Diamond-like carbon (DLC) coatings offer a range of advantages, making them highly desirable for industrial applications. These coatings are known for their excellent adhesion to various substrates, high hardness, and resistance to wear, corrosion, and friction. They can be deposited at relatively low temperatures, which is beneficial for heat-sensitive materials. Additionally, DLC coatings combine both diamond-like (Sp3) and graphite-like (Sp2) carbon bonds, providing a unique blend of hardness and low friction. These properties make DLC coatings ideal for enhancing the performance and longevity of components in demanding environments, while also reducing manufacturing costs by extending the life of existing parts.
Key Points Explained:
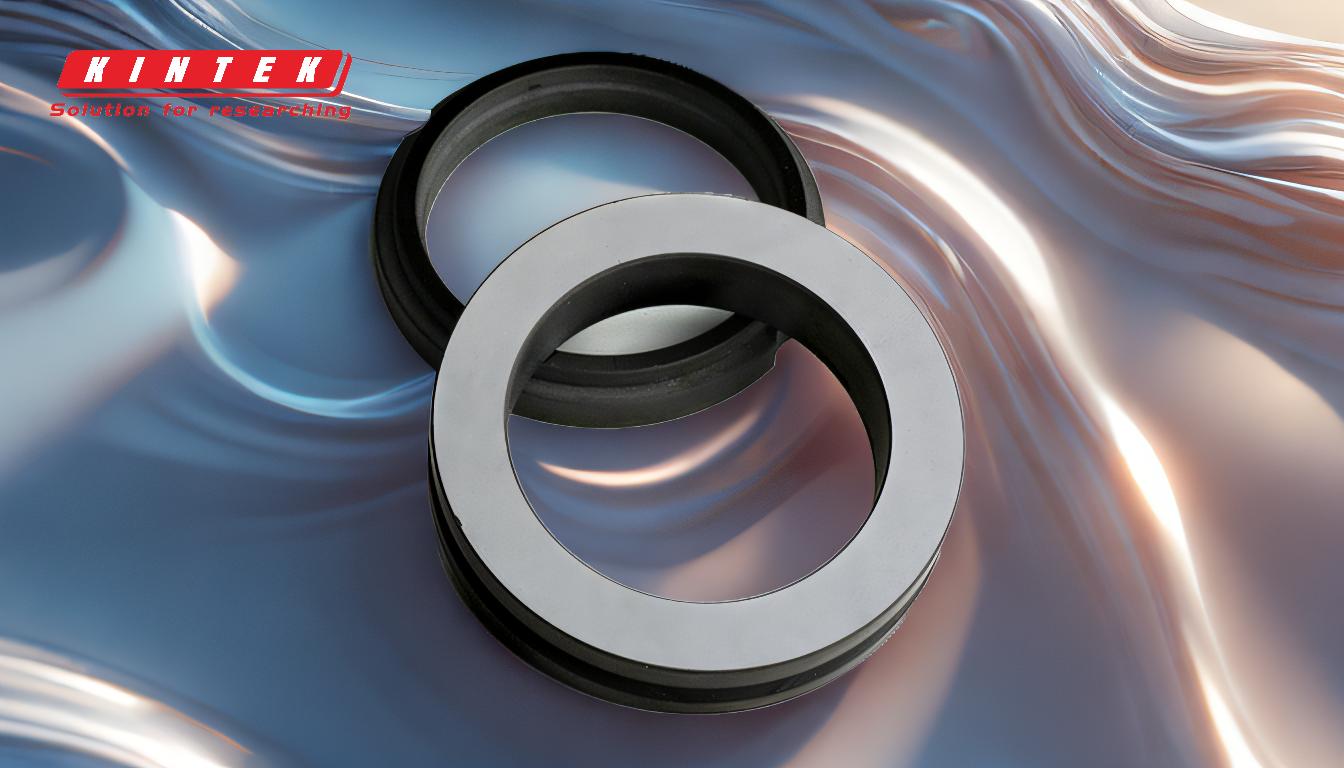
-
Excellent Adhesion to Substrates:
- DLC coatings exhibit strong adhesion to a wide range of substrates, including metals, ceramics, and polymers. This is achieved through the use of bonding layers, such as silicon-based films, which enhance the adhesion strength.
- The ability to adhere well to different materials makes DLC coatings versatile and applicable in various industries, from automotive to medical devices.
-
High Hardness and Wear Resistance:
- DLC coatings are characterized by their high hardness, which is comparable to that of diamond. This hardness is due to the presence of Sp3 (diamond-like) carbon bonds.
- The high hardness translates to excellent wear resistance, making DLC coatings ideal for components subjected to abrasive or erosive conditions, such as cutting tools, engine parts, and bearings.
-
Low Coefficient of Friction:
- The presence of Sp2 (graphite-like) carbon bonds in DLC coatings contributes to a low coefficient of friction. This property is particularly beneficial in applications where sliding or moving parts are involved.
- The low friction reduces energy loss and wear, leading to improved efficiency and longer service life of components.
-
Chemical and Corrosion Resistance:
- DLC coatings are highly resistant to chemical attack and corrosion, making them suitable for use in harsh environments, such as those involving exposure to acids, alkalis, or saltwater.
- This resistance is crucial for applications in the chemical processing industry, marine environments, and medical implants, where materials must withstand aggressive conditions.
-
Deposition at Low Temperatures:
- One of the significant advantages of DLC coatings is that they can be deposited at relatively low temperatures, typically around 300 °C. This is particularly advantageous for heat-sensitive substrates that cannot withstand high-temperature processes.
- The low-temperature deposition process expands the range of materials that can be coated with DLC, including polymers and certain alloys.
-
Cost-Effectiveness:
- By applying DLC coatings to existing parts, manufacturers can significantly extend the life of these components, reducing the need for frequent replacements. This leads to cost savings in terms of material and fabrication expenses.
- The protective functions of DLC coatings also reduce downtime and maintenance costs, contributing to overall operational efficiency.
-
Versatility in Applications:
- Due to their unique combination of properties, DLC coatings are used in a wide range of applications. These include automotive components (e.g., piston rings, fuel injectors), cutting tools, medical devices (e.g., surgical instruments, implants), and even consumer electronics (e.g., smartphone screens).
- The ability to tailor the properties of DLC coatings by adjusting the deposition process further enhances their versatility.
-
Enhanced Tribological Properties:
- DLC coatings improve the tribological properties of materials, such as reducing friction and wear. This is particularly important in applications where components are in constant contact and subject to high stress.
- The improved tribological performance leads to smoother operation, reduced energy consumption, and longer component life.
-
Environmental Benefits:
- The use of DLC coatings can contribute to environmental sustainability by reducing the need for new materials and minimizing waste. By extending the life of components, DLC coatings help reduce the environmental impact associated with manufacturing and disposal.
- Additionally, the low friction properties of DLC coatings can lead to energy savings, further contributing to environmental benefits.
In summary, DLC coatings offer a comprehensive set of advantages, including strong adhesion, high hardness, low friction, chemical resistance, and cost-effectiveness. These properties make DLC coatings an excellent choice for enhancing the performance and durability of components across a wide range of industries.
Summary Table:
Advantage | Description |
---|---|
Excellent Adhesion | Strong bonding to metals, ceramics, and polymers for versatile applications. |
High Hardness | Comparable to diamond, ideal for wear-resistant components. |
Low Friction | Reduces energy loss and wear, improving efficiency. |
Chemical Resistance | Resists acids, alkalis, and saltwater for harsh environments. |
Low-Temperature Deposition | Suitable for heat-sensitive materials like polymers. |
Cost-Effectiveness | Extends component life, reducing replacement and maintenance costs. |
Versatility | Used in automotive, medical, and consumer electronics industries. |
Environmental Benefits | Reduces waste and energy consumption, promoting sustainability. |
Enhance your components with DLC coatings—contact us today to learn more!