Chemical Vapor Deposition (CVD) and Physical Vapor Deposition (PVD) are two widely used thin-film deposition techniques, each offering unique advantages depending on the application. CVD excels in producing high-purity, uniform films with excellent thickness control and the ability to coat complex geometries, including deep holes and shaded areas. It is highly scalable, economical for thick coatings, and operates at atmospheric pressure, making it versatile for various materials and environments. PVD, on the other hand, is known for its precision, ability to deposit high-quality films at lower temperatures, and suitability for applications requiring fine control over film properties. Both methods have distinct strengths that make them suitable for different industrial and research needs.
Key Points Explained:
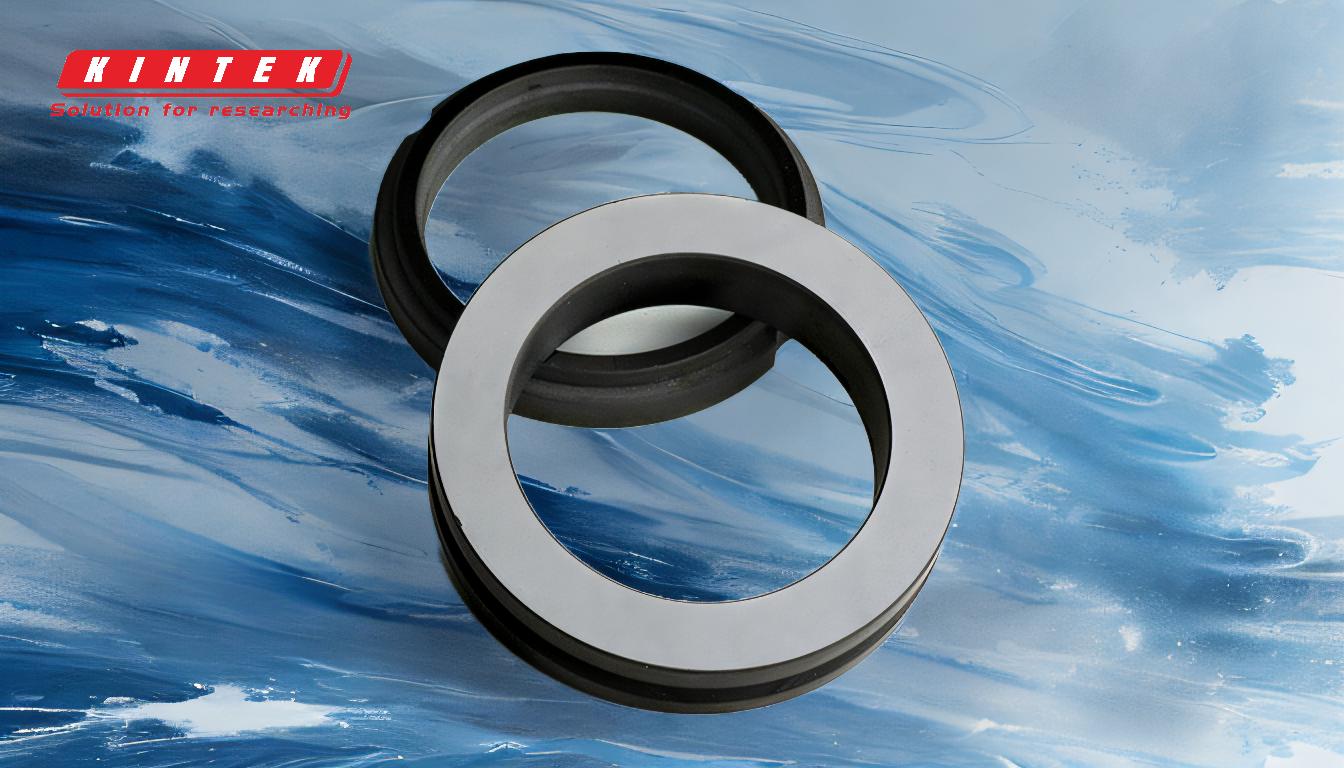
-
Advantages of CVD Over PVD:
- Line-of-Sight Deposition: Unlike PVD, CVD is not limited by line-of-sight effects, enabling it to coat complex shapes, deep holes, and recesses with high throwing power. This makes it ideal for applications requiring uniform coverage on intricate surfaces.
- Material Versatility: CVD can deposit a wide range of materials, including ceramics, metals, and glass, and can optimize gases for properties like corrosion resistance, abrasion resistance, or high purity.
- Scalability and Economical Production: CVD offers high deposition rates, making it suitable for large-scale manufacturing. It is also more economical for producing thick coatings compared to PVD.
- Atmospheric Pressure Operation: CVD can be performed at atmospheric pressure, eliminating the need for ultra-high vacuum systems, which simplifies the process and reduces costs.
-
Superior Film Quality and Control:
- High Purity and Uniformity: CVD allows for the deposition of high-purity films by purifying precursor gases and controlling deposition parameters like temperature, pressure, and gas flow rate. This results in uniform thickness and composition.
- Thickness Control: CVD provides excellent control over film thickness, producing smoother surfaces and better electrical and thermal conductivity compared to other deposition methods like pitch coating.
- Adjustable Properties: The chemical and physical properties of CVD films can be tailored by adjusting deposition parameters, making it suitable for a wide range of applications.
-
Flexibility in Deposition:
- Codeposition of Materials: CVD allows for the codeposition of different materials, enabling the creation of complex, multi-component films with specific properties.
- Plasma and Initiator Inclusion: The inclusion of plasma or initiators during CVD can enhance reactivity and improve film properties, offering greater flexibility in the deposition process.
-
Environmental and Performance Benefits:
- Reduced CO2 Footprint: CVD has a lower environmental impact compared to other deposition technologies, such as pitch coating, due to its efficient use of materials and energy.
- Durability in Extreme Conditions: CVD coatings are highly durable and can withstand high-stress environments, extreme temperatures, and temperature variations, making them suitable for demanding applications.
-
Advantages of PVD:
- Precision and Low-Temperature Deposition: PVD is known for its ability to deposit high-quality films at lower temperatures, which is beneficial for temperature-sensitive substrates.
- Fine Control Over Film Properties: PVD allows for precise control over film properties, such as adhesion, hardness, and density, making it suitable for applications requiring high-performance coatings.
In summary, CVD and PVD each have distinct advantages that make them suitable for different applications. CVD is ideal for coating complex geometries, producing high-purity films, and scaling up production, while PVD excels in precision and low-temperature deposition. The choice between the two depends on the specific requirements of the application, such as film properties, substrate material, and environmental conditions.
Summary Table:
Aspect | CVD Advantages | PVD Advantages |
---|---|---|
Deposition Method | Not limited by line-of-sight effects; coats complex geometries. | Requires line-of-sight; precise control over film properties. |
Material Versatility | Deposits ceramics, metals, glass; optimizes gases for specific properties. | Deposits metals, alloys, and compounds; fine control over film adhesion/hardness. |
Scalability | High deposition rates; economical for thick coatings; scalable for large production. | Suitable for small-scale, high-precision applications. |
Environmental Impact | Lower CO2 footprint; operates at atmospheric pressure. | Requires vacuum systems; lower energy consumption for low-temperature processes. |
Film Quality | High purity, uniformity, and thickness control; adjustable properties. | High-quality films with fine control over density and hardness. |
Temperature Sensitivity | Operates at higher temperatures; durable in extreme conditions. | Deposits films at lower temperatures; ideal for temperature-sensitive substrates. |
Need help choosing between CVD and PVD for your application? Contact our experts today for tailored advice!