Inert gases, such as nitrogen, argon, and helium, are widely used across various industries due to their non-reactive properties. Their primary advantage lies in their ability to prevent unwanted chemical reactions, such as oxidation and hydrolysis, which can degrade samples or materials. Inert gases are essential in creating controlled environments for chemical reactions, heat treatments, and industrial processes, reducing risks of contamination, fire, and explosions. They also enhance efficiency in processes like sputtering and deposition, where their high molecular weights contribute to higher rates. Overall, inert gases provide a stable, non-reactive atmosphere that ensures safety, quality, and precision in numerous applications.
Key Points Explained:
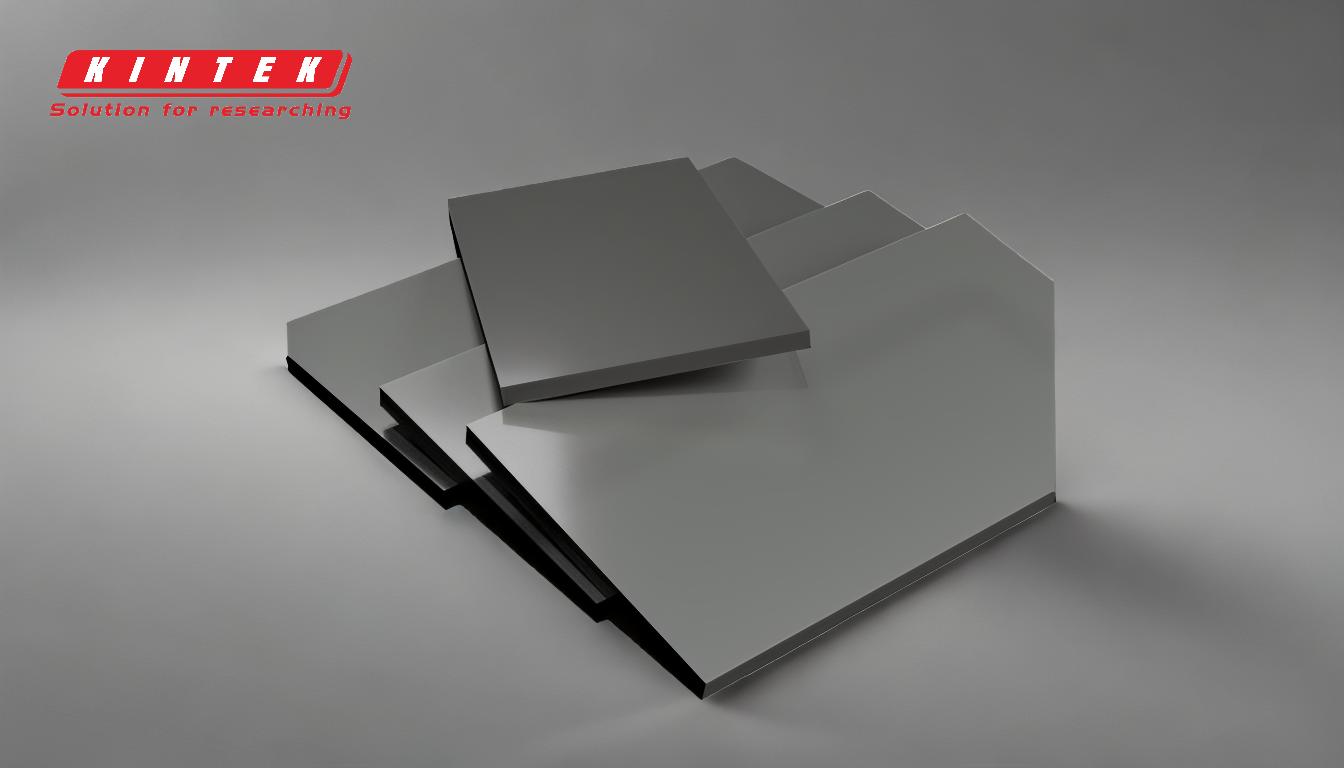
-
Prevention of Unwanted Chemical Reactions
- Inert gases are chemically non-reactive, making them ideal for preventing oxidation, hydrolysis, and other undesirable reactions.
- Oxidation, which occurs when materials react with oxygen, can degrade samples or alter their properties. Inert gases create an oxygen-free environment, preserving the integrity of sensitive materials.
- Hydrolysis, a reaction with moisture, is also minimized in inert atmospheres, ensuring stability in moisture-sensitive processes.
-
Reduction of Reaction Rates and Oxidation Potentials
- Inert gases slow down or inhibit chemical reactions, particularly those involving reactive gases like oxygen.
- This is crucial in industries such as pharmaceuticals, food packaging, and electronics, where even minor reactions can compromise product quality.
-
Fire and Explosion Prevention
- Inert gases are used to purge transfer lines, vessels, and reaction chambers, displacing oxygen and other reactive gases.
- This reduces the risk of fire or explosions, especially in industries handling flammable or volatile substances.
-
Contamination Control
- By replacing air with inert gases, the risk of contamination from airborne particles, moisture, or reactive gases is significantly reduced.
- This is particularly important in semiconductor manufacturing, where even trace contaminants can affect performance.
-
Enhanced Efficiency in Industrial Processes
- Inert gases like argon are used in sputtering processes due to their high molecular weights, which result in higher sputtering and deposition rates.
- Their non-reactive nature ensures that they do not interfere with the target material or process gases, maintaining process integrity.
-
Heat Treatment Applications
- Inert gases are used in rotary tube furnaces and other heat treatment processes to prevent oxidation or other chemical reactions during high-temperature processing.
- This is essential for materials like metals, ceramics, and composites, which can degrade when exposed to reactive gases at high temperatures.
-
Versatility Across Industries
- Inert gases are used in diverse fields, including chemical manufacturing, food preservation, electronics, and metallurgy.
- Their ability to create stable, non-reactive environments makes them indispensable for ensuring safety, quality, and efficiency in various applications.
By leveraging the unique properties of inert gases, industries can achieve precise control over their processes, ensuring optimal outcomes while minimizing risks and maintaining the integrity of materials and products.
Summary Table:
Advantage | Description |
---|---|
Prevents Unwanted Reactions | Creates oxygen-free environments to avoid oxidation and hydrolysis. |
Reduces Reaction Rates | Slows down chemical reactions, ensuring product quality in sensitive industries. |
Fire and Explosion Prevention | Displaces oxygen to minimize risks in flammable or volatile processes. |
Contamination Control | Reduces airborne particles and moisture, critical in semiconductor manufacturing. |
Enhances Industrial Efficiency | Improves sputtering and deposition rates with high molecular weight gases. |
Heat Treatment Applications | Protects materials from degradation during high-temperature processing. |
Versatility Across Industries | Used in pharmaceuticals, food packaging, electronics, and metallurgy. |
Learn how inert gases can optimize your industrial processes—contact our experts today!