Selective Laser Sintering (SLS) is a 3D printing technology that offers unique advantages, such as the ability to produce highly complex and functional parts with minimal post-processing. However, it also comes with significant drawbacks, including high costs for equipment and materials, as well as the need for skilled operators. This technology is particularly suited for applications requiring intricate designs but may not be cost-effective for large-scale production. Powder metallurgy, by contrast, is more economical for medium-complexity shapes and large-scale manufacturing, though it may result in less uniform components due to friction during processing.
Key Points Explained:
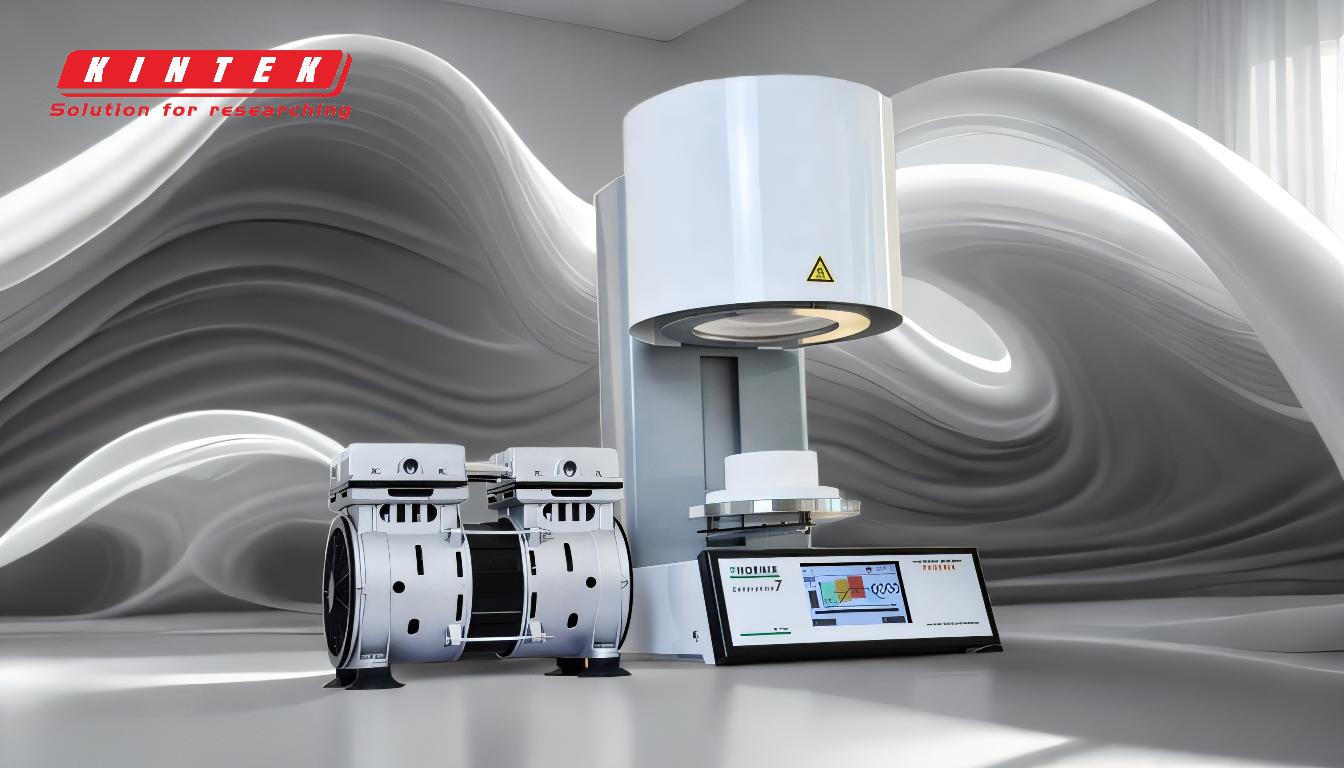
-
Advantages of SLS:
- Complex and Functional Shapes: SLS excels at creating intricate geometries that are difficult or impossible to achieve with traditional sintering or powder metallurgy. This makes it ideal for prototyping and manufacturing parts with complex internal structures or fine details.
- Minimal Post-Processing: Parts produced by SLS often require little to no additional finishing, as the process inherently produces smooth surfaces and functional components.
- Material Versatility: SLS can work with a wide range of materials, including polymers, metals, and ceramics, providing flexibility in material selection for specific applications.
-
Disadvantages of SLS:
- High Costs: The initial investment for SLS machines is substantial, often exceeding $250,000. Additionally, the materials used in SLS are expensive, further increasing the overall cost of production.
- Skilled Operator Requirement: Operating SLS machines requires specialized knowledge and training, adding to labor costs and limiting accessibility for smaller businesses.
- Limited Scalability: While SLS is excellent for small-batch production and prototyping, it is not cost-effective for large-scale manufacturing due to its slower production speeds and higher per-unit costs.
-
Comparison with Powder Metallurgy:
- Cost-Effectiveness: Powder metallurgy is generally more affordable than SLS, making it a better choice for large-scale production of medium-complexity parts.
- Ease of Operation: Unlike SLS, powder metallurgy does not require highly skilled operators, reducing labor costs and simplifying the production process.
- Uniformity Issues: However, powder metallurgy can result in non-uniform components due to friction between the powder and tooling during the pressing stage, which may affect the mechanical properties of the final product.
-
Applications and Suitability:
- SLS: Best suited for applications requiring high complexity, such as aerospace components, medical devices, and custom tooling. Its ability to produce functional prototypes quickly makes it valuable in industries where design iteration is critical.
- Powder Metallurgy: More appropriate for high-volume production of parts with moderate complexity, such as automotive components, gears, and bearings. Its cost efficiency and scalability make it a popular choice for mass production.
-
Future Considerations:
- Technological Advancements: As SLS technology evolves, costs may decrease, and the process could become more accessible to a broader range of industries. Improvements in material science may also expand the range of applications for SLS.
- Hybrid Approaches: Combining SLS with other manufacturing techniques, such as powder metallurgy, could offer a balance between complexity, cost, and scalability, potentially opening new opportunities in advanced manufacturing.
In summary, SLS offers unparalleled capabilities for creating complex and functional parts but comes with significant cost and operational challenges. Powder metallurgy, while less versatile in terms of design complexity, provides a more economical solution for large-scale production. The choice between these technologies depends on the specific requirements of the application, including complexity, volume, and budget constraints.
Summary Table:
Aspect | Selective Laser Sintering (SLS) | Powder Metallurgy |
---|---|---|
Complexity | Excels at intricate geometries and complex shapes. | Limited to medium-complexity shapes. |
Cost | High equipment and material costs; not cost-effective for large-scale production. | More economical for large-scale manufacturing. |
Post-Processing | Minimal post-processing required. | May require additional finishing due to uniformity issues. |
Operator Skill | Requires skilled operators. | Easier to operate, reducing labor costs. |
Scalability | Best for small-batch production and prototyping. | Ideal for high-volume production. |
Applications | Aerospace, medical devices, and custom tooling. | Automotive components, gears, and bearings. |
Discover how SLS or powder metallurgy can transform your manufacturing process—contact us today for expert guidance!