Selective Laser Sintering (SLS) is a powerful additive manufacturing technology that offers unique advantages and disadvantages. It excels in creating complex, functional shapes that are difficult to achieve with traditional sintering methods. However, it comes with high costs, including expensive machines and materials, and requires skilled operators. In contrast, powder metallurgy is more cost-effective for large-scale production of medium-complexity shapes but may result in non-uniform components due to friction between powder and tooling. Below, the key advantages and disadvantages of SLS are explored in detail.
Key Points Explained:
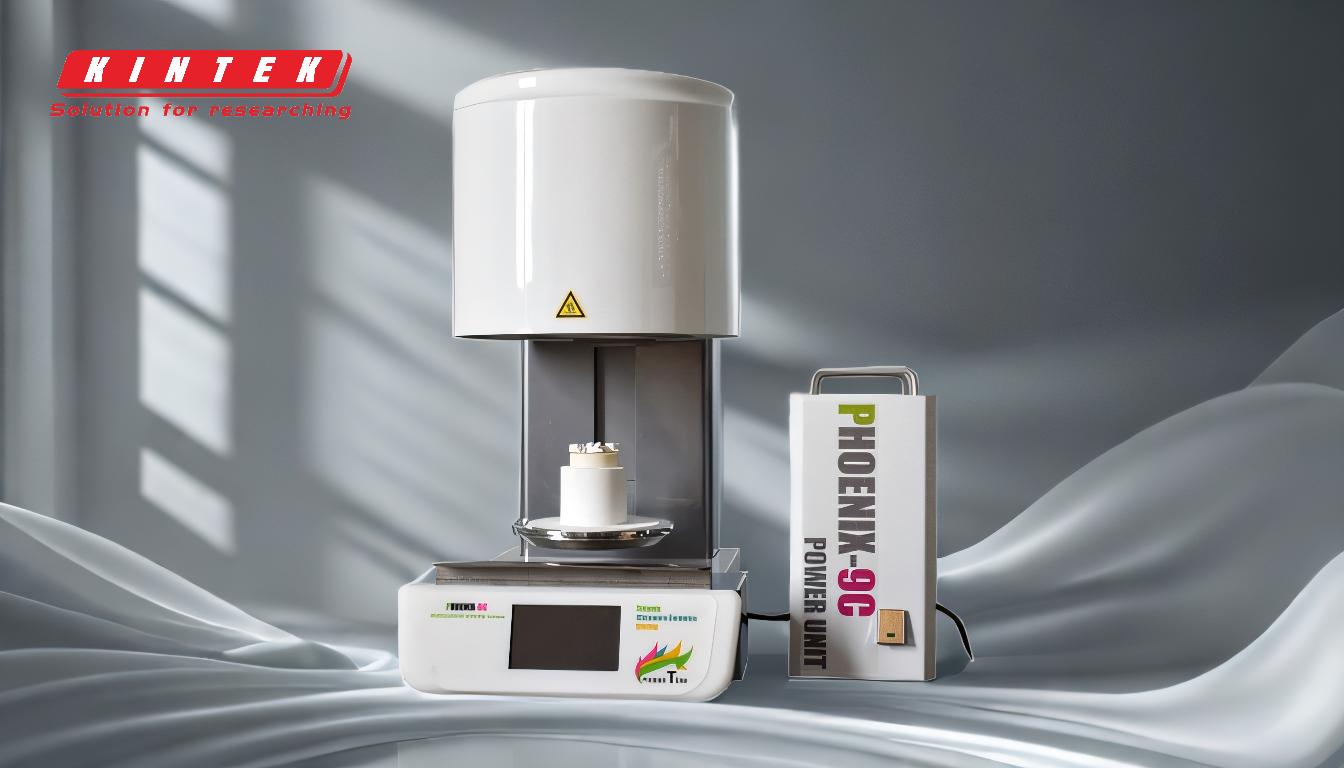
-
Advantages of Selective Laser Sintering (SLS):
-
Complex and Functional Shapes:
- SLS allows for the creation of highly complex and functional geometries that are difficult or impossible to achieve with traditional sintering or machining methods. This is particularly useful for industries requiring intricate designs, such as aerospace, medical, and automotive.
-
Material Versatility:
- SLS can work with a wide range of materials, including polymers, metals, and ceramics, enabling the production of parts with diverse mechanical and thermal properties.
-
No Support Structures Required:
- Unlike some other additive manufacturing techniques, SLS does not require support structures during the build process, as the unsintered powder acts as a natural support. This reduces post-processing time and material waste.
-
High Precision and Repeatability:
- SLS offers high precision and repeatability, making it suitable for producing parts with tight tolerances and consistent quality.
-
Complex and Functional Shapes:
-
Disadvantages of Selective Laser Sintering (SLS):
-
High Initial and Operational Costs:
- SLS machines are expensive, often costing over $250,000, which makes them inaccessible for small businesses or startups. Additionally, the materials used in SLS are costly, further increasing the overall expense.
-
Skilled Operator Requirement:
- Operating an SLS machine requires specialized knowledge and training, which can be a barrier for companies without access to skilled personnel.
-
Post-Processing Requirements:
- Parts produced by SLS often require post-processing, such as cleaning, heat treatment, or surface finishing, to achieve the desired properties and appearance.
-
Limited Build Size:
- The build chamber of SLS machines has size limitations, restricting the maximum dimensions of parts that can be produced in a single print.
-
High Initial and Operational Costs:
-
Comparison with Powder Metallurgy:
-
Cost-Effectiveness for Large-Scale Production:
- Powder metallurgy is more cost-effective for large-scale production of medium-complexity shapes, as it involves lower machine and material costs compared to SLS.
-
No Skilled Operator Requirement:
- Powder metallurgy processes are generally easier to operate and do not require highly skilled operators, reducing labor costs.
-
Non-Uniformity Issues:
- A potential drawback of powder metallurgy is the risk of non-uniform components due to friction between the powder and tooling, which can affect the mechanical properties of the final product.
-
Cost-Effectiveness for Large-Scale Production:
-
Applications and Suitability:
-
SLS for Prototyping and Low-Volume Production:
- SLS is ideal for prototyping and low-volume production of complex parts, where design flexibility and material properties are critical.
-
Powder Metallurgy for Mass Production:
- Powder metallurgy is better suited for mass production of simpler shapes, where cost efficiency and production speed are prioritized over design complexity.
-
SLS for Prototyping and Low-Volume Production:
In summary, SLS offers significant advantages in terms of design flexibility and material versatility but comes with high costs and operational challenges. Powder metallurgy, on the other hand, is more economical for large-scale production but may sacrifice some design complexity and uniformity. The choice between these technologies depends on the specific requirements of the project, including budget, production volume, and part complexity.
Summary Table:
Aspect | Selective Laser Sintering (SLS) | Powder Metallurgy |
---|---|---|
Design Complexity | High - Ideal for complex, functional shapes | Medium - Suitable for simpler shapes |
Material Versatility | High - Works with polymers, metals, ceramics | Limited - Primarily metals |
Cost | High - Expensive machines and materials | Low - Cost-effective for large-scale production |
Operator Skill Requirement | High - Requires specialized training | Low - Easier to operate |
Post-Processing | Required - Cleaning, heat treatment, surface finishing | Minimal - Less post-processing needed |
Build Size | Limited - Restricted by machine chamber size | Flexible - Larger parts achievable |
Uniformity | High - Consistent quality | Low - Risk of non-uniform components |
Applications | Prototyping, low-volume production of complex parts | Mass production of simpler shapes |
Need help deciding between SLS and powder metallurgy? Contact our experts today for tailored advice!