Chemical vapor deposition (CVD) is a highly advantageous technique for depositing thin films and coatings across a wide range of materials. It is cost-effective, versatile, and capable of producing high-purity, uniform, and durable coatings with excellent adhesion properties. CVD is particularly notable for its ability to coat complex and precision surfaces, withstand extreme environments, and allow precise control over deposition parameters. Additionally, it offers improved performance in terms of thickness control, surface smoothness, and conductivity, making it ideal for applications in electronics, optics, and protective coatings. Its non-line-of-sight process further enhances its utility in industrial and scientific applications.
Key Points Explained:
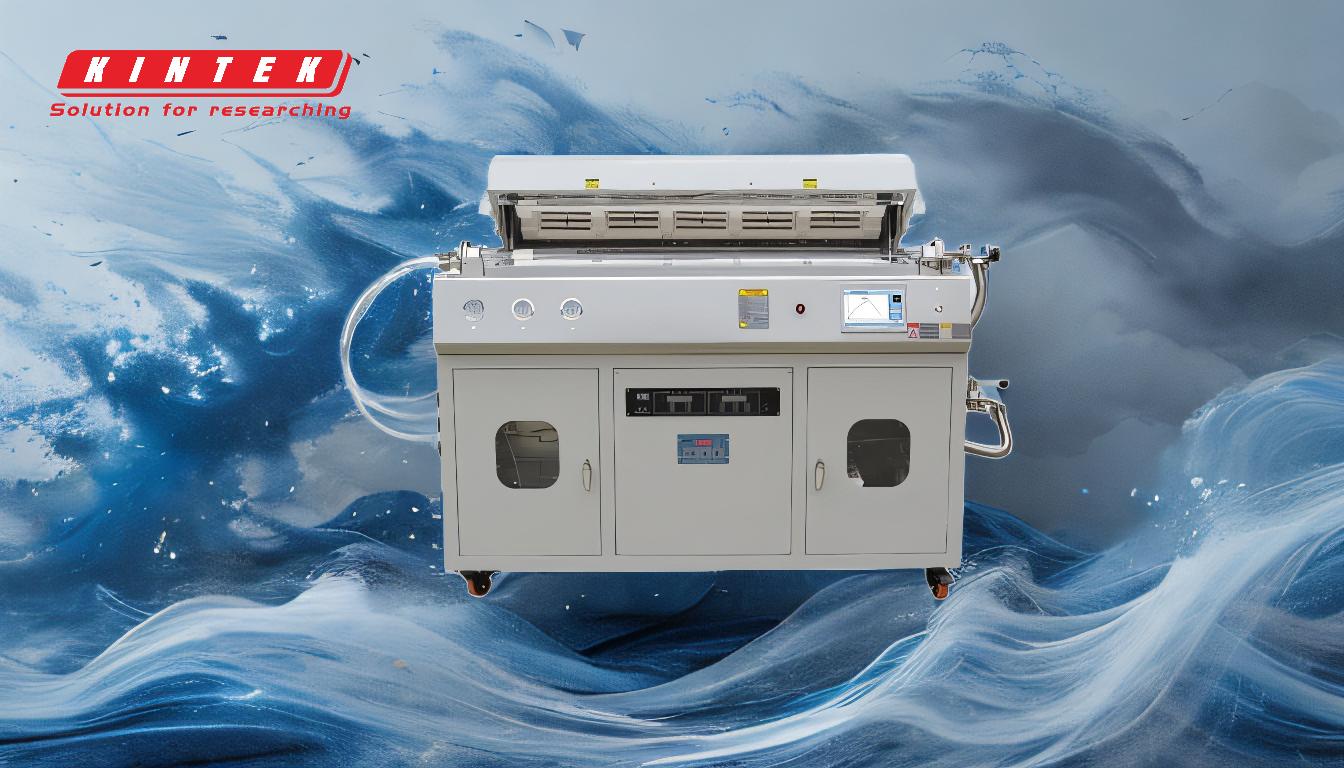
-
Versatility in Material Application
- CVD can be applied to a wide variety of materials, including ceramics, metals, glass, and polymers. This makes it suitable for diverse industries, from electronics to aerospace.
- The process allows for the optimization of gases to achieve specific properties such as corrosion resistance, abrasion resistance, or high purity, depending on the application.
-
High-Quality Coatings
- CVD produces coatings with high purity and density, ensuring excellent performance in demanding environments.
- The films exhibit low residual stress, good crystallinity, and uniform thickness, which are critical for applications requiring precision and durability.
-
Ability to Coat Complex Surfaces
- CVD has excellent wrap-around properties, enabling it to coat intricate and complex geometries with uniform thickness. This is particularly useful for precision components and devices.
- The non-line-of-sight nature of the process ensures that even hard-to-reach areas are adequately coated.
-
Durability in Extreme Conditions
- Coatings produced by CVD are highly durable and can withstand high-stress environments, extreme temperatures, and rapid temperature variations.
- This makes CVD ideal for applications in harsh conditions, such as in aerospace or high-temperature industrial processes.
-
Precise Control Over Deposition Parameters
- CVD allows for fine-tuning of deposition parameters, such as temperature, pressure, and gas composition, to achieve desired film properties.
- This control enables the production of ultra-thin layers, which are essential for applications like semiconductor manufacturing and electrical circuits.
-
Improved Performance Metrics
- Compared to other deposition technologies, CVD offers better thickness control, smoother surfaces, and enhanced electrical and thermal conductivity.
- It also provides better mixing compatibility with other materials and has a reduced environmental impact, such as a lower CO2 footprint.
-
Simplicity and Ease of Operation
- CVD equipment is relatively simple to operate and maintain, making it accessible for both industrial and research settings.
- The process is scalable, allowing for both small-scale laboratory experiments and large-scale industrial production.
-
Ideal for Advanced Applications
- Techniques like microwave plasma chemical vapor deposition further enhance the capabilities of CVD, enabling the deposition of high-quality films at lower temperatures and with greater precision.
- This makes CVD indispensable for cutting-edge applications in nanotechnology, optoelectronics, and protective coatings.
In summary, chemical vapor deposition is a highly versatile and efficient technique that offers numerous advantages, including high-quality coatings, precise control, and durability in extreme conditions. Its ability to coat complex surfaces and adapt to various materials makes it a preferred choice for a wide range of industrial and scientific applications.
Summary Table:
Advantage | Description |
---|---|
Versatility | Applicable to ceramics, metals, glass, and polymers for diverse industries. |
High-Quality Coatings | Produces high-purity, dense, and uniform coatings with excellent adhesion. |
Complex Surface Coating | Coats intricate geometries with uniform thickness, even in hard-to-reach areas. |
Durability in Extreme Conditions | Withstands high stress, extreme temperatures, and rapid temperature changes. |
Precise Control | Fine-tunes temperature, pressure, and gas composition for desired properties. |
Improved Performance Metrics | Offers better thickness control, smoother surfaces, and enhanced conductivity. |
Ease of Operation | Simple to operate and maintain, scalable for labs and industrial production. |
Advanced Applications | Ideal for nanotechnology, optoelectronics, and protective coatings. |
Unlock the potential of chemical vapor deposition for your applications—contact our experts today!