Metal-Organic Chemical Vapor Deposition (MOCVD) is a widely used technique in the semiconductor industry for growing high-quality epitaxial layers. It offers several advantages, such as precise control over material properties, high purity, and suitability for large-scale production. However, it also has notable disadvantages, including high costs, safety concerns related to toxic and flammable precursors, and environmental challenges. Understanding these pros and cons is essential for making informed decisions about its use in various applications.
Key Points Explained:
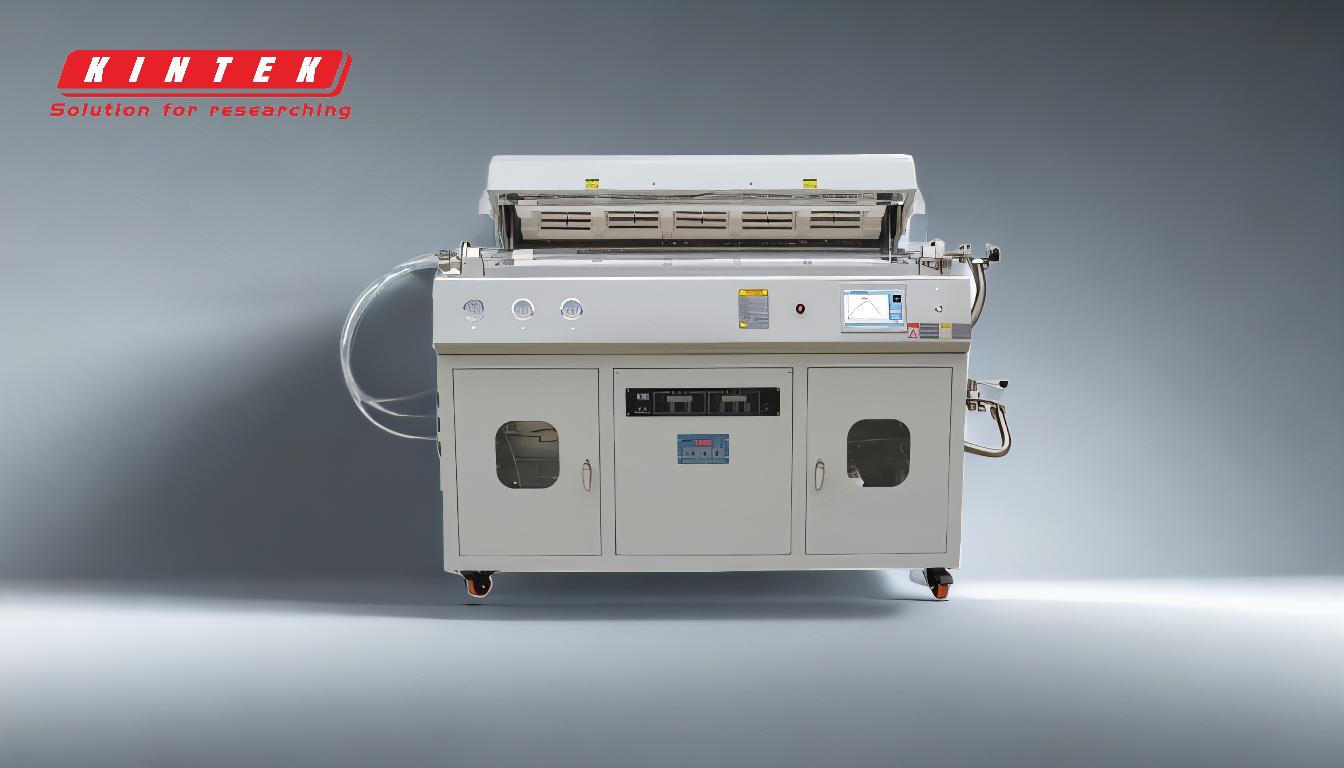
-
Advantages of MOCVD:
- Wide Range of Applications: MOCVD is versatile and can be used to grow a variety of heterostructured materials, making it suitable for applications in optoelectronics, photovoltaics, and semiconductor devices.
- Precision and Control: It allows for precise control over the components, dopant concentration, and thickness of the epitaxial layer, ensuring high-quality material growth.
- High Purity and Uniformity: MOCVD can produce ultra-thin epitaxial layers with steep interfacial transitions and excellent uniformity over large areas, which is critical for device performance.
- Scalability: The technology is well-suited for large-scale production, making it a preferred choice for industrial applications.
- In-situ Monitoring: The ability to monitor the growth process in real-time enhances process control and reproducibility.
-
Disadvantages of MOCVD:
-
High Costs:
- Precursor Costs: Metal-organic compounds and hydride sources used in MOCVD are expensive, increasing the overall cost of the process.
- Equipment Costs: The initial purchase, installation, and maintenance of MOCVD equipment are costly, making it less accessible for small-scale productions or laboratories.
-
Safety and Environmental Concerns:
- Toxic and Hazardous Precursors: Some precursors used in MOCVD are flammable, explosive, or toxic, requiring stringent safety measures and specialized handling.
- Waste Management: Reaction byproducts must be treated to avoid environmental pollution, adding to operational complexity and cost.
- Process Complexity: MOCVD requires careful control to prevent unintentional impurities, such as carbon and hydrogen, from being incorporated into the epitaxial layers, which can degrade material quality.
- Limited Suitability for High-Power Devices: MOCVD is not ideal for manufacturing high-performance, power-hungry devices, limiting its application in certain fields.
-
High Costs:
-
Comparison with CVD:
- While MOCVD offers superior control and material quality, it is more expensive and complex compared to traditional Chemical Vapor Deposition (CVD). CVD is simpler and more cost-effective but lacks the precision and scalability of MOCVD.
In summary, MOCVD is a powerful technology with significant advantages in material growth and scalability, but its high costs, safety concerns, and environmental challenges must be carefully considered. For large-scale, high-precision applications, MOCVD is often the best choice, but for smaller operations or less demanding requirements, alternative methods like CVD may be more practical.
Summary Table:
Aspect | Advantages | Disadvantages |
---|---|---|
Applications | Versatile for optoelectronics, photovoltaics, and semiconductor devices. | Limited suitability for high-power devices. |
Precision & Control | Precise control over material properties, dopant concentration, and thickness. | Process complexity to avoid impurities like carbon and hydrogen. |
Purity & Uniformity | Produces ultra-thin, high-purity, and uniform epitaxial layers. | High precursor and equipment costs. |
Scalability | Ideal for large-scale production. | Expensive initial setup and maintenance. |
Safety & Environment | In-situ monitoring enhances reproducibility. | Toxic, flammable precursors and environmental waste management challenges. |
Ready to optimize your semiconductor processes? Contact us today to learn more about MOCVD solutions!