Planetary ball milling offers several advantages that make it a preferred method for material processing in various industries. These advantages include the ability to produce very fine powders with particle sizes as small as 10 microns, suitability for milling toxic and abrasive materials, and the capability for continuous operation. Additionally, planetary ball mills are known for their low energy consumption, ease of cleaning, and minimal maintenance requirements. They also provide a controlled environment that prevents contamination and maintains sterility, making them ideal for sensitive applications. The method is versatile, cost-effective, and capable of producing materials with unique properties, such as crystal defects, which can be beneficial for specific applications.
Key Points Explained:
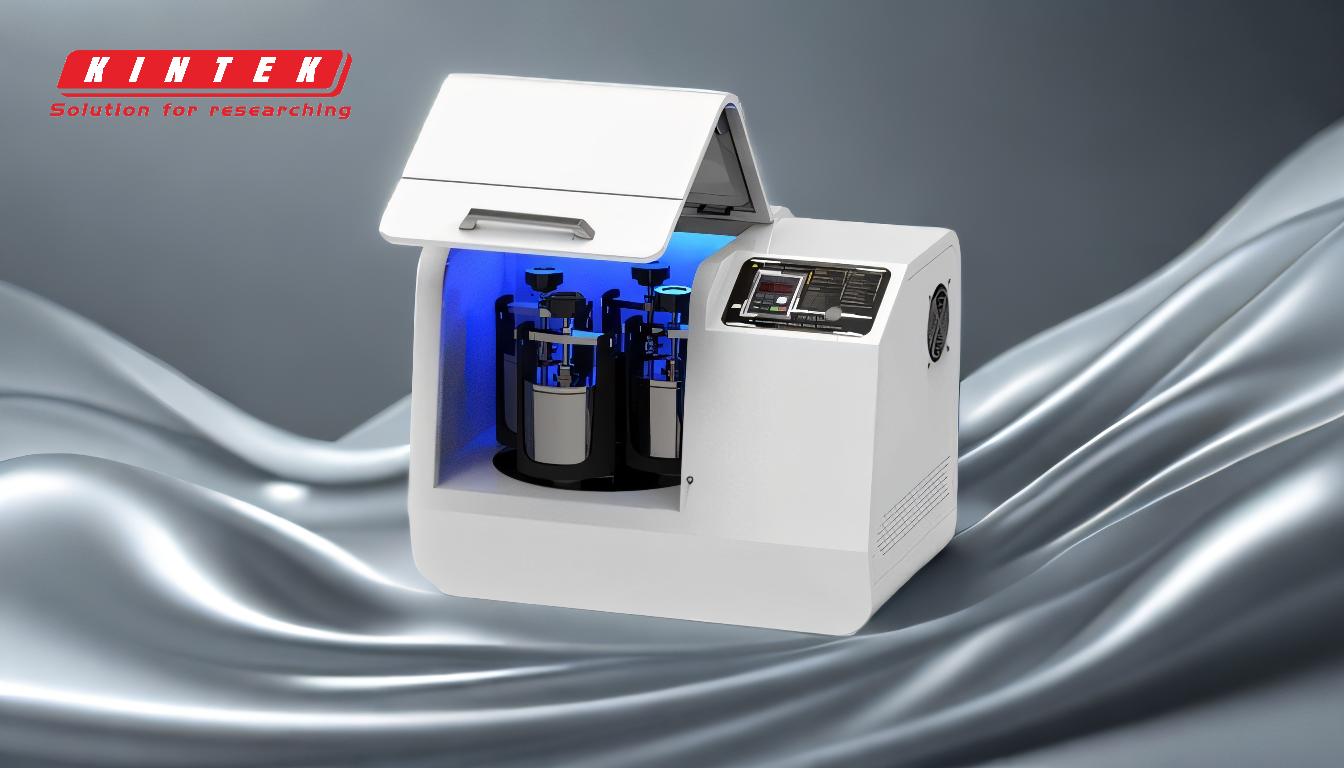
-
Fine Powder Production:
- Planetary ball mills are capable of producing very fine powders with particle sizes less than or equal to 10 microns. This is particularly important in industries where fine particle size is critical, such as pharmaceuticals, ceramics, and advanced materials.
-
Suitability for Toxic and Abrasive Materials:
- The enclosed form of planetary ball mills makes them suitable for milling toxic materials safely. Additionally, they are effective in milling abrasive materials, which can be challenging for other types of mills.
-
Continuous Operation:
- Planetary ball mills can operate continuously, which is beneficial for large-scale production processes. This continuous operation capability ensures a steady output and can improve overall efficiency.
-
Low Energy Consumption:
- Compared to other high-energy mills, planetary ball mills pump very low energy into the material during mixing. This results in lower energy consumption, which can lead to cost savings and reduced environmental impact.
-
Ease of Cleaning and Maintenance:
- Planetary ball mills are designed for easy cleaning and require minimal maintenance. This reduces downtime and ensures that the equipment remains in good working condition over long periods.
-
Sterility and Contamination Control:
- The closed container system of planetary ball mills helps maintain sterility and prevents contamination. This is particularly important in industries such as pharmaceuticals and food processing, where contamination can have serious consequences.
-
Versatility:
- Planetary ball mills are versatile and can be used for both wet and dry grinding processes. This flexibility makes them suitable for a wide range of applications, from material synthesis to particle size reduction.
-
Cost-Effectiveness:
- The ball milling method is generally inexpensive and easy to perform. This makes it an attractive option for both small-scale and large-scale operations.
-
Production of Crystal Defects:
- Planetary ball milling can produce materials with crystal defects, which can be beneficial for certain applications. These defects can enhance the material's properties, such as catalytic activity or mechanical strength.
-
Commercial Viability:
- High-energy ball milling, including planetary ball milling, is commercially viable and widely used in various industries. The ability to reduce impurities using tungsten carbide components and inert atmospheres further enhances its commercial appeal.
In summary, planetary ball milling offers a combination of fine powder production, safety, efficiency, and versatility, making it a valuable tool in material processing and synthesis. Its ability to handle toxic and abrasive materials, along with its low energy consumption and ease of maintenance, further solidifies its position as a preferred method in many industries.
Summary Table:
Advantage | Description |
---|---|
Fine Powder Production | Produces powders with particle sizes ≤ 10 microns, ideal for pharmaceuticals and ceramics. |
Toxic & Abrasive Material Handling | Enclosed design ensures safe milling of toxic and abrasive materials. |
Continuous Operation | Enables steady output for large-scale production, improving efficiency. |
Low Energy Consumption | Reduces energy use, lowering costs and environmental impact. |
Ease of Cleaning & Maintenance | Minimal downtime due to easy cleaning and low maintenance. |
Sterility & Contamination Control | Closed system prevents contamination, crucial for pharmaceuticals and food. |
Versatility | Suitable for both wet and dry grinding, adaptable to various applications. |
Cost-Effectiveness | Affordable and easy to perform, ideal for small and large-scale operations. |
Crystal Defect Production | Enhances material properties like catalytic activity and mechanical strength. |
Commercial Viability | Widely used across industries, with tungsten carbide components reducing impurities. |
Ready to enhance your material processing with planetary ball milling? Contact our experts today to learn more!