Muffle furnaces are highly versatile and efficient tools used in various industrial and laboratory settings for high-temperature applications. Their advantages include precise temperature control, uniform heating, and a controlled atmosphere, which protect samples from contamination and reduce oxidation. They are energy-efficient, durable, and designed for safety, with features like rapid heating and cooling, robust construction, and compatibility with different heating media. These furnaces are ideal for processes such as heat treatment, material testing, and scientific research, offering cost-effectiveness, ease of operation, and long service life.
Key Points Explained:
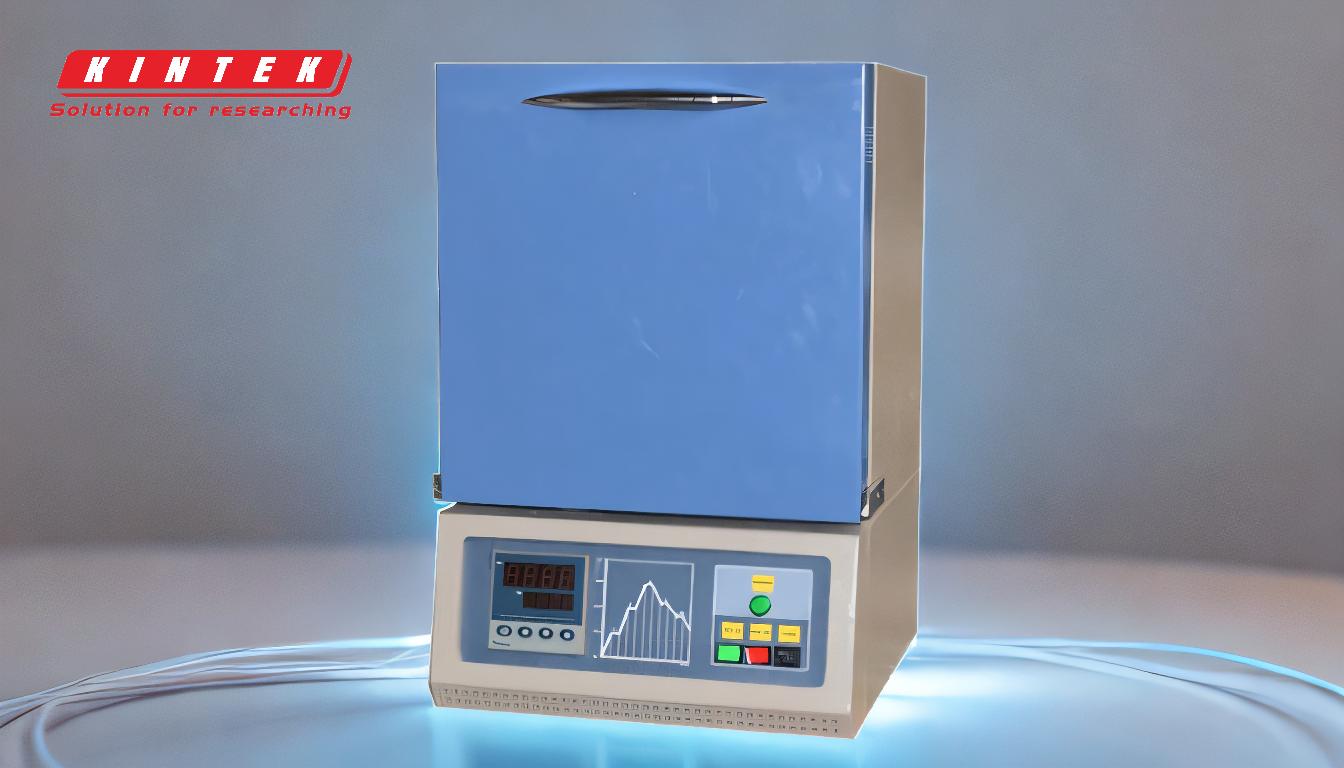
-
Precise Temperature Control
- Muffle furnaces provide exceptional temperature accuracy, allowing users to maintain specific temperatures required for processes like heat treatment, sintering, or material testing.
- This precision ensures consistent results, which is critical in scientific research and industrial applications.
-
Uniform Heating
- The design of muffle furnaces ensures even heat distribution throughout the chamber, eliminating hot spots.
- Uniform heating is essential for processes like annealing, where consistent temperature exposure is necessary to achieve desired material properties.
-
Controlled Atmosphere
- Muffle furnaces can operate in a controlled environment, isolating materials from combustion byproducts.
- This feature is particularly beneficial for processes requiring a vacuum or specific gas atmospheres (e.g., nitrogen or hydrogen), which prevent oxidation or contamination.
-
Protection from Contamination
- The muffle design separates the heating elements from the sample chamber, ensuring that samples are not exposed to direct flames or combustion gases.
- This isolation is crucial for maintaining the purity of materials in applications like ceramics, glass fusing, and metallurgy.
-
Energy Efficiency
- Muffle furnaces are designed with efficient heat insulation, reducing energy consumption while maintaining high temperatures.
- Their ability to retain heat and recover quickly after opening minimizes energy waste, making them cost-effective for long-term use.
-
Durability and Robust Construction
- These furnaces are built with high-quality materials, such as ceramic insulation and refractory linings, which withstand extreme temperatures and harsh conditions.
- Their durable design ensures a long service life, even in demanding industrial environments.
-
Safety Features
- Muffle furnaces are equipped with safety mechanisms, such as over-temperature protection and secure door seals, to prevent accidents and ensure operator safety.
- These features make them reliable for continuous operation in both laboratory and industrial settings.
-
Rapid Heating and Cooling
- Modern muffle furnaces can achieve high temperatures (up to 1,800°C) quickly, often within an hour, and cool down efficiently.
- This capability reduces processing time and increases productivity, especially in high-throughput environments.
-
Versatility in Applications
- Muffle furnaces are compatible with various heating media, including air, hydrogen, and nitrogen, making them suitable for a wide range of materials and processes.
- They are used in industries such as electronics, automotive, and mechanical engineering for tasks like brazing, sintering, and heat treatment.
-
Cost-Effectiveness and Ease of Operation
- With low operation and maintenance costs, muffle furnaces are an economical choice for both small-scale laboratories and large industrial facilities.
- Their user-friendly design and step-type assembling structure simplify installation, operation, and maintenance.
-
High-Temperature Resistance
- Muffle furnaces are capable of withstanding extreme temperatures, making them ideal for processes like glass fusing, metal heat treatment, and advanced scientific applications.
- Their ceramic construction ensures efficient heat retention and durability under prolonged high-temperature use.
-
Humanized Design
- Features like step-type assembling and integral door designs enhance usability and longevity.
- These design elements prevent hearth collapse and extend the lifespan of critical components, such as the door and door frame.
In summary, muffle furnaces offer a combination of precision, durability, and efficiency, making them indispensable tools for high-temperature processes across various industries. Their ability to provide controlled environments, protect samples, and operate cost-effectively ensures their continued relevance in both research and industrial applications.
Summary Table:
Advantage | Description |
---|---|
Precise Temperature Control | Ensures accurate and consistent results for heat treatment and material testing. |
Uniform Heating | Eliminates hot spots, essential for processes like annealing. |
Controlled Atmosphere | Prevents oxidation and contamination with vacuum or gas environments. |
Protection from Contamination | Isolates samples from combustion byproducts, ensuring material purity. |
Energy Efficiency | Reduces energy consumption with efficient heat insulation. |
Durability | Built with high-quality materials for long service life in harsh conditions. |
Safety Features | Includes over-temperature protection and secure door seals for operator safety. |
Rapid Heating/Cooling | Achieves high temperatures quickly and cools efficiently, boosting productivity. |
Versatility | Compatible with air, hydrogen, and nitrogen for diverse applications. |
Cost-Effectiveness | Low operation and maintenance costs for economical long-term use. |
High-Temperature Resistance | Withstands extreme temperatures for advanced scientific and industrial tasks. |
Humanized Design | Step-type assembling and integral door designs enhance usability and longevity. |
Ready to enhance your lab or industrial processes with a muffle furnace? Contact us today to find the perfect solution!