E-beam evaporation offers several advantages over thermal evaporation, making it a preferred choice for many thin-film deposition applications. The primary benefits include higher purity of the deposited films, better control over the evaporation process, the ability to handle materials with higher melting points, and improved deposition rates. E-beam evaporation also minimizes contamination risks by keeping the crucible cool and only heating the target material. These features make it suitable for applications requiring high-purity, dense, and uniform coatings, especially in industries like semiconductors, optics, and advanced materials.
Key Points Explained:
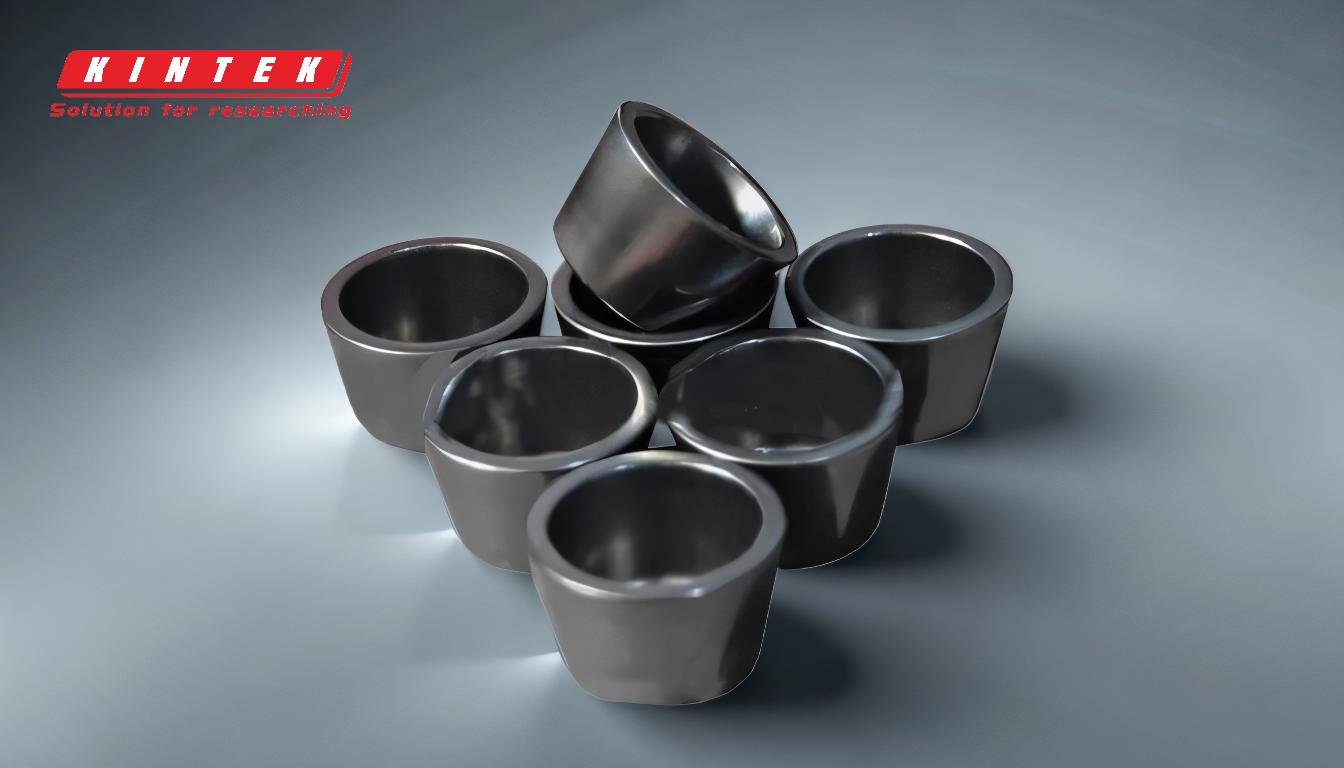
-
Higher Purity of Thin Films:
- E-beam evaporation produces thin films with significantly higher purity compared to thermal evaporation. This is because the electron beam directly heats only the target material, while the crucible remains at room temperature, preventing contamination from impurities.
- In thermal evaporation, the entire crucible is heated, which can lead to contamination of the deposited film due to reactions between the source material and the crucible at high temperatures.
-
Ability to Handle High-Melting-Point Materials:
- E-beam evaporation can deposit materials with high melting points, such as oxides and refractory metals, which are challenging or impossible to process using thermal evaporation.
- Thermal evaporation is limited to materials with lower melting temperatures, restricting its applicability for advanced materials.
-
Precise Control Over the Evaporation Process:
- The use of a high-energy electron beam in e-beam evaporation allows for precise control over the evaporation rate and deposition process. This precision is critical for applications requiring uniform and consistent thin films.
- Thermal evaporation relies on heating the crucible, which offers less control and can lead to inconsistent evaporation rates.
-
Higher Deposition Rates:
- E-beam evaporation provides higher deposition rates compared to thermal evaporation, making it more efficient for large-scale or high-throughput applications.
- The increased deposition rate is particularly beneficial for industrial applications where time and cost efficiency are critical.
-
Denser and More Uniform Coatings:
- E-beam evaporation results in denser thin film coatings with excellent adhesion to the substrate. This is due to the high-energy process and the ability to control the deposition parameters precisely.
- The use of masks and planetary systems in e-beam evaporation further enhances coating uniformity, which is essential for applications in optics and electronics.
-
Reduced Risk of Contamination:
- The cooling of the crucible in e-beam evaporation prevents contamination from impurities, ensuring high-purity films. This is particularly important for applications in semiconductors and other high-tech industries.
- Thermal evaporation, on the other hand, involves heating the crucible, which can introduce impurities and degrade film quality.
-
Compatibility with Ion-Assisted Deposition (IAD):
- E-beam evaporation systems can be integrated with ion assist sources for pre-cleaning or ion-assisted deposition (IAD). This capability enhances film properties, such as adhesion and density, making it suitable for advanced applications.
- Thermal evaporation does not offer this level of integration, limiting its versatility.
-
Better Step Coverage:
- E-beam evaporation provides superior step coverage compared to sputtering or chemical vapor deposition (CVD). This is particularly advantageous for coating complex geometries or substrates with intricate features.
- Thermal evaporation typically struggles with step coverage, leading to uneven coatings on such substrates.
-
Higher Material Utilization Efficiency:
- E-beam evaporation offers higher material utilization efficiency compared to sputtering, reducing material waste and lowering costs.
- This efficiency is another reason why e-beam evaporation is preferred for high-value materials and large-scale production.
-
Versatility for a Wide Range of Materials:
- E-beam evaporation is compatible with a wide variety of materials, including metals, oxides, and alloys. This versatility makes it suitable for diverse applications across multiple industries.
- Thermal evaporation is more limited in the range of materials it can process, restricting its use to simpler applications.
In summary, e-beam evaporation outperforms thermal evaporation in terms of purity, control, material versatility, and deposition efficiency. These advantages make it the preferred method for applications requiring high-quality, uniform, and contamination-free thin films.
Summary Table:
Advantage | E-beam Evaporation | Thermal Evaporation |
---|---|---|
Purity of Thin Films | Higher purity due to direct heating of target material and cool crucible. | Lower purity due to heating of the entire crucible, risking contamination. |
High-Melting-Point Materials | Can handle materials like oxides and refractory metals. | Limited to materials with lower melting points. |
Control Over Evaporation | Precise control over evaporation rate and deposition process. | Less control, leading to inconsistent evaporation rates. |
Deposition Rates | Higher deposition rates, ideal for large-scale applications. | Lower deposition rates, less efficient for high-throughput needs. |
Coating Uniformity | Denser, more uniform coatings with excellent adhesion. | Less uniform coatings, especially on complex geometries. |
Contamination Risk | Reduced contamination due to cool crucible. | Higher contamination risk from heated crucible. |
Ion-Assisted Deposition (IAD) | Compatible with IAD for enhanced film properties. | Not compatible with IAD, limiting versatility. |
Step Coverage | Superior step coverage for complex geometries. | Poor step coverage, leading to uneven coatings. |
Material Utilization Efficiency | Higher efficiency, reducing waste and costs. | Lower efficiency, resulting in more material waste. |
Material Versatility | Compatible with metals, oxides, and alloys for diverse applications. | Limited to simpler materials, restricting its use. |
Ready to elevate your thin-film deposition process? Contact us today to learn how e-beam evaporation can meet your needs!