Induction heating is a highly efficient, precise, and environmentally friendly method of heating conductive materials. It generates heat directly within the material using electromagnetic induction, eliminating the need for direct contact with flames or other heat sources. This process ensures rapid heating, precise control over temperature and depth, and minimal heat loss. Induction heating is also clean, non-polluting, and suitable for industrial automation, making it a preferred choice for applications requiring high efficiency, safety, and repeatability.
Key Points Explained:
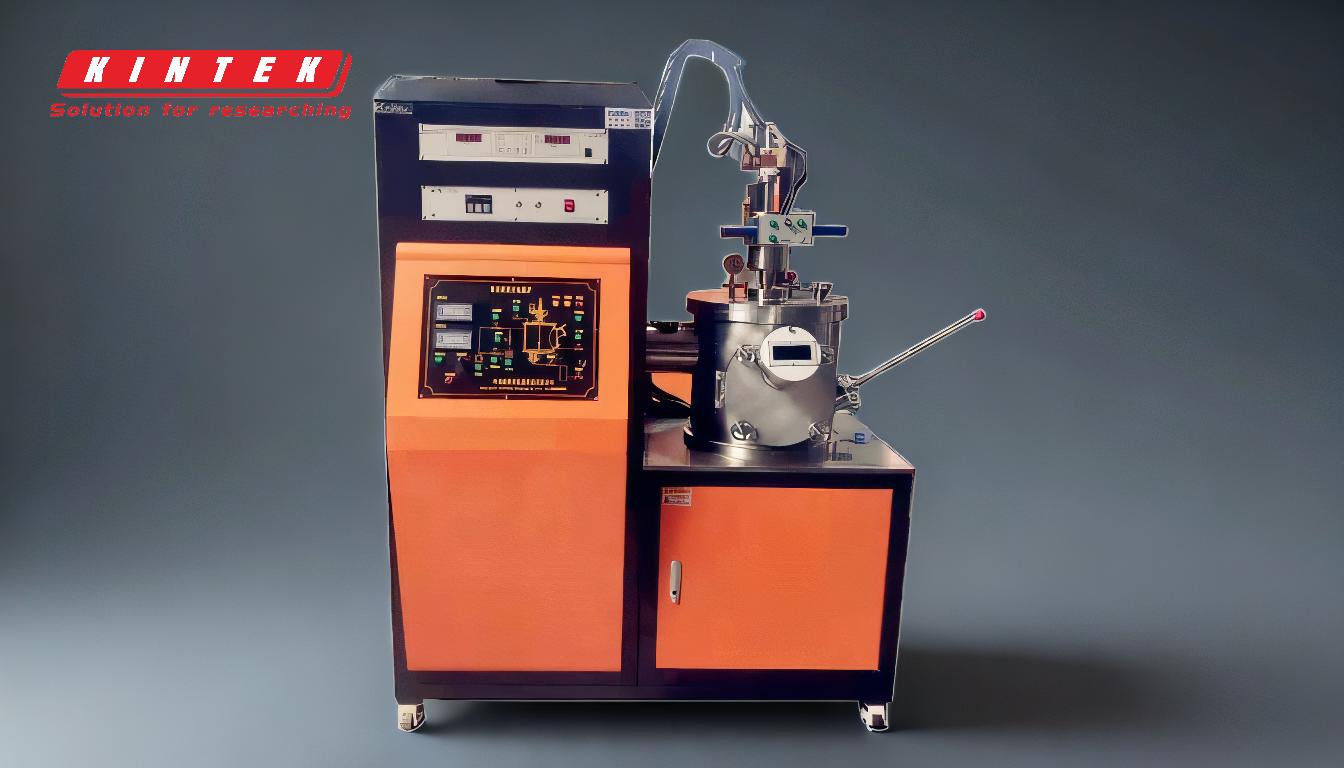
-
Rapid Heating and Reduced Processing Time
- Induction heating generates heat directly within the material through electromagnetic induction, allowing for extremely fast heating rates.
- This rapid heating reduces processing times significantly compared to traditional methods like gas furnaces or salt baths, which rely on slower heat transfer mechanisms such as convection and radiation.
- The ability to heat materials quickly improves productivity, making induction heating ideal for high-volume industrial applications.
-
High Efficiency and Energy Savings
- Induction heating systems boast high efficiency, often exceeding 90%.
- Heat is generated directly within the material, minimizing heat loss to the surrounding environment.
- This efficiency translates to reduced energy consumption, lowering operational costs and making induction heating a more sustainable option compared to traditional heating methods.
-
Precise Control Over Heating
- Induction heating allows for precise control over heating power, temperature, and depth.
- By adjusting the frequency of the electromagnetic current, operators can target specific depths within the material, ensuring uniform heating and avoiding overheating or underheating.
- This precision is critical for applications requiring consistent and repeatable results, such as heat treatment, brazing, and welding.
-
Clean and Non-Polluting Process
- Induction heating does not involve direct contact with flames or fuel substances, eliminating the risk of product contamination.
- The process is clean and non-polluting, as it does not produce harmful emissions or residues.
- This makes induction heating suitable for industries with strict cleanliness requirements, such as food processing, pharmaceuticals, and electronics manufacturing.
-
Improved Safety
- Since induction heating does not rely on open flames or combustible fuels, it significantly reduces the risk of fire hazards and accidents.
- The absence of direct contact with heat sources also minimizes the risk of burns or injuries to operators.
- This improved safety profile makes induction heating a preferred choice for workplaces prioritizing worker safety.
-
Industrial Automation Compatibility
- Induction heating systems are highly compatible with industrial automation, allowing for seamless integration into production lines.
- Automated systems can precisely control heating parameters, ensuring consistent quality and reducing the need for manual intervention.
- This compatibility enhances productivity and reduces labor costs, making induction heating ideal for modern manufacturing environments.
-
Reduced Maintenance and Longevity
- Induction heating systems have fewer moving parts and do not rely on combustion, reducing wear and tear.
- The absence of soot, ash, or other residues minimizes the need for frequent cleaning and maintenance.
- These factors contribute to longer equipment lifespans and lower maintenance costs over time.
-
Environmental Friendliness
- Induction heating is an environmentally friendly technology due to its high energy efficiency and lack of emissions.
- By reducing energy consumption and eliminating pollutants, induction heating supports sustainable manufacturing practices.
- This aligns with global efforts to reduce carbon footprints and promote green technologies.
-
Versatility Across Applications
- Induction heating is suitable for a wide range of applications, including metal hardening, annealing, forging, and brazing.
- Its ability to heat specific areas of a material without affecting surrounding regions makes it ideal for delicate or complex components.
- This versatility ensures that induction heating can meet the diverse needs of various industries.
-
No Product Contamination
- Since induction heating relies on electromagnetic waves to transfer heat, the material being heated never comes into direct contact with flames or other contaminants.
- This feature is particularly beneficial for industries requiring high-purity products, such as medical device manufacturing or semiconductor production.
- The elimination of contamination ensures product integrity and compliance with industry standards.
In summary, induction heating offers a combination of speed, precision, efficiency, and environmental benefits that make it a superior choice for many industrial applications. Its ability to deliver consistent, high-quality results while minimizing energy consumption and environmental impact positions it as a key technology for modern manufacturing.
Summary Table:
Key Benefit | Description |
---|---|
Rapid Heating | Achieves fast heating rates, reducing processing time and improving productivity. |
High Efficiency | Exceeds 90% efficiency, minimizing energy loss and lowering operational costs. |
Precise Control | Allows accurate temperature and depth control for consistent results. |
Clean and Non-Polluting | Eliminates emissions and contamination, ideal for clean industries. |
Improved Safety | Reduces fire hazards and operator injuries with no open flames. |
Automation Compatibility | Integrates seamlessly into automated production lines for enhanced productivity. |
Reduced Maintenance | Fewer moving parts and no combustion residues ensure longer equipment lifespan. |
Environmental Friendliness | Supports sustainability with low energy consumption and no emissions. |
Versatility | Suitable for diverse applications like hardening, annealing, and brazing. |
No Product Contamination | Ensures high-purity results for industries like medical and electronics. |
Ready to enhance your industrial processes with induction heating? Contact us today to learn more!