Induction coils, a core component of induction heating systems, offer numerous advantages that make them highly desirable in various industrial and manufacturing applications. These advantages stem from the unique way induction heating works—using electromagnetic waves to generate heat directly within the material being processed. This method ensures rapid, clean, and non-polluting heating, with no direct contact between the heat source and the material, eliminating contamination risks. Below, we delve into the key advantages of induction coils in detail.
Key Points Explained:
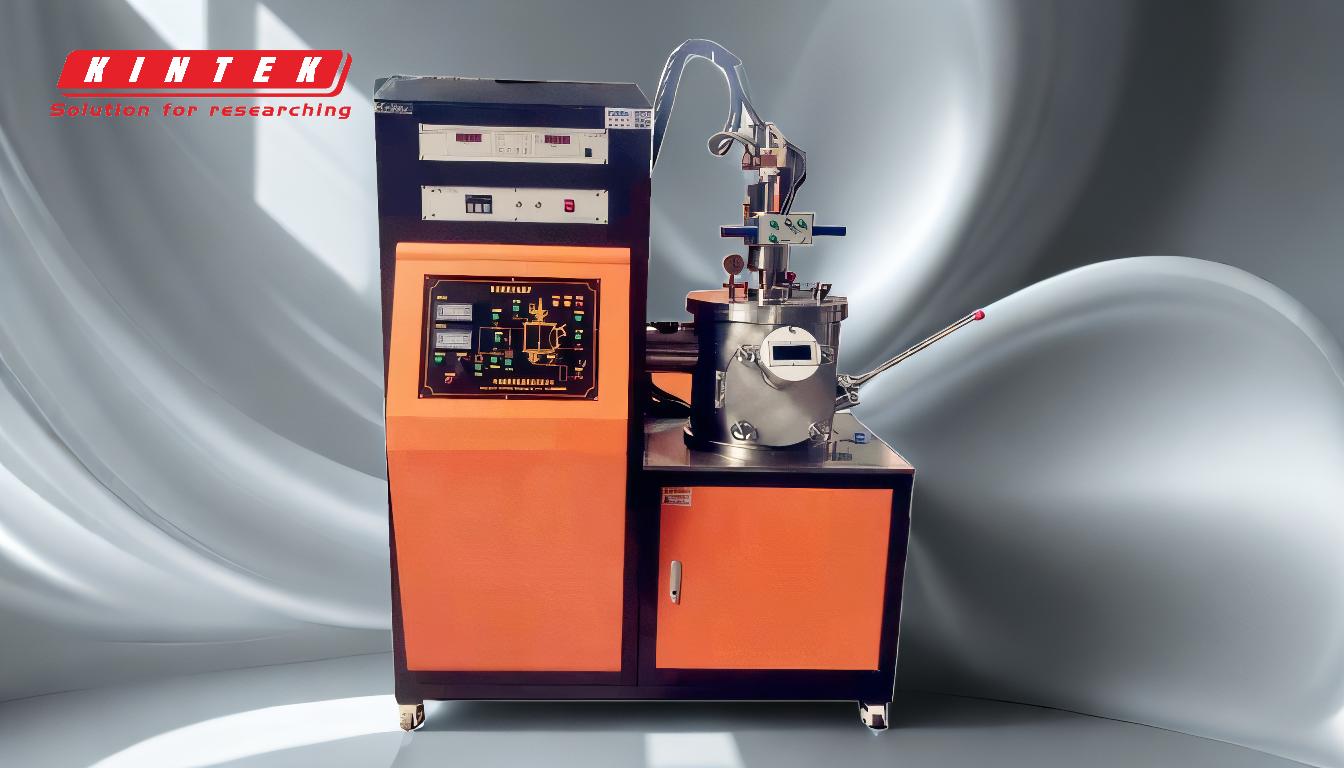
-
Rapid Heating
- Induction coils enable extremely fast heating compared to traditional methods like flame or convection heating. The electromagnetic waves generated by the coil directly induce eddy currents within the conductive material, creating heat almost instantaneously.
- This rapid heating is particularly beneficial in high-speed manufacturing processes, where time efficiency is critical. For example, in metal forging or heat treatment, induction coils can significantly reduce cycle times.
-
Clean and Non-Polluting
- Induction heating is an environmentally friendly process. Unlike combustion-based heating methods, it does not produce harmful emissions, smoke, or soot.
- The absence of open flames or direct contact with heating elements ensures that the process remains clean, making it ideal for industries with strict environmental regulations, such as food processing or pharmaceuticals.
-
Non-Contact Heating
- One of the most significant advantages of induction coils is that they heat materials without direct physical contact. This eliminates the risk of contamination, which is crucial in industries like medical device manufacturing or semiconductor production.
- Non-contact heating also reduces wear and tear on equipment, as there is no friction or physical interaction between the coil and the material being heated.
-
Precise and Controllable Heating
- Induction coils allow for precise control over the heating process. By adjusting the frequency and power of the electromagnetic field, operators can target specific areas of a material with high accuracy.
- This precision is invaluable in applications like brazing, soldering, or hardening, where localized heating is required to achieve desired material properties without affecting surrounding areas.
-
Energy Efficiency
- Induction heating is highly energy-efficient because the heat is generated directly within the material, minimizing energy loss. Traditional heating methods often lose significant energy to the surrounding environment.
- This efficiency translates to lower operational costs and reduced energy consumption, making induction coils a cost-effective solution in the long run.
-
Consistency and Repeatability
- Induction coils provide consistent and repeatable heating results, which is essential for maintaining product quality in mass production.
- The ability to precisely control the heating process ensures that each part is heated uniformly, reducing defects and improving overall product reliability.
-
Compact and Versatile Design
- Induction coils are compact and can be designed in various shapes and sizes to suit specific applications. This versatility makes them suitable for a wide range of industries, from automotive to electronics.
- Their compact design also allows for easy integration into existing production lines without requiring significant modifications.
-
Reduced Maintenance Requirements
- Since induction coils do not come into direct contact with the material being heated, they experience minimal wear and tear. This reduces the need for frequent maintenance and extends the lifespan of the equipment.
- Additionally, the absence of combustion byproducts means there is no buildup of residue or contaminants on the coils, further lowering maintenance demands.
-
Improved Safety
- Induction heating is inherently safer than traditional methods. The absence of open flames reduces the risk of fire hazards, and the non-contact nature of the process minimizes the risk of burns or injuries to operators.
- Advanced induction systems often include safety features like temperature monitoring and automatic shutoff, further enhancing workplace safety.
-
Wide Range of Applications
- Induction coils are used in diverse applications, including metal hardening, annealing, melting, brazing, and even cooking. Their adaptability makes them a valuable tool across multiple industries.
- For example, in the automotive industry, induction coils are used for hardening gears and shafts, while in the food industry, they are employed for precise heating in cooking processes.
In summary, induction coils offer a combination of speed, precision, cleanliness, and energy efficiency that makes them superior to traditional heating methods. Their non-contact nature ensures contamination-free processing, while their versatility and controllability make them suitable for a wide range of industrial applications. These advantages not only improve product quality and process efficiency but also contribute to cost savings and environmental sustainability. Whether in manufacturing, healthcare, or food processing, induction coils are a reliable and innovative solution for modern heating needs.
Summary Table:
Advantage | Description |
---|---|
Rapid Heating | Extremely fast heating compared to traditional methods, ideal for high-speed processes. |
Clean and Non-Polluting | No harmful emissions or open flames, making it eco-friendly and suitable for regulated industries. |
Non-Contact Heating | Eliminates contamination risks and reduces equipment wear and tear. |
Precise and Controllable | Allows for accurate, localized heating, perfect for brazing, soldering, and hardening. |
Energy Efficiency | Heat is generated directly within the material, minimizing energy loss and costs. |
Consistency and Repeatability | Ensures uniform heating, reducing defects and improving product quality. |
Compact and Versatile | Adaptable designs for various applications, easy to integrate into production lines. |
Reduced Maintenance | Minimal wear and tear, with no residue buildup, lowering maintenance needs. |
Improved Safety | No open flames or direct contact, reducing fire hazards and operator injuries. |
Wide Range of Applications | Used in industries like automotive, electronics, and food processing for diverse tasks. |
Ready to enhance your heating processes with induction coils? Contact us today to learn more!