Induction melting is a highly efficient and versatile method for melting metals, offering numerous advantages over traditional melting techniques. It is a clean, energy-efficient, and well-controlled process that ensures uniform heating, fast production rates, and flexibility in handling different metals and alloys. Additionally, it is environmentally friendly, producing no harmful emissions, and is safe to operate, eliminating risks associated with flame or combustion heating. Induction melting also provides precise temperature regulation, homogeneous alloy composition, and cost-effectiveness, making it a preferred choice in various industrial applications.
Key Points Explained:
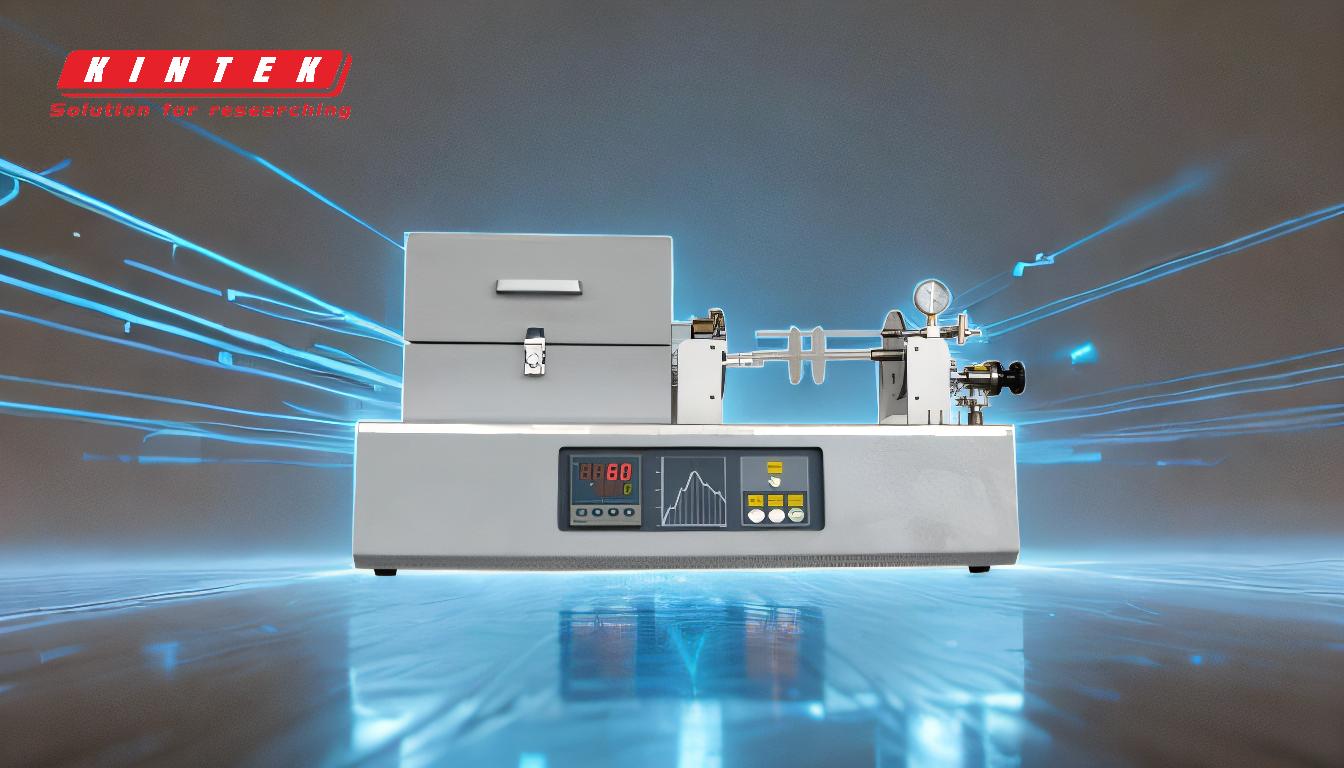
-
Clean and Environmentally Friendly Process
- Induction melting does not produce dust, smoke, or pollutants, making it an eco-friendly option.
- It emits no harmful emissions into the atmosphere, contributing to a cleaner working environment.
- This is particularly beneficial for industries aiming to reduce their environmental footprint.
-
Energy Efficiency
- The process minimizes heat losses, reducing energy consumption significantly.
- Heat is generated directly within the material through eddy currents, ensuring efficient energy use.
- This results in lower operational costs and a smaller carbon footprint.
-
Precise Temperature Control and Uniform Heating
- Induction melting allows for precise temperature regulation, ensuring consistent and uniform heating of the metal charge.
- This precision reduces the risk of defects and improves the quality of the final product.
- The ability to maintain tight compositional tolerances is especially valuable in producing high-performance alloys.
-
Fast Melting and High Production Rates
- Induction melting heats metals quickly, leading to faster production cycles and increased throughput.
- The rapid heating process also reduces defect rates and ensures repeatable results.
- This efficiency is crucial for industries requiring high-volume production.
-
Flexibility in Melting Different Metals and Alloys
- Induction furnaces can melt a wide range of metals and alloys, from small volumes to large-scale batches.
- The process allows for easy changeover between different materials, enhancing operational flexibility.
- Immediate shutdown capabilities further add to the convenience and safety of the process.
-
Safety and Risk Reduction
- Induction melting eliminates the risks of fire, explosion, or burns associated with flame or combustion heating.
- The absence of open flames and combustible materials makes it a safer option for operators.
- This safety feature is particularly important in high-risk industrial environments.
-
Homogeneous Alloy Composition
- The inductive stirring inherent in the process ensures a uniform mix of molten metal, leading to consistent alloy composition.
- This homogeneity is critical for producing high-quality metals with precise mechanical properties.
- It also aids in the dispersion of alloying elements, enhancing the final product's performance.
-
Cost-Effectiveness
- Induction melting is cost-effective due to its fast melting times, reduced energy consumption, and lower maintenance requirements.
- The absence of electrodes or fuel further reduces operational costs.
- Extended furnace life and minimal downtime contribute to long-term savings.
-
Vacuum Induction Melting (VIM) Advantages
- VIM allows melting under an oxygen-free atmosphere, preventing oxidation and reducing non-metallic inclusions.
- It achieves close compositional tolerances and low gas contents, ideal for high-purity applications.
- The elimination of a protective slag cover reduces the risk of contamination, ensuring cleaner ingots.
-
Automation and Customization
- Induction melting processes are easily automated, improving operational efficiency and reducing labor costs.
- The technology is highly customizable, allowing for tailored solutions to meet specific production needs.
- This adaptability makes it suitable for a wide range of industrial applications.
In summary, induction melting stands out as a superior method due to its environmental benefits, energy efficiency, precision, speed, flexibility, safety, and cost-effectiveness. These advantages make it an ideal choice for industries seeking high-quality, reliable, and sustainable metal melting solutions.
Summary Table:
Advantage | Description |
---|---|
Clean & Eco-Friendly | No dust, smoke, or harmful emissions; reduces environmental footprint. |
Energy Efficiency | Minimizes heat loss, reduces energy consumption, and lowers operational costs. |
Precise Temperature Control | Ensures uniform heating, reduces defects, and improves product quality. |
Fast Melting & High Production | Rapid heating speeds up production cycles and increases throughput. |
Flexibility | Handles various metals/alloys, easy changeover, and immediate shutdown. |
Safety | Eliminates risks of fire, explosion, or burns; no open flames. |
Homogeneous Alloy Composition | Ensures uniform mixing and consistent alloy composition. |
Cost-Effectiveness | Fast melting, low energy use, and minimal maintenance reduce long-term costs. |
Vacuum Induction Melting (VIM) | Prevents oxidation, achieves high purity, and reduces contamination risks. |
Automation & Customization | Easily automated and customizable for specific production needs. |
Ready to enhance your metal melting process? Contact us today to learn more about induction melting solutions!