The advantages of the Chemical Vapor Deposition (CVD) process are numerous, particularly when compared to other material deposition techniques. CVD allows for the creation of high-purity, high-performance solid materials, often with superior properties such as hardness, thermal stability, and chemical resistance. The process is highly versatile, capable of depositing a wide range of materials including metals, ceramics, and polymers onto various substrates. Additionally, CVD can produce uniform coatings even on complex geometries, making it ideal for applications in electronics, optics, and protective coatings. The process is also scalable, making it suitable for both small-scale laboratory research and large-scale industrial production.
Key Points Explained:
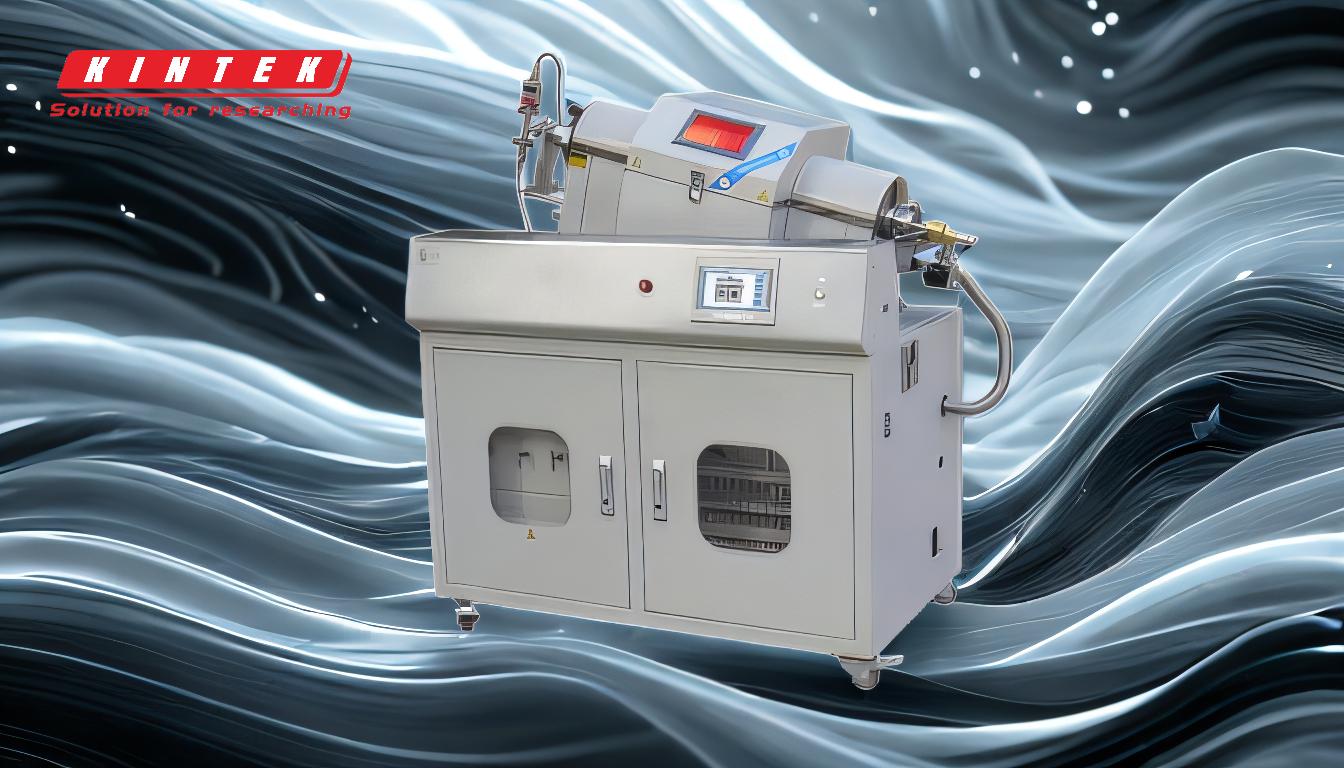
-
High Purity and Performance:
- CVD enables the deposition of materials with exceptional purity, which is crucial for applications requiring high-performance materials. The process involves the chemical reaction of gaseous precursors, which decompose to form a solid material on the substrate. This results in coatings that are free from impurities, leading to materials with superior mechanical, thermal, and chemical properties.
-
Versatility in Material Deposition:
- CVD is capable of depositing a wide variety of materials, including metals, ceramics, and polymers. This versatility makes it a preferred method for creating coatings and thin films in industries ranging from electronics to aerospace. For example, CVD is used to deposit silicon dioxide in semiconductor manufacturing and to create diamond-like carbon coatings for wear resistance.
-
Uniform Coatings on Complex Geometries:
- One of the standout advantages of CVD is its ability to produce uniform coatings even on substrates with complex shapes. This is particularly important in applications such as turbine blades, where a consistent coating is necessary to protect against high temperatures and corrosive environments. The process ensures that the coating thickness is even across the entire surface, regardless of the substrate's geometry.
-
Scalability:
- CVD is highly scalable, making it suitable for both small-scale research and large-scale industrial production. This scalability is a significant advantage for manufacturers who need to produce large quantities of coated materials without compromising on quality. The process can be adjusted to accommodate different production volumes, from laboratory-scale experiments to mass production.
-
Cost-Effectiveness and Efficiency:
- Compared to other deposition techniques, CVD can be more cost-effective, especially when considering the high quality and performance of the resulting materials. The process is efficient, with minimal waste, and can be easily modified for different applications. Additionally, the use of short path vacuum distillation in related processes can further enhance efficiency by reducing the boiling points of compounds, thereby lowering energy consumption and preventing thermal degradation.
-
Enhanced Control and Precision:
- CVD offers precise control over the deposition process, allowing for the creation of materials with specific properties. This precision is achieved through careful regulation of the reaction conditions, such as temperature, pressure, and gas flow rates. The ability to fine-tune these parameters ensures that the resulting materials meet the exact requirements of the intended application.
In summary, the CVD process offers a combination of high purity, versatility, uniformity, scalability, cost-effectiveness, and precision, making it a highly advantageous method for material deposition in a wide range of industries. The integration of technologies like short path vacuum distillation further enhances the efficiency and quality of the process, ensuring that CVD remains a leading choice for advanced material synthesis.
Summary Table:
Advantage | Description |
---|---|
High Purity and Performance | Produces materials with exceptional purity, superior mechanical and thermal properties. |
Versatility | Deposits metals, ceramics, and polymers for diverse applications. |
Uniform Coatings | Ensures even coatings on complex geometries, ideal for protective and functional layers. |
Scalability | Suitable for both small-scale research and large-scale industrial production. |
Cost-Effectiveness | Efficient process with minimal waste, enhanced by technologies like short path vacuum distillation. |
Enhanced Control and Precision | Offers precise control over deposition parameters for tailored material properties. |
Learn how the CVD process can transform your material synthesis—contact our experts today!