DC magnetron sputtering is a highly efficient and versatile thin-film deposition technique widely used in industries such as microelectronics, optics, and surface engineering. It offers numerous advantages, including high deposition rates, precise control over film properties, and compatibility with a wide range of materials and substrates. The process is energy-efficient, scalable, and capable of producing high-quality films with excellent adhesion, uniformity, and purity. These features make it a preferred choice for applications requiring durable, functional, and high-performance coatings.
Key Points Explained:
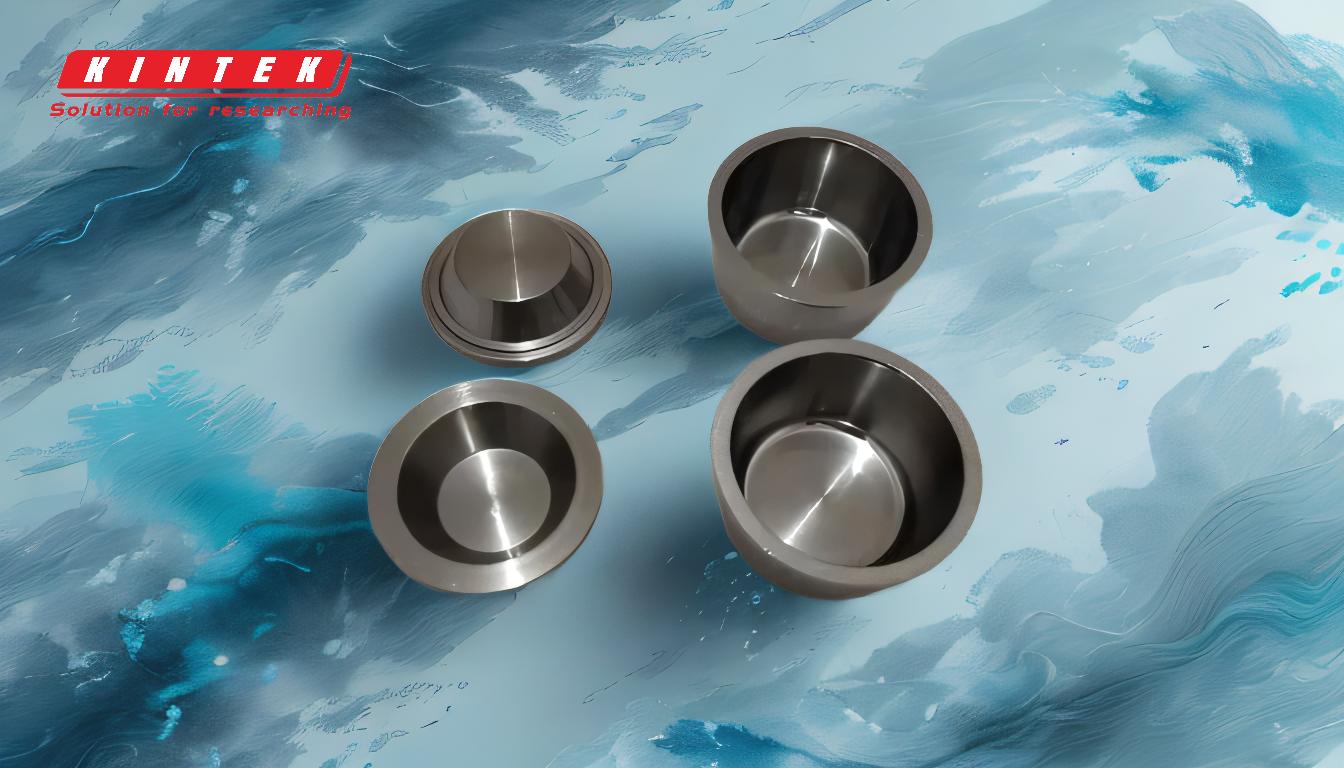
-
High Deposition Rates
- DC magnetron sputtering achieves significantly higher deposition rates compared to other sputtering methods, such as DC diode sputtering.
- For example, it can deposit metal films at rates as high as 2 μm/min, making it ideal for industrial-scale production.
- This efficiency reduces processing time and increases throughput, which is critical for large-scale manufacturing.
-
Precise Control Over Film Properties
- The process allows for precise control over film thickness, composition, and microstructure.
- This precision is essential for applications in microelectronics, where tailored film properties are required for optimal performance.
- The ability to deposit uniform films with minimal defects ensures high yield and reliability in semiconductor and optical applications.
-
Versatility in Material Compatibility
- DC magnetron sputtering can deposit a wide range of materials, including metals, alloys, oxides, nitrides, and even high-melting-point materials.
- It is compatible with various substrates, such as glass, metals, polymers, and heat-sensitive materials, making it suitable for diverse applications.
- This versatility enables its use in industries ranging from wear-resistant coatings to functional thin films in electronics.
-
Energy Efficiency and Low Thermal Load
- The process operates at low voltages and high currents, making it more energy-efficient than other sputtering techniques.
- The low thermal load minimizes damage to heat-sensitive substrates, such as polymers and textiles, while still achieving high-quality coatings.
- This feature is particularly advantageous for applications requiring low-temperature processing.
-
High-Quality Films with Excellent Adhesion
- Films produced by DC magnetron sputtering exhibit high density, purity, and strong adhesion to substrates.
- The process minimizes impurities and defects, resulting in coatings with superior mechanical, optical, and electrical properties.
- These characteristics are critical for applications such as corrosion-resistant coatings, optical films, and semiconductor devices.
-
Scalability and Industrialization
- DC magnetron sputtering is highly scalable, making it suitable for both small-scale research and large-scale industrial production.
- Modern systems are equipped with advanced automation and arc-handling capabilities, reducing downtime and improving process stability.
- Its ease of industrialization ensures consistent quality and cost-effectiveness in high-volume manufacturing.
-
Environmental Friendliness
- The process is environmentally friendly, as it operates in a vacuum environment, minimizing contamination and waste.
- It does not require hazardous chemicals or produce harmful byproducts, aligning with sustainable manufacturing practices.
- This advantage is increasingly important in industries striving to reduce their environmental footprint.
-
Uniformity and High Yield
- DC magnetron sputtering produces films with excellent uniformity, which is critical for applications requiring tight tolerances, such as microelectronics and optics.
- The high yield and reproducibility of the process reduce material waste and improve cost efficiency.
- This uniformity also enhances the performance and durability of functional coatings.
-
Simultaneous Deposition of Multiple Materials
- The technique allows for the simultaneous sputtering of different materials, enabling the creation of complex multilayer or composite films.
- This capability is particularly useful for advanced applications, such as multilayer optical coatings and multifunctional thin films.
- It provides flexibility in designing coatings with tailored properties for specific applications.
-
Advancements in Technology
- Ongoing research and development continue to improve DC magnetron sputtering, enhancing its efficiency, versatility, and application range.
- Innovations in power supply technology, such as sophisticated arc-handling systems, have further reduced process instability and improved film quality.
- These advancements ensure that the technique remains at the forefront of thin-film deposition technologies.
By combining these advantages, DC magnetron sputtering stands out as a highly effective and adaptable method for producing high-performance coatings across a wide range of industries. Its ability to deliver precise, uniform, and durable films makes it an indispensable tool for modern manufacturing and research.
Summary Table:
Advantage | Description |
---|---|
High Deposition Rates | Achieves rates up to 2 μm/min, ideal for industrial-scale production. |
Precise Film Control | Enables exact control over thickness, composition, and microstructure. |
Material Compatibility | Deposits metals, alloys, oxides, and nitrides on various substrates. |
Energy Efficiency | Operates at low voltages, minimizing thermal load on heat-sensitive materials. |
High-Quality Films | Produces dense, pure, and strongly adherent coatings. |
Scalability | Suitable for both research and large-scale industrial production. |
Environmental Friendliness | Minimizes contamination and waste, aligning with sustainable practices. |
Uniformity and High Yield | Ensures consistent film quality, reducing material waste. |
Multi-Material Deposition | Enables creation of complex multilayer or composite films. |
Technological Advancements | Continuous improvements enhance efficiency, versatility, and film quality. |
Ready to enhance your thin-film deposition process? Contact us today to learn more about DC magnetron sputtering solutions!