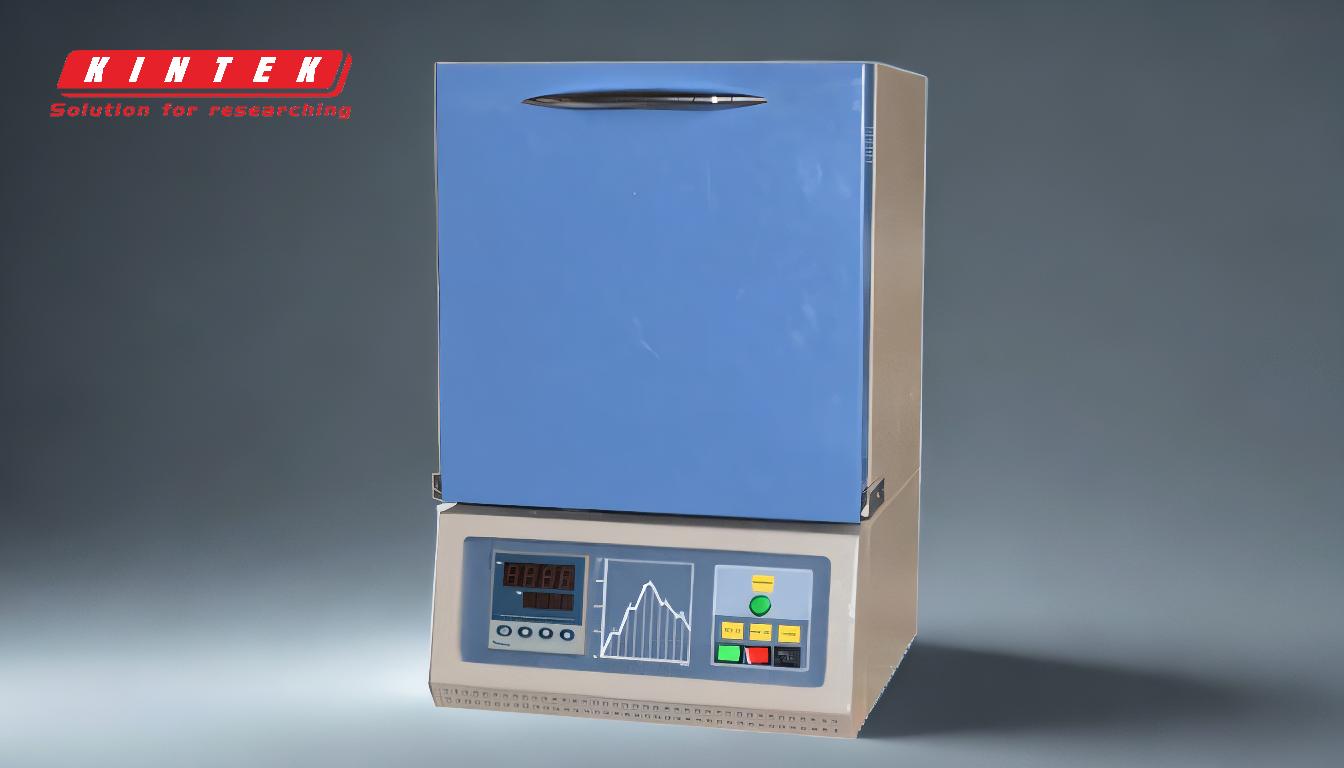
-
Advantages of a Muffle Furnace:
- High-Temperature Processing: Capable of reaching very high temperatures quickly, making it suitable for applications like sintering, dissolution, and analysis of metals and ceramics.
- Temperature Uniformity: Ensures consistent heating, which is critical for processes like ashing and elemental analysis.
- Durability and Resistance: Made with high-quality materials like ceramic muffles and stainless steel, offering resistance to oxidation, acids, alkalis, and corrosion.
- Versatility: Used across various industries, including pharmaceuticals, analytical chemistry, and coal analysis, for tasks like drug testing, water quality analysis, and ash composition analysis.
- Low Maintenance Costs: Designed for long service life with minimal operational and maintenance expenses.
- Safety Features: Includes humanized designs like optional flap doors and adjustable air inlets to protect operators from hot surfaces and aggressive gases.
-
Disadvantages of a Muffle Furnace:
- Longer Warm-Up Times: Takes more time to reach desired temperatures compared to open-flame methods, which may not be ideal for time-sensitive projects.
- Limited Accessibility: The enclosed design makes it harder to access the interior, requiring careful placement of materials to ensure even heating.
- Heat Loss Prevention: While insulated materials prevent heat loss, they can also slow down cooling processes, which might be a drawback for certain applications.
-
Applications of a Muffle Furnace:
- Laboratory Use: Ideal for moisture, ash, volatile matter, and elemental analysis, as well as melting point and ash composition analysis.
- Industrial Use: Used for quenching, annealing, tempering, and sintering of small steel parts, metals, and ceramics.
- Pharmaceutical and Analytical Chemistry: Essential for drug testing, medical sample pretreatment, water quality analysis, and environmental analysis.
- General Ashing: Commonly used as a general-purpose ashing furnace in various industries.
-
Design Features:
- Ceramic Muffle: Provides high resistance to aggressive gases and vapors, ensuring a clean and particle-free environment for sensitive processes.
- Stainless Steel Housing: Enhances durability and corrosion resistance.
- Solid-State Relays: Enable low-noise operation, making it suitable for quiet laboratory environments.
- Step-Type Assembling Structure: Ensures the hearth remains stable and prevents heat dissipation.
In summary, a muffle furnace is a highly efficient and durable tool for high-temperature applications, offering excellent temperature control and resistance to harsh conditions. While it has some limitations, such as longer warm-up times and limited interior access, its advantages far outweigh these drawbacks, making it indispensable in various scientific and industrial settings.
Summary Table:
Aspect | Advantages | Disadvantages |
---|---|---|
Temperature Control | High-temperature processing with excellent uniformity. | Longer warm-up times compared to open-flame methods. |
Durability | Resistant to oxidation, acids, alkalis, and corrosion. | Limited interior accessibility requires careful material placement. |
Versatility | Suitable for ashing, elemental analysis, and thermal processing. | Insulated materials may slow down cooling processes. |
Maintenance | Low maintenance costs with a long service life. | |
Safety | Includes safety features like flap doors and adjustable air inlets. |
Ready to enhance your lab or industrial processes with a muffle furnace? Contact us today to find the perfect solution for your needs!