Physical Vapor Deposition (PVD) is a highly advanced coating technology that offers numerous advantages, particularly for metal applications. It is widely recognized for its ability to create durable, corrosion-resistant, and environmentally friendly coatings. PVD coatings are applied in a vacuum environment, ensuring high-quality, long-lasting results. This process is suitable for a wide range of materials and applications, making it a versatile choice for industries requiring high-performance coatings. The key advantages of PVD include exceptional durability, environmental safety, aesthetic flexibility, and the ability to enhance the mechanical and chemical properties of coated materials.
Key Points Explained:
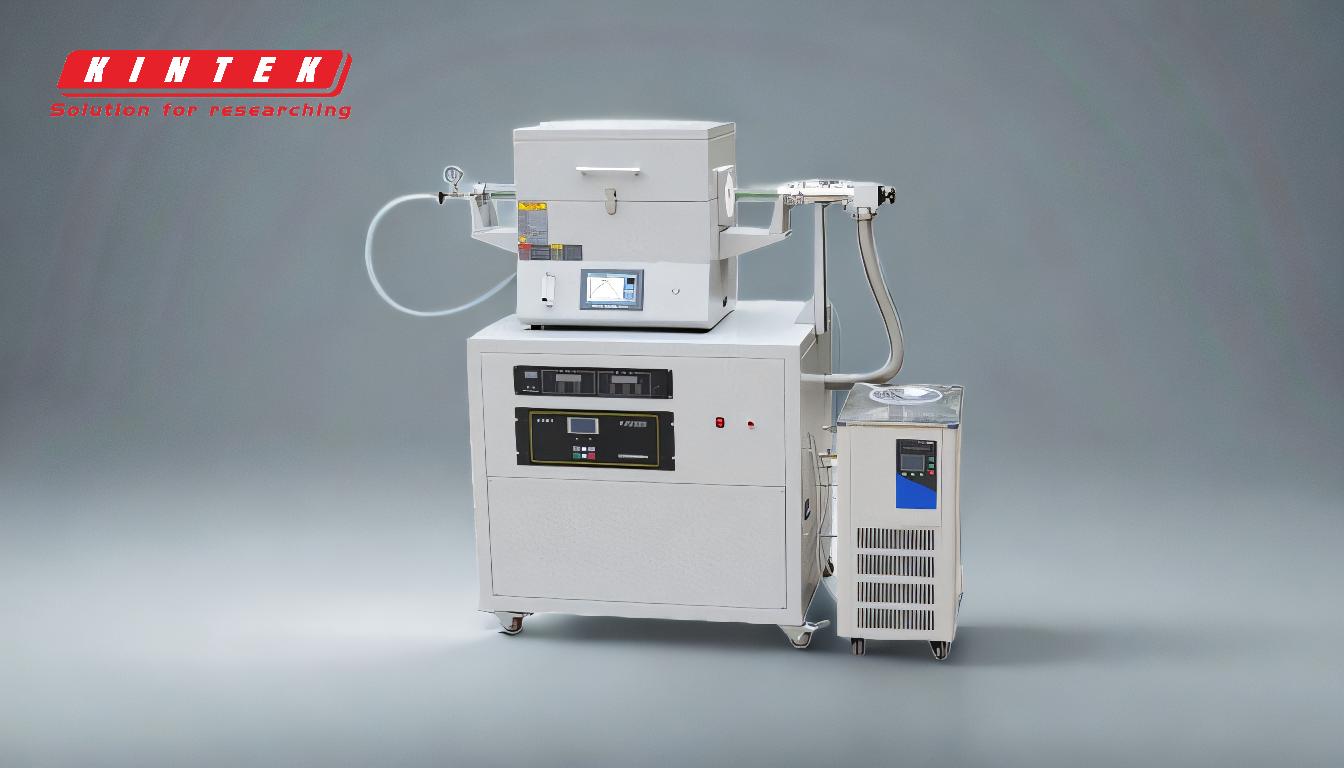
-
Durability and Wear Resistance
- PVD coatings are known for their exceptional durability, making them ideal for applications requiring high wear resistance, friction, hardness, and heat resistance.
- They provide superior abrasion resistance and impact strength, which is particularly beneficial for industrial components subjected to high wear and tear.
- The coatings are long-lasting and rarely require protective topcoats, reducing maintenance costs and extending the lifespan of the coated products.
-
Corrosion Resistance
- PVD coatings offer excellent corrosion resistance, making them suitable for use in corrosive environments.
- This property is critical for industries such as aerospace, automotive, and marine, where components are exposed to harsh conditions.
- The coatings act as a barrier, protecting the substrate material from chemical and environmental degradation.
-
Environmental Friendliness
- PVD is an environmentally friendly process that does not involve the use of hazardous chemicals or produce toxic residues.
- Unlike traditional coating methods like electroplating, PVD does not require extensive cleanups or post-treatments, reducing its environmental impact.
- The coated components are 100% recyclable, contributing to sustainability efforts.
-
Versatility in Material Application
- PVD can be used to deposit almost any type of inorganic material and some organic materials, making it highly versatile.
- It is compatible with a wide range of substrates, including metals, ceramics, and plastics, allowing for diverse applications across industries.
- The process can produce single-material films or complex multilayer coatings with tailored properties.
-
Enhanced Mechanical and Chemical Properties
- PVD coatings improve the hardness, strength, and scratch resistance of components, making them suitable for high-stress applications.
- They enhance the chemical resistance of products, protecting them from degradation due to exposure to chemicals or environmental factors.
- The precise control over coating composition and thickness ensures consistent performance and quality.
-
Aesthetic Flexibility
- PVD coatings allow the texture of the metal to remain visible, offering greater design freedom and new color options.
- This makes PVD an attractive choice for industries where aesthetics are important, such as consumer electronics, jewelry, and architectural applications.
- The coatings provide a brilliant and durable finish, enhancing the visual appeal of products.
-
High-Temperature and Impact Strength
- PVD coatings exhibit high temperature and impact strength, making them suitable for applications in extreme conditions.
- This property is particularly valuable in industries such as aerospace and automotive, where components are exposed to high temperatures and mechanical stress.
-
Sustainability and Recyclability
- PVD is a sustainable coating method that aligns with modern environmental standards.
- The process does not use hazardous substances, and the coated components can be fully recycled, reducing waste and promoting a circular economy.
In summary, PVD offers a comprehensive range of benefits, including durability, corrosion resistance, environmental safety, and aesthetic flexibility. Its ability to enhance the mechanical and chemical properties of materials, combined with its versatility and sustainability, makes it a preferred choice for high-performance applications across various industries.
Summary Table:
Advantage | Key Benefits |
---|---|
Durability and Wear Resistance | Exceptional durability, high wear resistance, and reduced maintenance costs. |
Corrosion Resistance | Protects against harsh environments, ideal for aerospace and marine industries. |
Environmental Friendliness | Eco-friendly process, no hazardous chemicals, and 100% recyclable coatings. |
Versatility in Material Application | Compatible with metals, ceramics, and plastics for diverse applications. |
Enhanced Mechanical Properties | Improves hardness, strength, and scratch resistance for high-stress applications. |
Aesthetic Flexibility | Offers design freedom, new color options, and durable finishes. |
High-Temperature and Impact Strength | Suitable for extreme conditions, including aerospace and automotive industries. |
Sustainability and Recyclability | Aligns with environmental standards and promotes a circular economy. |
Ready to enhance your materials with PVD coatings? Contact us today to learn more!