A three-plate mold and a two-plate mold are both used in injection molding, but they serve different purposes and have distinct advantages depending on the application. A two-plate mold is simpler, more cost-effective, and has a shorter lead time and cycle time, making it ideal for straightforward parts. In contrast, a three-plate mold, while more complex and costly, offers greater flexibility in part design, especially for parts requiring multiple gates or automatic separation of runners and parts. The choice between the two depends on the specific requirements of the part being produced.
Key Points Explained:
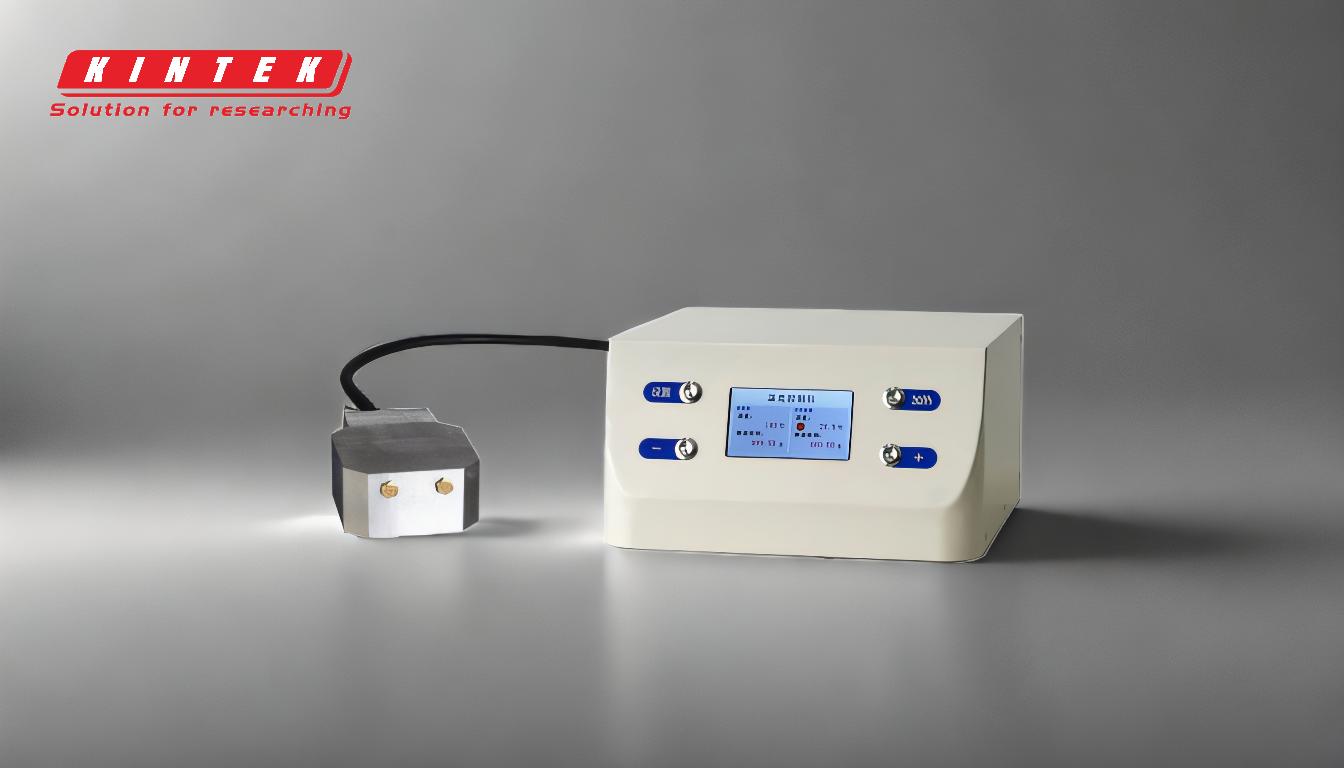
-
Design Complexity and Cost:
-
Two-Plate Mold:
- Simpler design, making it easier and faster to manufacture.
- Lower cost due to fewer components and less complexity.
-
Three-Plate Mold:
- More complex design, requiring additional plates and mechanisms.
- Higher cost due to increased complexity and more components.
-
Two-Plate Mold:
-
Lead Time:
-
Two-Plate Mold:
- Shorter lead time because of its simpler design and fewer components.
-
Three-Plate Mold:
- Longer lead time due to the complexity of the design and the need for more precise manufacturing.
-
Two-Plate Mold:
-
Cycle Time:
-
Two-Plate Mold:
- Lower cycle time, as the mold opens and closes more quickly.
-
Three-Plate Mold:
- Higher cycle time, due to the additional movements required to separate the runner system from the part.
-
Two-Plate Mold:
-
Flexibility in Part Design:
-
Two-Plate Mold:
- Limited flexibility, typically used for simpler parts with fewer gates.
-
Three-Plate Mold:
- Greater flexibility, allowing for more complex parts with multiple gates and automatic separation of runners and parts.
-
Two-Plate Mold:
-
Runner System:
-
Two-Plate Mold:
- The runner system is part of the mold cavity, and the part and runner are ejected together.
-
Three-Plate Mold:
- The runner system is separate from the part, allowing for automatic separation and more efficient material use.
-
Two-Plate Mold:
-
Ejection Mechanism:
-
Two-Plate Mold:
- Simpler ejection mechanism, as the part and runner are ejected together.
-
Three-Plate Mold:
- More complex ejection mechanism, requiring additional plates and mechanisms to separate the runner from the part.
-
Two-Plate Mold:
-
Material Efficiency:
-
Two-Plate Mold:
- Less efficient in terms of material use, as the runner system is part of the mold cavity and may require more material.
-
Three-Plate Mold:
- More efficient in terms of material use, as the runner system can be designed to minimize waste and can be automatically separated from the part.
-
Two-Plate Mold:
-
Application Suitability:
-
Two-Plate Mold:
- Best suited for simpler parts with fewer gates and where cost and lead time are critical factors.
-
Three-Plate Mold:
- Best suited for more complex parts requiring multiple gates, automatic runner separation, and where design flexibility is more important than cost and lead time.
-
Two-Plate Mold:
In summary, the choice between a two-plate mold and a three-plate mold depends on the specific requirements of the part being produced. A two-plate mold is more cost-effective and faster to produce, making it ideal for simpler parts. In contrast, a three-plate mold offers greater design flexibility and material efficiency, making it suitable for more complex parts.
Summary Table:
Feature | Two-Plate Mold | Three-Plate Mold |
---|---|---|
Design Complexity | Simpler design, fewer components | More complex design, additional mechanisms |
Cost | Lower cost | Higher cost |
Lead Time | Shorter lead time | Longer lead time |
Cycle Time | Lower cycle time | Higher cycle time |
Design Flexibility | Limited flexibility | Greater flexibility |
Runner System | Part and runner ejected together | Automatic separation of runners and parts |
Ejection Mechanism | Simpler ejection mechanism | More complex ejection mechanism |
Material Efficiency | Less efficient material use | More efficient material use |
Application Suitability | Best for simpler parts | Best for complex parts |
Need help choosing the right mold for your project? Contact our experts today for personalized advice!