Magnetrons, particularly in applications like sputtering and high-power oscillators, offer a range of advantages that make them highly valuable in various industries. They are known for their high-power output capabilities in both pulsed and continuous wave (CW) modes, making them versatile for different operational needs. In magnetron sputtering, they enable high deposition rates, produce high-purity films, and ensure strong adhesion of coatings, even on heat-sensitive substrates. Additionally, DC magnetrons simplify power delivery, enhance reliability by eliminating impedance matching units, and allow for sequential deposition of materials, making them attractive for equipment builders.
Key Points Explained:
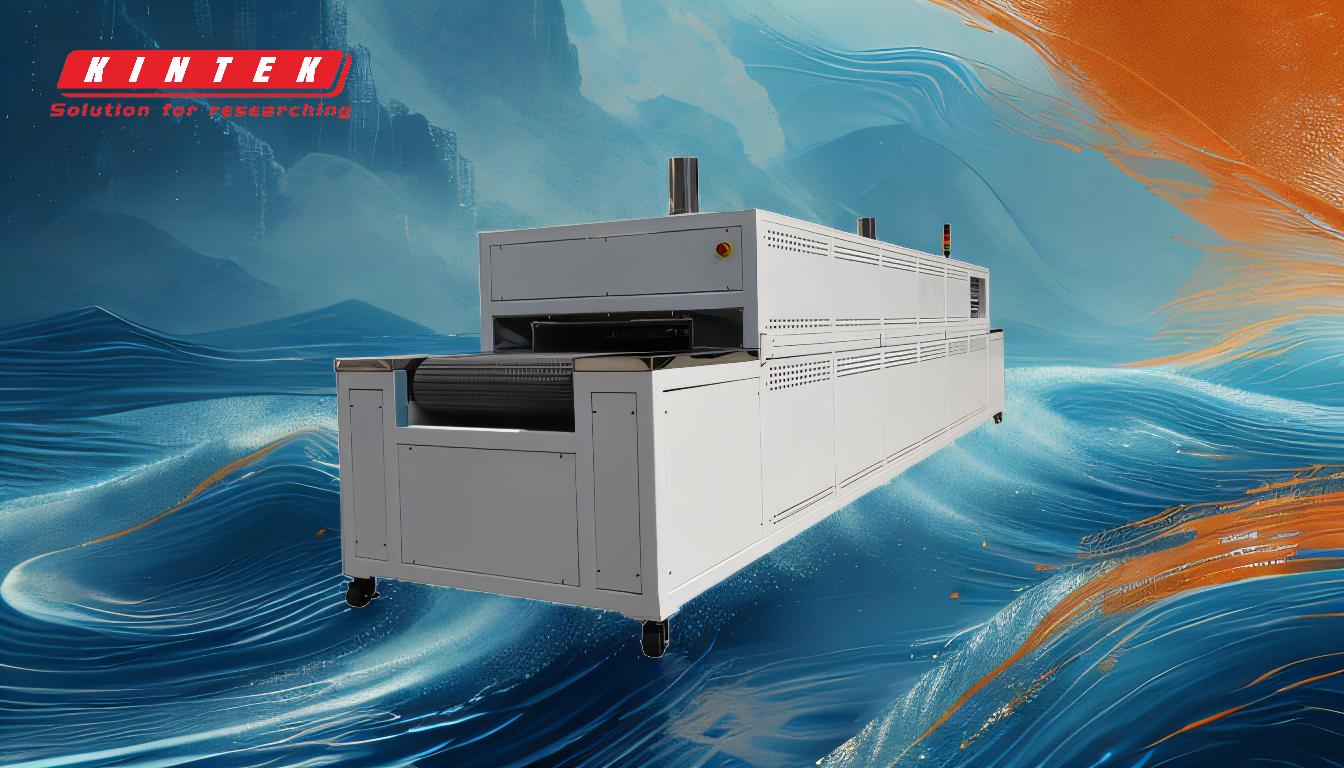
-
High-Power Output in Pulsed and CW Modes:
- Magnetrons are capable of delivering high-power output in both pulsed and continuous wave modes. This versatility makes them suitable for a wide range of applications, from radar systems to industrial coating processes. The ability to operate in different modes ensures flexibility in meeting specific power requirements.
-
High Deposition Rates in Magnetron Sputtering:
- Magnetron sputtering is a high-rate vacuum coating technique that deposits metals, alloys, and compounds onto various materials. The high deposition rates make the process efficient and cost-effective, especially in industrial settings where large-scale coating is required.
-
Ease of Sputtering:
- The process of sputtering with a magnetron is relatively straightforward, which reduces operational complexity. This ease of use is beneficial for both equipment manufacturers and end-users, as it lowers the barrier to entry and simplifies maintenance.
-
High Purity Films:
- Magnetron sputtering produces films with high purity, which is critical in industries like semiconductors and optics where contamination can significantly impact performance. The high purity ensures that the coatings meet stringent quality standards.
-
High Adhesion of Films:
- The films deposited using magnetron sputtering exhibit high adhesion to the substrate. This strong bond is essential for applications where durability and longevity of the coating are important, such as in protective coatings or electronic devices.
-
Coating Heat-Sensitive Substrates:
- Magnetron sputtering can be used to coat heat-sensitive substrates without causing damage. This capability is particularly valuable in industries like electronics and medical devices, where substrates may not withstand high temperatures.
-
Simplified Power Delivery in DC Magnetrons:
- DC magnetrons are simpler in terms of power delivery compared to RF systems. The absence of complex impedance matching units in DC systems enhances reliability and reduces the likelihood of equipment failure, making them more attractive for equipment builders.
-
Sequential Deposition of Materials:
- The output from a single DC magnetron drive can be switched between multiple cathodes, allowing for sequential deposition of different materials. This feature is particularly useful in multi-layer coating applications, where different materials need to be deposited in a specific order.
-
Reliability of DC Systems:
- DC magnetron systems are generally more reliable than RF systems due to the absence of an impedance matching unit. This increased reliability translates to lower maintenance costs and fewer operational disruptions, which is a significant advantage for industrial applications.
By leveraging these advantages, magnetrons, particularly in sputtering applications, provide a robust and efficient solution for high-quality coating and high-power output needs across various industries.
Summary Table:
Advantage | Key Benefit |
---|---|
High-Power Output (Pulsed & CW Modes) | Versatile for radar, industrial coating, and other high-power applications. |
High Deposition Rates | Efficient and cost-effective for large-scale coating processes. |
Ease of Sputtering | Simplifies operation and maintenance, lowering barriers for users. |
High Purity Films | Ensures contamination-free coatings for semiconductors and optics. |
High Adhesion of Films | Provides durable and long-lasting coatings for protective and electronic uses. |
Coating Heat-Sensitive Substrates | Safe for electronics and medical devices without damaging substrates. |
Simplified Power Delivery (DC) | Enhances reliability and reduces equipment failure risks. |
Sequential Deposition of Materials | Enables multi-layer coatings for advanced industrial applications. |
Reliability of DC Systems | Reduces maintenance costs and operational disruptions. |
Ready to enhance your industrial processes with magnetron technology? Contact us today to learn more!